In too many cases, the importance of properly mounting custom alloy wheels and high performance tires takes a backseat to the sales process. Customers don´t always realize that the hard work begins after their selection.
Unfortunately, it´s still not uncommon for the mounting procedure to be treated in a routine and perhaps hasty manner in some shops. As seasoned technicians will tell you, this is not the approach to follow!
We realize that not all installers take this view, but enough mishandling is occurring in the marketplace to warrant a close look at this issue.
Care and attention to detail is important for two primary reasons: to prevent cosmetic damage to the wheel, and to prevent critical (functional) damage to both the tire and wheel. In addition, proper care during mounting will assure proper bead seating to minimize the risk of air leakage, and can directly affect the dynamic balance scenario.
[PAGEBREAK]
APPEARANCE
When installing a tire and wheel assembly, reasonable care should be exercised to prevent scratches or gouges on the wheel surfaces. This is extremely critical when dealing with high-dollar custom alloys and low-profile performance rubber. Whether a customer spends $129 per wheel or $1,000 per wheel, he or she deserves a final assembled and installed package minus torn beads, improperly oriented tires (we´ll touch on this later in this article), scratches and gouges on the wheel, etc.
After mounting, balancing and installation, take the time to carefully clean the wheels, removing any smudges, fingerprints, traces of mounting lubricant, etc. Also clean the tires, removing any smudges, protective film on white letters, etc.
Finally, pay attention to the installed appearance on the vehicle. By that, we´re referring to what you can see when the package is installed -- items such as brake calipers, rotors and wheelwells.
Of course, you´ll need to discuss any corrective work of this type with the customer, but the point that we´re trying to make is to never blindly accept the installed appearance when, say, a rusty or dirty caliper is visible behind a custom wheel. Alerting the customer to options that will enhance the appearance of the installed package can lead to increased sales.
For instance, the OE calipers may be cleaned and coated with a special high-heat paint specifically designed for brake caliper applications. Or, the customer may be agreeable to replacing the OE brake setup with new performance aftermarket calipers and rotors.
Today´s performance brake system manufacturers offer a great selection of caliper bodies that feature attractive design shapes and plated, anodized or specialty-coated bodies. Enthusiasts may be attracted to performance rotors that feature drilled or slotted discs. So don´t assume that you can´t do anything to alleviate an existing boring or cruddy brake component.
MOUNTING THE TIRE TO THE WHEEL
Before attempting the mount, verify that the tire size (diameter and width) is correct for the wheel at hand. This may sound basic, but catastrophic damage can result from attempting a mismatched assembly.
Make sure that both the wheel and tire are clean. This is especially important if either component has previously been used. Today´s high performance tires feature relatively stiff bead areas that simply won´t tolerate contaminants such as old rubber particles, dirt, etc., at the seating area. Also, burrs or gouges on the wheel´s rim or bead seat areas may cause severe damage to the new tire bead during mounting, may create an air leak path, or both. Always check the wheel (even if new) for cleanliness and a consistent, smooth bead flange wall and seat area.
Clean the tire changer! We can´t stress this enough. Trying to mount a beautiful performance tire onto a yummy alloy wheel on a dirty, rotten, filthy changer is asking for trouble. It´s like performing eye surgery wearing crud-laden, stinky work gloves. Cleanliness is paramount in order to avoid scratching the wheel or depositing contaminants on the bead area. Every area of the changer that contacts the wheel (and tire) must be clean and free of foreign deposits and burrs.
Also, before mounting, always install a new air valve. Of course, a new wheel will require a valve, but don´t be tempted to install a used valve. A used wheel already may feature a valve that appears to be OK, but don´t make this assumption. When you send a vehicle out of the shop with a fresh set of tires or a tire/wheel combo, always install new air valves. There´s no sense in taking a chance of an air leak in an attempt to save a couple of bucks.
Regarding air valve selection, do not assume that any bland-looking black rubber valve will be acceptable to every customer. When you sell the tires and/or wheels, make a point of asking the customer if he or she has a preference for black rubber, metal-shrouded rubber, or a threaded modular stainless steel valve. In some cases, the customer won´t care. In other cases, the customer may be adamant about using a specific style. And in yet other cases, the customer might not be aware that an option beyond black rubber even exists.
If you´re dealing in high performance wheels and tires, you should offer this option and have various style valves available (either in stock or at immediate access). After all, why should the customer settle for a boring black valve when a satin-finished or polished stainless steel (or chromed) valve might enhance or compliment the selected custom wheel?
[PAGEBREAK]
While we´re discussing valves, it should be noted that the task of installing a new valve onto a wheel is a job that deserves as much care and attention as tire mounting itself.
1. Make sure the valve hole in the wheel is clean, free of any debris.
2. Consider using a valve installer tool when dealing with any aftermarket chrome steel or alloy wheel. The tool allows you to take advantage of leverage by resting the tool handle on the wheel rim edge when pulling the valve through the hole.
3. Pad the rim where the tool handle will make contact to avoid marring the rim surface. Some installers apply a buildup of tape on the tool handle as a mater of course.
However you decide to tackle this issue, pay attention and never apply the bare steel tool handle directly onto the plated, painted or powder-coated rim edge. The best tool is a straight-pull-type that never touches the wheel.
CHECK SIZES AND DIRECTION
Before attempting to mount the tire onto the wheel, first take the time to inspect both parts. Check to see if the tire is directional, in which case it only can be mounted in one direction of forward rotation. If the tires feature directional tread, first organize the tires as they will be positioned on the vehicle (left side tires and right side tires).
Also check to see if the tires are designed with dedicated outboard/inboard location. The sidewall may be marked "OUT" or "OUTSIDE," etc. The tire may feature outboard shoulder tread designed for better grip on dry road, while the inboard shoulder tread may feature increased void ratio for better wet grip. Pay attention to tire orientation.
MATCH-MOUNTING
Also inspect both the tires and wheels for any match-mounting labels.
Two methods of match-mounting are available: weight (balance) and uniformity (radial runout).
A yellow dot on the tire indicates the tire´s point of least weight, which should be matched to the wheel´s heaviest weight point. A red dot on the tire indicates the tire´s point of maximum runout ("high" point), which should be aligned with the wheel´s point of minimum runout. If the wheel is not marked for runout, or if you don´t plan to measure wheel runout, at the very least mount the tire while aligning the red dot to the wheel valve location, which will likely be the wheel´s minimum runout point.
RFV (radial force variation, which can be the source of a vibration complaint) can be minimized by phase matching the wheel and tire. This phase matching allows you to align the tire´s point of maximum RFV with the wheel´s point of minimum radial runout. Maximum RFV is generally indicated on the tire by a small red dot. This red dot should be aligned with the wheel´s minimal runout point, sometimes labeled on the wheel with a small white dot.
On alloy wheels that don´t feature a white dot, the valve stem area can be aligned with the red dot, since this should be the wheel´s area of minimum runout. If in doubt, you can locate the wheel´s minimum radial runout point by mounting the wheel to a balancer hub and slowly rotating the wheel while measuring runout with a solid-mounted dial indicator.
If you opt to mount the wheel to the vehicle hub to rotate and check runout, make sure that you then dedicate that wheel to that specific hub location (since you´re now including any potential hub runout into the equation).
In addition to RFV phase matching, you can reduce or possibly eliminate the need for balance weights by weight-matching the tire to the wheel. A yellow dot on the tire will indicate the point of that tire´s least weight. This can be aligned to the wheel´s point of heaviest weight (this may be marked on the wheel or can be determined by first balance-checking the bare wheel). If you have a choice between phase-matching and weight matching, it´s better to phase-match, since imbalance can be addressed by add-on weights.
[PAGEBREAK]
INFLATING
In general, never exceed 40 psi when seating beads. This recommendation may vary when dealing with run-flat tires (which may require higher seating pressure), so always check the tiremaker´s specific recommendations. In most cases, if the beads won´t seat at 40 psi, something´s wrong.
Don´t be tempted to over-inflate in order to "force" the seating. After initial tire inflation results in bead seating, deflate the tire to zero, and re-inflate to the recommended inflation pressure. Apply a bit of water, or soapy water, to the bead area where the tire meets the rim. While re-inflating (or after fully inflated), carefully examine the entire bead circumference to check for air bubbles. This deflation/re-inflation step allows any trapped air pockets to work their way out of the bead seat area. Trapped air pockets can result in an uneven mounting position of the tire -- potentially leading to a slight initial runout condition.
Before installing the package onto the vehicle, make sure that inflation pressure is set at the recommended level. Also, following a test drive (allowing the tire beads to "find their home"), re-check cold inflation pressure to verify a leak-free assembly.
Never use petroleum or silicon-based lubricants. Also, excessive lubricant can cause the beads to slip on the rim.
DEMOUNTING
Never use sharp tools or any type of impact device (hammer, etc.) to unseat beads. Make sure that the bead breaker (whether a shovel-type mounted on the side of the changer or a roller-type that´s built into the arm) is clean. Burrs on the bead breaker or dirt/debris easily can cause scratching or gouging of the wheel rim lip. Once the beads are freed from the wheel´s bead seats, lube both front and rear tire beads to provide needed lubricity and to avoid both bead damage and wheel rim damage.
CHECK THE WHEEL FIT
Never assume that you´ve received the correct wheel for any given vehicle application. Before going through the time and effort to mount the tires onto the wheels, test-fit each wheel onto the vehicle to verify that the bolt pattern is correct, and that the rim clears the suspension/brakes. Also make sure that the wheel fits flush to the mounting surface.
NOTE: OE hubs may feature lock washers (used during factory assembly) at one of the stud locations at each hub. While OE wheels feature a chamfer or relief on the wheel mounting face to clear this washer, the aftermarket wheel might not feature this chamfer. If the wheel´s holes are not chamfered, the washer won´t allow flush mating, resulting in axial runout (wobble). Remove the retaining washers as needed.
Shipping mistakes may not occur often, but it´s best not to assume anything. While an unmounted, mark-free wheel may be returned/exchanged with relative ease, a wheel that already has been fitted with a tire and weights may pose a difficulty if a return is needed. For this reason, make sure that the hub face is clean and free of rust and contaminants before the test-fitting or final installation of any wheel. Also make sure that all wheel studs (if applicable) are clean.
If the wheel does not fit flush with the hub mounting surface, look for obstructions such as spring clip retainers, drum balancing weights, drum rivets, etc.
Also, it´s always a good idea to check a new or used wheel for excess runout. This can be done by temporarily installing the wheel (with three fasteners finger-tight) onto the hub, and slowly rotating the wheel 360 degrees to check for radial and axial runout. If runout is suspected, it can be measured with the use of a dial indicator. While it may add a few minutes to the job, it´s best to verify wheel fit and condition before mounting the tire.
Two styles of center caps (if used) include the type that pops into place from the outside of the center, and the type that is inserted from behind the wheel hub face. If the caps are to be inserted from the rear, make sure that the cap flange matches the wheel´s center hole chamfer and is below the wheel´s mounting surface. If the cap protrudes beyond the mounting surface, it will create an obstruction that won´t allow flush seating of the wheel to the hub, resulting in false torque value readings.
[PAGEBREAK]
Always install any wheel by tightening the fasteners in a crisscross pattern in order to provide even clamping loads. Uneven tightening easily can result in a distorted hub or wheel, leading to vibration complaints and brake pedal-bounce complaints.
Also, after mounting one tire/wheel, test fit the assembly onto the vehicle. With the vehicle on the lift, check for clearance between the fender, suspension and brake components and the tire/wheel in a straight-ahead position and during full turns (lock-to-lock) in each direction. This is especially important when an upgrade has been performed and tire section width and/or wheel offset and backspace has changed vs. the OE setup.
Next, lower the vehicle in order to compress the suspension, and repeat the clearance inspection (have a helper bounce the vehicle as well, to further inspect for clearance issues). It´s better to discover an interference problem at this point as compared to after all four wheels/tires have been mounted, balanced and installed.
WHEEL FASTENER TIGHTENING
Always follow the torque value supplied by the wheel maker. If this isn´t available, follow the OE specs. Following is a common range of torque values for various fastener diameters.
7/16": 70-80 ft.-lbs.
1/2": 75-85 ft.-lbs.
9/16": 105-115 ft.-lbs.
10mm: 45-55 ft.-lbs.
12mm: 70-80 ft.-lbs.
14mm: 85-90 ft.-lbs.
This list is an example only. For example, the 9/16-inch fastener diameter listed above may have a torque value of 135-145 ft.-lbs. depending on the application.
Torque values are based primarily on the stretch and below-yield points of specific fasteners based on shank diameter, thread pitch and material, but they also can be influenced by the "compressibility" of the wheel hub material. Never assume that any torque value is correct by playing guessing games. And always adhere to torque values specified by the wheel or vehicle manufacturer.
CHECK FASTENER SIZE AND STYLE
Also, always verify that you have the correct wheel fasteners for the job at hand. Whether using nuts or wheel bolts, make sure that the thread size is correct (shank diameter and thread pitch), and make absolutely sure that the fastener´s seat style matches that of the wheels.
Using an incorrect seat style will prevent secure clamping of the wheel to the hub, and will result in loosening during operation. Never assume that the fasteners match the wheels. Again, packing/shipping mistakes are possible, so never blindly assume that what you have is correct.
Also, be sure to verify that the fasteners have been correctly packaged. Although it doesn´t happen often, it is possible to find that the fasteners have been improperly boxed (a set of 12mm x 1.5 nuts boxed and labeled as 7/16-inch x 20, for example).
Wheel fastener seat styles include 60-degree taper/conical seats, radius/spherical/ball seats or mag-style straight shank with washers. Never mismatch by using a mag/shank type fastener on a wheel intended for a conical seat, or any other mismatch. Only the correct matching-type seat will provide the required wheel clamping. This cannot be over-emphasized. The use of incorrect seat styles not only can result in wheel damage, but also can lead to a tragic accident if the wheel either loosens or leaves the vehicle.
Also make sure that the fastener does not bottom-out internally. This will prevent full clamping force, resulting in wheel wobble and almost-certain failure of the threaded studs.
In some cases, the wheel´s bolt holes may be small in diameter and deep (in a design effort to "hide" the fasteners from view). In these cases, you may find it difficult to locate a deepwell socket that will clear the wheel´s hole recesses. Especially intended for these wheels (often referred to as "tuner" wheels), special small-diameter nuts that feature a female hex drive or a special splined drive socket may be required.
In these cases, a dedicated spline-drive socket likely will be included with the nuts.
A side benefit of these splined (or female hex) drive styles lies in the fact that most wheel thieves may not have hex bits or spline drive sockets in their burglary arsenal, and may pass on the attempt to pilfer the wheels as a result.
Although a fastener drive type other than a male hex may hinder theft, the best approach to deter would-be felons is to install a set of "wheel locks" that require a unique key drive.
Refer to the article in this issue that addresses wheel dimensions for more information on fasteners.
Wheel fastener threads must be clean and in good condition. Do not lubricate threads unless specifically instructed to do so by the vehicle manufacturer. Torque values are commonly specified based on the use of dry threads. The use of lubricants will result in over-clamping the fasteners if OE torque specs are followed.
[PAGEBREAK]
CHECK WHEEL CENTERING
Wheels are designed to center onto the vehicle hubs by one of two methods: lug-centricity or hub-centricity.
A lug-centric wheel relies on centering via the fastener locations only. As the lug nuts (or wheel bolts) are tightened, the wheel is centered onto the hub. This requires precise location of both wheel bolt holes and the fastener locations on the hub.
A hub-centric wheel is centered onto the hub via the fit of the wheel center hole at the hub face. The hub face will feature a center lip that engages into a recess on the wheel´s hub face. Hub-centric designs more precisely locate the wheel onto the hub in an effort to minimize the chance for installed-radial-runout.
It´s important to recognize which type of centering you have. If the hub design calls for a hub-centric mounting, take a close look at both the wheel´s hub face and the vehicle´s hub face itself. In some cases, the wheel´s centering hole is precisely machined to fit the hub center flange lip.
A hub-centric ring adapter is used to attain a proper fit when the wheels at hand feature a larger center hole (which makes the wheel adaptable to various hub center fitments).
Make sure there are no old adapter ring has stuck to the hub. If this ring is not the correct size for the wheel, new wheels already sized for the OE hub without a ring, or new wheels using a new ring may not be able to seat flush against the hub.
TIRE CHANGERS
As wheels become larger in diameter, and as tire section widths increase while sidewall heights decrease and beads become stiffer, "conventional" tire changing equipment must make way for machines that are specifically designed for today´s and tomorrow´s generations of super-performance fitments.
Today´s custom wheels are available in diameters ranging from diminutive to large to ridiculously enormous (plus-sizing today can involve 16- through 26-inch sizes). These large diameters, coupled with sometimes dainty rim lips that seem to blend into the tire sidewall profile, require the use of tire changers that are designed to handle these large sizes and the often stiff, incredibly low-profile (short sidewall) tires that have become popular in today´s aftermarket.
Generally speaking, the shorter the sidewall, the stiffer the sidewall and bead becomes, which requires a stout, precision changer.
One of the most important aspects with regard to proper mounting and avoiding bead damage is to keep the bead in the well! The newer three-arm mounting machines available today make mounting stiff-bead/sidewall, low-profile high performance tires much easier; they virtually eliminate the chance for bead damage during the shoe-on process.
Even many of the "table-top/overhead" models may not be adequate to service some of today´s wide rims when mated to low-profile performance tires. This type of changer secures the wheel by using steel jaws to clamp to the inside of the rear rim area, which causes damage (gouging, ruining clearcoat, the slipping of the wheel against the jaws, etc.) to the rim surface. The jaws may be applied to hold the rear of the rim externally, which also can damage the rim lip. Granted, plastic jaw covers may be used to protect the rim surfaces, but they also can diminish the grip, which can allow the rim to move on the jaws during ultra-stiff-bead, low-profile tire removal or installation. Wheel movement (cocking on the changer table) can place the front rim lip into dangerous contact with the guide spoon, causing rim lip damage.
Another concern while securing the wheel on the changer is the availability of shop air. During peak periods of shop air demand, air pressure available at the changer might drop below acceptable levels, possibly allowing the rim to spin on the jaws.
If your shop handles large volumes of custom wheel/performance tire work, serious consideration should be given to upgrading to a changer that is specifically designed to address large wheel diameters and stiff tire sidewalls. To mention only three, the Corghi Artiglio Master, Coats Model 9024E and Hunter TC 3500 are prime examples of sophisticated machines that will increase customer satisfaction and eliminate wheel or tire damage.
Nylon roller-type blades or tube-shape rollers apply downward pressure to the bead area to "roll" the bead onto the rim during mounting, and offer the same protective action when breaking the bead during demounting.
The new generation of changers includes features that permit secure rim clamping without damaging delicate custom wheels. The Hunter TC3500 features a "tulip" rubber-footed clamping system with center-spring-assist. The floating three-point articulating mounting arm follows the rim, with no need to adjust the arm away from the wheel. A polymer mount/demount head removes the potential for head-to-rim damage and rides closer than steel-head designs and reduces stress to beads on low profile tires.
The Corghi Artiglio Master uses a composite center taper cone and offset bolt hole dowel assembly. Coupled with articulated arms or articulated bead grippers, it is simply impossible to damage either the wheel or tire during mounting or demounting. The machine is capable of handling up to 26-inch rims with ease thanks to upper and lower rolling nylon bead breaker wheels and a fully articulated bead-gripper arm/finger ram.
The Coats Model 9024E handles 12-inch up to and including 24-inch diameter wheels using external clamping and 26-inch wheels using internal rim clamping that prevent wheel contact damage. The Model 9024E features an exclusive pneumatic drop center arm capable of flexing even the stiffest sidewalls, along with a power taper roller head. Swing-in rollers hold heavy tires when necessary.
[PAGEBREAK]
SAFETY CONCERNS WHEN CHANGING TIRES
Follow these safety procedures when changing tires.
* Wear safety glasses/goggles. During bead seating, airborne rim metal or bead material particles or loose debris from inside the well area can result in injury to the eyes, face or other body areas.
* Be aware of your surroundings (underfoot debris on the shop floor, loose clothing, jewelry, long hair, etc., that can be caught by the tire changer). Make sure that the shop floor in the immediate area of the change is clean and dry.
* Don´t hang/store miscellaneous items on the changer. Keep all moving parts of the changer free of obstructions.
* Never inflate the tire over 40 psi in order to seat the beads. If the beads won´t seat at 40 psi, something´s wrong. Deflate, inspect and start over.
* Routinely inspect the condition of the changer´s air hose and connections to avoid an unexpected pressure burst.
* Never position your body over the tire/wheel. Stand clear of the tire/wheel, especially during bead seating.
* Use a snap-on air chuck when inflating to avoid the need to keep your hand on the chuck. Use the machine´s foot pedal to apply compressed air, and stand to the side of the machine during this operation.
* Maintain your bead lubricant supply. Routinely check the lubricant reservoir to make sure that the lubricant isn´t contaminated, and that it hasn´t gelled or dried out. Always keep the lubricant supply covered to avoid contamination by airborne grit, etc.
* Always inspect the rim for cleanliness and damage before mounting.
* Use your legs, not your back. When lifting a tire, wheel or tire/wheel package, always lift using your legs. Improper lifting by bending and using your back can lead to back injuries.
IN CASE OF EMERGENCY, OPEN BAG: Provide customers with spare fasteners
After installing a set of custom wheels onto the customer´s vehicle, place one wheel´s worth of OE fasteners in an airtight plastic bag and store this in the vehicle (perhaps in an OE tool kit). If the customer ever needs to install the OE spare in an emergency, he or she will have the correct fasteners, since the fasteners that are used with the aftermarket wheels may differ in length or style from the OE fasteners.
Chances are the new fasteners will require the same size wrench as the OE fasteners. But if the fastener hex size differs from the OE size, at least make sure that the customer is aware of this. Maybe you can sell the customer an appropriate-sized socket and breaker bar.
PREPARE FOR IMPACT: This isn´t a race, so tighten properly
I cannot over-emphasize this enough: Never use an impact gun to install any alloy wheel. Why? There are two reasons for this.
1. There is an increased chance of marring a wheel with the use of a fast-moving and possibly misaligned air tool.
2. The value and consistency of any threaded fastener clamping load can be achieved only by hand-installation using a quality, calibrated torque wrench.
Ignore what you see during tire changes at a racing event. Pneumatic guns are used in those situations as a necessity in order to save time only. Don´t make believe that you´re in the pits at an endurance race when installing a customer´s set of pricey custom wheels. Take the time to do it right. Yes, it takes more time to hand tighten as opposed to zipping the fasteners on with a gun, but it´s worth it in terms of customer satisfaction.
Pay attention to torque value accuracy. When you do use a torque wrench, make the final pulls in a slow and careful manner, creeping up onto the final value (or "click"). By abruptly "slamming" the torque wrench, especially when using a ratcheting "click" type wrench, you easily can tighten beyond the target value. Is this being nitpicky? Yes, but what´s wrong with that?
By avoiding the use of an air wrench and following correct tightening procedures, you will avoid damage to the wheel and greatly minimize the chance of a comeback "vibration" complaint. Over-tightening or uneven tightening easily can cause hub/rotor distortion, which will result in brake rotor distortion.
After the initial installation, it´s advisable to check and re-torque all wheel fasteners after the vehicle has been driven about 25 to 50 miles. If the technician does not have the opportunity to perform this initial drive, make a point of instructing the customer to bring the vehicle back to the shop after 25 to 50 miles for a re-torque.
About the Author
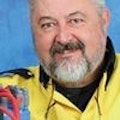
Mike Mavrigian
Longtime automotive industry journalist and Modern Tire Dealer contributor Mike Mavrigian also is the editor of MTD’s sister publication, Auto Service Professional. Mavrigian received a bachelors degree from Youngstown State University in English literature with a minor in journalism in 1975.