While there might be some debate regarding the first person to say “The only thing that is certain in life is death and taxes” (most attribute it to Ben Franklin), it’s obvious they were not talking about the tire business. Among the many certainties are the loss of tread depth, the dependence on natural rubber, the need for correct inflation pressure, and, of course, flat tires.
According to a 1999 report from the AAA Foundation for Traffic Safety, 60% of the drivers surveyed experienced a flat tire in the previous five years, and the most common cause was punctures (75%).
But anyone with more than a few years of experience in the industry does not need a 15-year-old study to know that flat tires are common. And it also isn’t a surprise that according to the same AAA report, frequent drivers (10,000 miles or more annually) have a better chance of getting a flat tire when compared to those who drive less (64% vs. 54%).
In contrast, the frequency of flat tires in the trucking industry has more to do with the application than the number of miles traveled.
As long as tires have relied on inflation pressure, problems associated with punctures and other damage that results in the loss of air have existed. From the old days of inner tube repairs and hot patches to modern, chemically vulcanized patch/plug combinations, technology has made it much easier to safely return a flat tire to service. That’s a good thing: The liability associated with repairing tires has increased since the landmark Barber v. Mossy Ford case — and its subsequent $22.8 million combined wrongful death verdict and settlement.
In some cases, the risks have led retailers and commercial tire dealers to establish strict guidelines, while in others, the businesses have eliminated tire repair altogether. Unfortunately, there are still far too many companies that, in my opinion, continue to put lives in jeopardy because they are either uninformed or just want to gain a competitive edge by offering cheap tire repairs that are not consistent with the best practices established by the industry.
Consumer tire repair
The Tire Industry Association (TIA) has been conducting a national training tour for the last few years to educate people on all aspects of passenger and light truck tire service, including repair. These classes are typically held at local community and technical colleges. We have found most of the schools do not have the tools, equipment or supplies to teach the proper method for repairing tires. The good news is that almost all of them have seen the error in their ways and are now teaching the correct repair procedures.
Even though there is universal agreement regarding the steps and guidelines for repairing tires, there are still a few issues that need to be addressed. Most of them are related to the elimination of the spare tire.
On vehicles with run-flat tires, the guidelines are the same, although the manufacturer may place limitations on the criteria or the number of repairs. For example, Goodyear does not have any restrictions regarding the repair of a run-flat versus any other tire. Michelin only allows one repair on run-flats, while Bridgestone, Continental, Pirelli and Yokohama do not recommend repairing them at all.
Another trend that is impacting the tire repair industry is the use of temporary mobility kits on new vehicles. Some manufacturers are replacing the spare tire with a portable air pump that includes sealant to stop the air leak.
In most cases, the sealant contains ethylene glycol or propylene glycol, both of which are primary components of antifreeze. Many states classify compounds in the glycol family as hazardous waste; therefore, the disposal of the sealant material may be regulated (because propylene glycol is less toxic than ethylene, states may handle it differently).
I am not aware of any specific regulations regarding the disposal of glycol-based tire sealants. So what should you do with them? The answer to that question may lie in how states legally discard antifreeze.
In a September 2008 document from the Michigan Department of Environmental Quality, lawmakers indicated it is acceptable to wash antifreeze down the drain only if it is connected to the municipal wastewater treatment facility, and if permission has been obtained from the sewer authority. They also recommend getting the permission in writing. Antifreeze cannot be discharged into storm drains, on the ground, or into a drain that leads to a septic system.
A November 2013 publication from the Wisconsin Department of Natural Resources mirrors the Michigan guidelines. And the California Integrated Waste Management Board clearly indicates that it is illegal to dispose of antifreeze by throwing it in the trash or dumping it down storm drains. California also does not include the option of using the municipal wastewater system.
The best practice would be to contact your hazardous waste recycler to see if glycol-based sealant materials can be combined with antifreeze, or if they must be stored in separate containers. Disposing of any glycol products in storm sewers or septic systems is probably illegal (and not very environmentally responsible). It may, however, be acceptable to wash them down the drain for processing at the local wastewater plant.
On the legislative front, it appears that efforts to introduce any laws mandating proper tire repair have diminished. I testified in support of tire repair legislation in Maryland and attempted to educate the committee on the dangers of on-the-wheel plug repairs. Unfortunately, quite a few legislators in the room were driving on tires they had plugged at the local service station. Since they weren’t having any problems, they didn’t see the need for a law that would make them illegal. Regardless, repairing a tire on the wheel with a plug is still a tremendous liability concern for the company making the repair, so TIA strongly discourages the practice with or without legislation.
[PAGEBREAK]
Truck tire repair
Truck tire dealers recently benefitted from the introduction of the reinforced shoulder repair, or RSR. In the past, puncture (or nail hole) repairs, defined as 3/8-inch or smaller, were restricted to the crown area of the tire, which is the center of the tread approximately 1 to 1.5 inches from each shoulder. All injuries in the shoulder or sidewall were previously referred to a retread plant for a section repair.
While injuries in the sidewall are still in need of a section repair, small “injuries” that are 5/16-inch (8 mm) or less in the shoulder can be repaired in the field using the RSR guidelines established by the Tread Rubber and Tire Repair Materials Manufacturers’ Group, or TRMG.
Basically, the RSR uses the same procedures as a standard puncture repair in the crown. The biggest difference is that a larger repair unit is required so the reinforcing plies of the patch do not end in the flex zone of the tire. Depending on the tire, technicians must use a No. 22, 24 or 26 repair unit that will extend past the flex zone so it is anchored on the lower sidewall.
In a departure from previous tire repair practices, the injury is not centered on the patch. By offsetting the repair unit, technicians can accomplish the goal of reinforcing the area around the injury while ensuring the end of the plies is not located in the flex zone of the sidewall. Most tire repair material manufacturers have created a series of templates that make it easy to determine where the repair unit must be located in relation to the injury and the sidewall.
TIA recently developed a video in cooperation with TRMG and filmed the RSR process at Tech International’s new training facility in Johnstown, Ohio. The RSR procedures will be part of the planned update to the association’s highly successful Commercial Tire Service (CTS) Program that is scheduled for 2015.
Tire repair has always been a key component of the Certified CTS training, so the addition of the RSR will make it even more effective. All of the Certified CTS Instructors will receive a copy this fall.
Drill, fill, patch and bill
The basic principles of proper tire repair haven’t changed much in the 32-plus years that I’ve been in the industry. Over the last 18 years as an educator, my mantra has been “drill it, fill it, patch it, bill it.”
Drilling the injury is important because the damaged material must be removed. Filling the injury prevents moisture from entering the body of the casing and causing corrosion that leads to separations. Patching the injury prevents air from escaping the interior of the tire and reinforces the area. And, of course, billing for the work keeps you in business, because it takes a substantial investment in tools, equipment and materials to properly repair tires. I believe when people receive anything for free, it becomes devalued in their mind, and its level of importance is diminished.
Despite the narrow-minded opinions of legislators who are unwilling to recognize the dangers that improper (including on-the-wheel) tire repairs create for motorists, it’s important that the industry continues to emphasize the need to demount the tire from the rim so it can be inspected before following the guidelines. After the tire passes inspection and the trained technician determines it is repairable, then the proper procedures can be followed to safely return it to service.
The message appears to be getting through: More retailers are abandoning the on-the-wheel plug and patch-only methods in favor of the process that has been universally endorsed by the tire companies and industry organizations for decades.
While I seriously doubt that improper tire repair will ever completely disappear, I’m optimistic that the progress we’ve made as an industry is a sign that accidents like the one that claimed the lives of the Barbers will be few and far between. ■
Kevin Rohlwing is the Tire Industry Association’s senior vice president of training and a frequent Modern Tire Dealer contributor.
About the Author
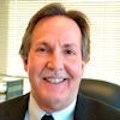
Bob Ulrich
Bob Ulrich was named Modern Tire Dealer editor in August 2000 and retired in January 2020. He joined the magazine in 1985 as assistant editor, and had been responsible for gathering statistical information for MTD's "Facts Issue" since 1993. He won numerous awards for editorial and feature writing, including five gold medals from the International Automotive Media Association. Bob earned a B.A. in English literature from Ohio Northern University and has a law degree from the University of Akron.