A tire mounting machine or wheel balancer never dies. It doesn’t fade away, either. It just stays in your shop until, well, you sell the shop.
The equipment is built to be sturdy. The average tire dealer performs 250 mounting/balancing jobs per month. And the machines built before the addition of electronics and lasers seemingly last forever.
Two years ago, Abe and Jim Torro won a then state-of-the-art Coats 1250-3DV tire balancer from Hennessy Industries Inc. They had entered their 30-year-old balancer in Hennessy’s “Search for the Oldest Direct Drive Balancer Contest.”
Abe Torro says the new balancer, which features laser-guided wheel weight placement capabilities, does a fine job. He still, however, prefers the older model, which can balance up to 20-inch tire and wheel packages. “I got used to it.”
The future is now
When asked by Modern Tire Dealer “What is innovative about your latest piece of mounting and/or balancing equipment?” these sales and marketing executives talked about features that will be around for a while.
Michael Alusick, worldwide product manager for undercar products, Snap-on Equipment Division of Snap-on Inc.: “Precision wheel centering to achieve accurate wheel balance is possibly the most neglected, yet most important part of successful wheel balancing. With the advent of clad-style wheels, precision tooling is a non-negotiable requirement to avoid wheel damage and achieve accurate centering.
“With our balancer brands, we offer several solutions to ensure the most accurate precision centering. We have a large coverage of OEM-specific tooling solutions. Precision tooling offers a best-buy situation for someone interested in a tooling package with a specific purpose.
“We offer a variety of precision John Bean General Purpose Tooling Kits with pin plates, unique speed plates and a variety of collet sets. These tooling packages offer complete coverage for the customer looking for a wide coverage offering for OEM and aftermarket wheels, truck and SUVs and even light commercial vehicles.
“We recommend wherever possible, that customers consider a power clamp instead of a standard quick nut. Power clamping is fast. Used in combination with precision tooling, the result is the most repeatable solution for accurate wheel centering.”
Jon Barganier, vice president of sales, Allpart Supply Inc.: “Our Haweka QuickPlates are designed to mimic the lugs exactly. We have four-hole, five-hole and six-hole variable flange plates. They are fast, easily adjustable with your thumb and precise. Unfortunately, the standard equipment for a lot of shops is a cone and a plastic pressure cup. The procedure is less precise, and when the cup touches the wheel, it can damage it.
“Bottom line, front coning is a no-no, yet it’s still a common practice. QuickPlates replace front coning and flange plating. The result is fewer comebacks, and the dealer doesn’t waste wheel weights, either.
“Although our QuickPlates have been out a couple of years, we continue to evolve their design features.”
[PAGEBREAK]
Derek Forney, marketing coordinator, International Marketing Inc. (IMI): “Equal is a plastic polymer that balances the tire from inside for the life of the tread and created the internal balancing category over 20 years ago. IMI continued the innovation with the ‘Drop-In Bag,’ not only eliminating the act of installation, as well as the time and labor involved, but also providing a simple solution for balancing tires during road service calls.
“Regardless of the size of shop, the increasing capital expense of a static balancing machine added to regular maintenance and calibration to maintain it is no longer the only option.”
Kevin Keefe, vice president of marketing, Hennessy Industries Inc.: “With the Coats EL-X Express Lane Inflation System, inflation can be carried out off the tire changer, so the technician can be changing the next tire while inflation occurs. The tire is fully inflated to within plus or minus .5 psi of the preset pressure.”
Jeff Kritzer, senior vice president of sales and marketing, BendPak Inc.: “When mounting heavy truck wheels on a wheel balancer, many users find themselves multi-tasking, as they’re forced to first lift the wheel over the wheel balancer shaft, choose the prescribed mounting cone, elevate the wheel to allow clearance for the mounting cone, then tighten the wheel mounting nut.
“Ranger products recently introduced their RB24T truck wheel balancer with a quick-chuck kit that reduces operator fatigue and decreases set-up times. Users simply raise and hang the wheel onto the quick-chuck that features auto-centering hardened steel wheel-holding supports. Then using a special quick-chuck wrench, the wheel is automatically centered and secured in just seconds.
“The three-jaw chuck features a forged steel body and hardened wheel supports and gear slides.”
MTD: What will the next generation of tire mounting and balancing machines look like?
Alusick: “We continue to look at the metrics of the complete wheel handling procedure. We consider the time element of moving a tire and wheel assembly from the vehicle through tire mount/re-mount, tire and wheel assembly diagnostic and balance, and then back to the vehicle. For any business from the large OEM to the small shop, procedures that shorten the time (bay turns), provide more information to the technician, promote handling safety, and most of all a ‘do no harm’ approach to expensive tire and wheel assemblies is our goal.
“Tire changers offer a number of enhancements, from bead breaking to wheel lifting to wheel holding options. There are a variety of methods to separate the tire and wheel to make the process easier. In combination, the goal is a shorter cycle time, safety for the technician, and most important, to avoid damage to the tire and wheel assembly.
“Future products will expand the capability of the tire changer and balancer by migrating technologies. For example, we may find that assembly runout measurement currently in balancers may migrate to a tire changer also.
[PAGEBREAK]
Barganier: “I think manufacturers are spending more on balancing and ignoring the mounting aspect of the service. Some of the so-called improvements are just bells and whistles. It is important that mounting and balancing interact with each other. Perhaps we will see both in the same unit. Mounting equipment just needs to be more precise, especially when dealing with medium and heavy-duty wheels. Also, dealers need to make sure they are getting full use out of their balancers. That is why training and education are absolutely key.”
Keefe: “Absent any radical change in tire or wheel technology that would drive substantive tire service process changes, I believe we will continue to see innovative new equipment features focused on delivering increased uptime, bay turns and ease of use. At the end of the day, our job as equipment manufacturers is to make it easy for our users to get the job done right, in a fast and intuitive way the first time.”
MTD: What innovations can we expect from wheel weight manufacturers?
Forney: “The increasing cost of tires may push for even smarter machines to diagnose issues with balance, run-out, and much more. However, the key remains to have an adaptive solution. Tires are not perfect before they leave the manufacturer’s dock and will never achieve such nirvana on a truck. The ‘revolutionary’ solution lies in the ability to adapt to changing conditions like the road, the load, speed, and tread wear that impact how long the tire will remain in service. Static wheel weights can’t achieve an adaptive balance, even if tires are rebalanced regularly.
“Wheel weight manufacturers have focused mostly on the green initiative in recent years. However, the adaptive balance feature in both the commercial and consumer markets can be found in XACTBalance, a stick-on weight that balances dynamically through free-moving steel particles.”
Keefe: “As automotive manufacturers continue to shift to flangeless wheel designs, I would expect to see ongoing innovations in the adhesive weight product category focused on reducing cycle time and achieving more one-spin adhesive weight balances.”
Gregory Parker, marketing manager, Perfect Equipment Inc.: “We are starting to see a lot of innovation in the OEM automation space, which is being driven by the larger wheel weight manufacturers. Automation allows OEMs to be faster and more precise with their in-line balancing processes. Some of those technologies can even be transferred over to the aftermarket.
“We will also begin to see more universal weights, or adjustable weights, in the aftermarket in the near future. This allows shops and distributors to lessen their inventory SKUs, yet still provide customers with a perfect balance.
“With this in mind, you will also begin to see better packaging, better handling and better recycling return options coming from wheel weight manufacturers. All of this is done in an effort to make shops faster, leaner, more efficient and more environmentally friendly. In the end, it’s all about reducing key-to-key time” and increasing overall customer satisfaction.” ■
About the Author
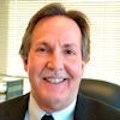
Bob Ulrich
Bob Ulrich was named Modern Tire Dealer editor in August 2000 and retired in January 2020. He joined the magazine in 1985 as assistant editor, and had been responsible for gathering statistical information for MTD's "Facts Issue" since 1993. He won numerous awards for editorial and feature writing, including five gold medals from the International Automotive Media Association. Bob earned a B.A. in English literature from Ohio Northern University and has a law degree from the University of Akron.