Where will its next automated tire plant be built? Halfway around the world, Kumho eyes the U.S.
Kumho Tire Co. Inc. manufactures between 36 and 38 million tires a year at its three ISO-certified plants in South Korea. It´s the smallest of the three, however, that excites the company and its new president the most.
The company´s APU (Automated Production Unit) in Pyongtaek, Kyungki-do (in photo), opened less than a year ago, 15 months from its groundbreaking. It can produce two million passenger and light truck tires annually; the plant runs 24/7, 350 days a year, with a workforce of 174 people.
That factors out to roughly 11,500 tires per employee annually. By comparison, Kumho´s plants in Koksung and Kwangju total 2,267 and 3,129 workers, respectively. Koksung employees turn out an estimated 7,500 tires each, while Kwangju personnel turn out 5,450 each.
Auto-mated
Dr. Sae-Chul Oh, who took over as CEO and president of Kumho Tire Co. at the beginning of the year, continues to make use of his chemical engineering degree. He spends his weekdays in Seoul supervising the company, but returns to the Pyongtaek plant on weekends.
Oh says he is looking at opening another APU outside Korea, and admits that the United States and Europe are two possibilities.
The majority, up to 80%, of the automated plant´s capacity is targeted for original equipment in Asia. There are three automobile factories near the Pyongtaek plant: Hyundai Motor Co., Kia Motors Corp. and GM Daewoo. All are tire customers of Kumho.
Kumho wants OE contracts in the U.S., so opening an APU there might help the company reach that goal. The new Hyundai manufacturing facility in Montgomery, Ala., is an attractive lure. (Kumho has OE ties to Volkswagen AG in Europe.).
But Kumho has limited plant capacity, according to J.H. Kim, executive vice president of sales and marketing. "We have very tight capacity. So we take care (of our OE customers) only in Korea."
Kim says he recently met with General Motors Corp., but had to admit he couldn´t produce large enough quantities needed by the world´s biggest vehicle manufacturer.
Joint ventures or off-take arrangements with other tire manufacturers are a possibility, he says.
[PAGEBREAK]
Kumho also supplies almost all of the vehicle manufacturers in China, helped by its Nanjing, China, facility. The company hopes to more than double the plant´s five million tire capacity by 2007 to meet growing demand. A second plant in China also may be necessary. "(China is) not a big market yet for us," says Kim.
Oh´s goal is an overall capacity increase of at least 3% every year.
Proprietary technology
The key to the Pyongtaek manufacturing facility is the way Kumho consolidated some steps and eliminated others. There are nine independent tire-making processes -- which Oh says he is always trying to modify. They not only speed up the process -- it takes 48 seconds to build a green tire in the APU -- but also increases tire uniformity.
For example, Kumho extrudes the tread rubber at a reduced speed, which lowers the required temperature and results in less rubber degradation.
Investment cost in the APU, which took 15 to 20 months to build, was 70% less than a traditional plant. Oh says it would take longer to build such a plant in the U.S.
"We´d like to share our technical know-how with other countries," says Oh. However, APU technology is proprietary.
Healthy, if not wealthy
Kumho recorded $1.3 billion in sales in 2003. Exports represented $830 million, or roughly 64%, of total sales. Sales in North America accounted for close to $365 million -- $305 million in the United States alone.
Only $17-20 million came from Mexico, in part because of the very high duties Mexico places on imported tires.
The tire group received an infusion of cash in April 2003 when Kumho Industrial Co. Ltd. sold 50% of its tire business to the South Korean Military Mutual Aid Association (MMMA) and 20% to other investors, mainly suppliers.
Talks with Groupe Michelin and Pirelli & Cie SpA fell through when they wanted too much control. According to Kim, the military leaves management of the company in the hands of Kumho executives. It just wants a return on its investment, which was estimated at 10% last year.
According to a recent The Korea Times article, South Korea "is losing global competitiveness in manufacturing due to a reduction in investment, according to a report from a state-run research institute (the Korea Development Institute (KDI)."
The KDI says U.S. investment in machinery and equipment has risen from 9.3% of GDP between 1993-1997 to 12.3% between 1998-2002; Japan rose from 12.6% to 13.5% over the same period.
South Korea is down from 13.8% to 11.2%. The rate of Kumho´s investment in machinery and equipment was 9.2% in 2003.
On the horizon
The Korean Times also reported that the Korea Listed Companies Association (KLCA) said Korea "lagged behind the U.S., Japan and Germany in the ratio of the average research and development expenditure against total sales" (for listed companies). KLCA said South Korean companies spent 2.09% of overall sales on R&D in 2003, which places them behind the U.S. and Germany (4% each) and Japan (3.9%).
Kumho´s R&D expenditure against total sales was 3.05% in 2003.
Oh says he would like to focus R&D on new concept tires. "To survive, we have to develop high value-added tires, especially new concept tires. That´s very important for the company."
He says Kumho has been working on a number of ideas, including run-flat technology (without tire pressure monitoring systems) and fuel efficient tires (weighing as little as possible).
[PAGEBREAK]
"We can´t be a leader in the worldwide market. But we can be a fast follower. In niche markets we can be a leader."
In addition to consumer tires, Kumho manufactures truck tires, including super single radial tires. However, a 50-series super single truck tire from Kumho is still two years away.
"We don´t want to be the biggest company in the world," says Kim, "but we want to be the (most) profitable."
Kumho hopes to top $1.5 billion in sales in 2004. "It all depends on the exchange rate," he adds.
Everybody´s doing it: Automated plants are the wave of the present
Kumho Tire Co. Inc. is one of many tire manufacturers attempting to automate the tire manufacturing process (see list below). Although their technology is not always open to outsiders, almost all of them claim it improves tire uniformity and makes the tire production process more flexible.
Groupe Michelin: C3M (for "Carcasse, Monofil, Moulage, Mecanique" in French and "Mechanically molded single-cord cover" in English) features a single manufacturing "phase" instead of the standard seven and an integrated curing press. There are C3M plants, which take up relatively little space, in North America (Greenville, S.C.), South America and Europe.
Pirelli & Cie SpA: Modular Integrated Robotized System (MIRS) reduces the average tire production cycle from 14 steps to three automated steps, and can economically accommodate small runs. Pirelli Tire North America runs a MIRS plant in Rome, Ga.
Goodyear Tire & Rubber Co.: Integrated Manufacturing, Precision Assembly Cellular Technology (IMPACT) "integrates component formation and assembly, automated tire assembly and curing within a cellular system," according to the company.
Sumitomo Rubber Industries Ltd.: "Taiyo" is a fully automated tire production system that integrates production processes from component preparation to tire curing in one compact cell.
Continental AG: Modular Manufacturing Process (MMP) produces small runs economically.
Bridgestone Corp.: Bridgestone Innovative and Rational Development (BIRD) automates tire production through the inspection process. The company says it plans to refine the system "under mass production conditions," although it is designed to produce multiple sizes of tire simultaneously.
Yokohama Rubber Co. Ltd.: New Manufacturing System, which boasts "small lot production of diverse models."
About the Author
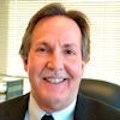
Bob Ulrich
Bob Ulrich was named Modern Tire Dealer editor in August 2000 and retired in January 2020. He joined the magazine in 1985 as assistant editor, and had been responsible for gathering statistical information for MTD's "Facts Issue" since 1993. He won numerous awards for editorial and feature writing, including five gold medals from the International Automotive Media Association. Bob earned a B.A. in English literature from Ohio Northern University and has a law degree from the University of Akron.