Third in a series
Last year, Modern Tire Dealer asked me to write an article comparing the 1970 Lincoln Continental MK3, the first American automobile to be equipped with radial-ply tires as standard original equipment, with a more recent Lincoln model. The purpose was to show how technology has advanced — and, in some cases, regressed — and what these changes and possible trends tell us about what is to come.
I compared the 1970 model with two other models. The first was the 1990 Lincoln Towncar, which typically exemplifies the Lincoln brand. In production for seven years, the vehicle was the last Lincoln of its kind. Its replacement in 1998 was inferior. I also selected a 2013 Lincoln MKS to make some sort of comparison.
Lincoln, at one time, was the best-selling luxury car brand in North America. Unfortunately, it has lost its way, and all attempts by Ford Motor Co. to regain its former position and glory have failed. Recently, the luxury segment of the U.S. automobile market has been dominated by foreign manufacturers (Lexus, BMW, Audi, Daimler-Mercedes, Tesla model S and others). But that’s another story worth telling at another time.
As part of this article, I was also asked to provide a “sneak peek” of what the future may hold for the American automobile manufacturers by 2020 as far as designing, developing, producing and marketing tires, tire/wheel assemblies and tire/vehicle systems are concerned. Eight years, even 10 years, is a rather limited time span to deliver vehicles that would:
• be unique in style and technologically superior;
• be affordable to Americans of any means; and
• capture the imagination of the driving public.
If OEMs can do this, then America would have a chance to gradually regain its former automotive industry glory.
[PAGEBREAK]
As Robert McNamara in the 1950s told us at Ford: “You can’t really break into a market dominated by well-established brands, unless you can provide something those brands don’t.” Let’s wait and see. In my opinion, it will be hard to achieve under the general circumstances facing America today.
I vividly recall when , at one point, General Motors Corp. had captured 55% of the market in the United States due, at the time, to its unique corporate structure, which, under Chairman Alfred Sloan, was already supplying a car for, as he said, “every purpose and purse.” This corporate structure, which Sloan called “decentralized operation with coordinated control,” worked well as long as GM dominated the market and had little to no real competition within and outside the U.S.
Today, GM has 18% of the U.S. car market, and foreign manufacturers dominate, having captured 55% of it. So much for a brief update on the current state of the American automobile industry.
Fundamentals
The field of tire/vehicle systems engineering, development and manufacturing encompasses vehicle ride, handling, stability, noise, vibrations, harshness, skid resistance or traction, overall vehicle rolling feel and operating smoothness, particularly braking, accelerating and cornering smoothness, as well as a high level of vehicle operating efficiency, judicious use of efficient materials, and, of significant value, structural integrity retention. Today, this requires fresh thinking of design, product development, manufacturing processes and personnel training.
The first impressions consumers get when driving a vehicle are design, comfort, noise levels, smoothness, intuitiveness and predictability of operation. The vehicle driver and the occupants all expect to arrive safely at their destination, and survive driving errors and vehicle operational problems. This is where the professionalism and scientific integrity of tire/vehicle systems design and development engineers involved in the entire vehicle development process come into play. As for achieving high levels of excellence in vehicle durability and reliability, once the prototypes have been validated for mass-production and consumption, it simply requires know-how, derived from years of experience.
Tire/vehicle system comparison: 1970 Lincoln Continental MK3/1990 Lincoln Towncar/2013 Lincoln MKS
The vehicles of the 1950s, ’60s, ’70s and even up to the mid-1990s featured high profile/high stroke tires with aspect ratios ranging from .60 to .80. They were inflated at low air pressures and mounted on 13-, 14- or 15-inch diameter wheels of widths ranging from five inches to 6-1/2 inches, which, when coupled to appropriately sized tires, represented 70% of the inflated tire section width.
These tire/wheel assemblies, when operating on the vehicle efficiently, performed all the functions for which they were designed, developed and produced. They efficiently absorbed road surface irregularities, and provided the vehicles with smooth, safe, predictable steering, braking and acceleration responses, as well as skid resistance and long tread life.
The vehicles on which these tire/wheel assemblies were fitted featured much more compliant suspension systems, including in the fore and aft direction; back then, we called it “pussy-foot suspension.” This fore and aft compliance significantly reduced vehicle ride harshness, particularly when using radial-ply tires, which were notorious for their very high harshness levels without such tire/vehicle system tuning (radial tuned suspension). These vehicles also featured full-vehicle perimeter frames, isolated from the vehicle bodies via judiciously positioned and well-tuned rubber mounts, and there-in lay the major differences between the 1970 Lincoln Continental MK3 or the 1990 Lincoln Towncar and the recently introduced 2013 Lincoln MKS.
1. The 1970 Lincoln Continental MK3. The 1970 Lincoln Continental MK3 was a radial-ply tire-tuned, elegantly styled, six passenger, rear-wheel drive, low aerodynamic drag, low center of gravity, softly sprung car of impressive stature and operational characteristics.
This gorgeous body-on-frame car weighed 4,800 pounds — heavy, but normal for this kind of car at that time. It was the first car in America fitted, as standard original equipment, with steel cord-belted, tubeless, white sidewall Michelin radial-ply tires, mounted on Kelsey-Hayes steel wheels of 15-inch diameter and six-inch rim width. The tire size was 225x15, the aspect ratio .80, and the inflation pressure 22 psi for town driving, and 26 psi for highway driving.
These new Kelsey-Hayes wheels were of a unique design and manufacture, both aimed at improving wheel precision, including improving tire/wheel assembly centering precision with the vehicle spindles. Within a few years of the 1970 Lincoln Continental MK3’s introduction, the Lincoln brand became the top-selling luxury car brand in North America.
[PAGEBREAK]
2. The 1990 Lincoln Towncar. The 1990 Lincoln Towncar was, in my opinion, the last Lincoln that Ford produced which I consider superior in all aspects of vehicle ride, NVH (noise, vibration, harshness) and overall operating smoothness characteristics, as compared to the much more recent Lincoln models, such as the 2013 MKS. The 1990 Lincoln Towncar weighed 5,442 pounds and featured body-on-frame construction and air suspension (in rear only). This suspension kept the car leveled, regardless of loads, and provided for a smooth, low-harshness ride.
It came equipped with 215/70R15 tires mounted on six-inch wide aluminum wheels, with the tire inflation pressure set at 30 psi in front and 34 psi in rear. By 1998, unfortunately, the car had changed, not only in style (less elegant-looking, in my opinion), but also in ride, NVH and operating smoothness characteristics. It was worse than ever before; it was no longer your typical Lincoln.
3. The 2013 Lincoln MKS. Recently, I had the opportunity to ride in a 2013 Lincoln MKS (which could have been more attractively styled) weighing 4,276 pounds and fitted with 245/45R20 tires mounted on 20-inch diameter, eight-inch wide cast aluminum alloy wheels. These tires were inflated at 32 psi, about 50% more than the 225x15 radial Michelin tires of the 1970 Lincoln Continental MK3 — and the MKS’ tire/wheel assemblies were much heavier than the MK3’s!
The 2013 Lincoln MKS is a stiffly sprung, highly damped car with a drastically “different” suspension system (continuously controlled suspension damping) featuring a unitized-body construction with a small sub-frame as compared to the body-on-full-frame construction of the MK3. As for the MKS’ NVH operating smoothness characteristics and rolling feel, I not only consider it inferior to both the 1970 Lincoln MK3 and the 1990 model year Lincoln Towncar, I actually find it unacceptable, and this in spite of that apparently newly developed, continuously controlled suspension damping system, which an ordinary consumer would not be able to discern. (Keep in mind that all vehicle suspension systems are continuously damped.)
There really is no reason why a unitized-body vehicle cannot be tuned for NVH to ride like a body-on-frame vehicle (1990 Lincoln Towncar); you just have to know how to do it. I demonstrated this, in collaboration with Pirelli, back in 1965 with the unitized-body Ford Falcon, which at the time, and upon radial-ply tire-tuning, was rated superior to a body-on-frame car, Lincoln included, in regard to NVH. Unfortunately, this lower-priced vehicle, as tuned, was never produced.
But back to the 2013 Lincoln MKS. The NVH characteristics are not the only aspect of the vehicle that is unacceptable. So is its $53,000 starting price. For the same price you might as well purchase the new, very elegantly styled Tesla Model S, a four-passenger, fully electrically powered vehicle, providing superior operating quietness for 265 miles before it needs recharging.
The 2013 Lincoln MKS’ interior was impressive. The on-board equipment, however, follows the current frivolous trends and features, heated front seats, for example. Have we really become such sissies that we need our rear-ends warmed-up?
Flashback to the past
The following offers an idea of what has happened in the past.
Tires and tire/wheel systems. Soon after World War II, when new tire, wheel and tire/vehicle systems testing techniques began to be developed, I was working at Ford (1955) and was keenly interested in not only improving tire, wheel and tire/wheel combinations in regard to manufacturing precision and uniformity, but also, and of great importance, in improving the match between tires and wheels, and between tire/wheel assemblies and vehicles.
By the 1960s, I called this approach “tuning,” including “tire/vehicle system tuning,” and this during the then “bias tire days.” With the advent of U.S. radialization, first initiated by Ford U.S. under my jurisdiction, “tuning” became much more problematic than originally anticipated, but it nevertheless became a success.
[PAGEBREAK]
Along the way, I became interested in significantly simplifying tire structures and tire manufacturing processes. I used the then recently introduced DuPont “Kevlar” cord material, called “Fiber B,” in conjunction with liquid reaction injection molding, a single polyurethane compound tire body and an SBR tread compound — all in combination with a simpler tire construction, but still based on the radial-ply tire architecture. I thought this would be a more economical solution to the fundamental problems of harshness, boom and “tire pull,” for which steel cord-belted radial-ply tires were notorious on many vehicles.
Nothing came out of this idea, but maybe one day it will. In the meantime, on certain vehicles, the basic radial tire problems are still with us today. In fairness, some solutions have been implemented, but with variable levels of success.
What may the future hold? Tires today are considered mature, fully developed products. However, they have become much too expensive, not only to purchase at replacement time, but also to design, develop, produce and apply. Consequently, by 2020 to 2025, tire design and tire manufacturing processes will have to have improved. Also to be improved is the match between tires (tire/wheel systems) and vehicles. To reach such desirable goals, the tire, wheel and vehicle industries have to make a serious concentrated effort. But, with the currently prevailing industry mentality, I fail to see how fundamental progress can be rapidly achieved, and this regardless of the effect of U.S. government legislation.
Today, we are living in a rush-rush-rush society that is detrimental to progress. To be creative and develop outstanding, fully competitive, well-developed, economical and attractive systems requires time to think. Real discoveries actually are unpredictable and often are derived by people who are not academically trained.
The solution requires more than simply modifying existing systems. Unfortunately, it often focuses on frivolous details, as exemplified by the wheel having become the cosmetic component of the vehicle’s unsprung mass. Something must change, and a serious education/indoctrination effort must be undertaken by the industry for the benefit of the consumers.
It is hard to imagine today that really new, fundamentally different and better tire/wheel system developments will take place for application on 2020 to 2025 vehicles, although I firmly believe that the potential of the radial-ply tire has yet to be fully exploited.
In the meantime, and again initiated by the U.S. government, tire and vehicle producers are getting ready to meet the U.S. corporate average vehicle fuel economy standards of 54.5 miles per gallon by 2025. I addressed this issue in my MTD article of August 2008, “Tire rolling resistance: How power wastage affects vehicle fuel consumption,” available on MTD’s website www.moderntiredealer.com. In it, I mention that there is only so much one can squeeze out of radial tires to improve vehicle system fuel efficiency, for the bulk of such efficiency lies in improving the vehicle because it is the vehicle that consumes most of the energy required for its propulsion.
The U.S. government is still pushing corn-based ethanol as a fuel to propel our vehicles, which goes against its own objectives, to maximize vehicle fuel economy. Also keep in mind that ethanol can damage the engine in some vehicles. Instead, what the tire, wheel and vehicle producers should do is increase tire tread life (80,000 to 90,000 miles), reduce tire/wheel assembly mass, reduce tire section width, increase tire section height, reduce tire prices, and reduce vehicle mass and prices.
[PAGEBREAK]
I like to finish my report on tire/wheel systems by quoting my late friend and collaborator at Dunlop England, Tom French, the director of tire development, who in 1989 concluded that “any changes are likely to be slow, and the reinforced pneumatic tire will essentially remain an engineering automotive component, which is awkward to produce, but which has a guaranteed future because of its unique and irreplaceable contribution to most forms of wheeled transport.”
Cars of the future. Before I get into the car of the future, the following may give you an idea of what has happened to date.
For many years, up to about 1933/1934, the engine pre-empted some of the most desirable space in the vehicle, and the prestige image was that of an enormous engine and hood, which occupied the front half of the vehicle’s available package, leaving a crowded passenger space that extended back over the rear axle and between the rear wheels.
By 1933, the passenger space had begun its forward migration to a position ahead of the rear wheels, while shorter but wider V8 engines (Ford) moved forward between the front wheels. By 1955, this pattern was complete, with the passenger compartment occupying the entire space between the front and the rear wheels, the engine occupying the space between the front wheels, and a luggage compartment, formerly not really available at all, having grown out behind the passenger compartment. This evolution of the American car layout permitted the passenger compartment to be lowered, thus bringing about a more efficient form of vehicle, which made the most effective use of its displaced volume, and provided for the minimum of weight, aerodynamic drag, cost and frontal area in proportion to its total capacity. But by about 1990/1995, the level of U.S. passenger car efficiency had begun to change for the worse, with the introduction of the SUV.
The major tire/vehicle system improvement implemented over the last 44 years in America was the introduction of Michelin radial-ply tires as original equipment on the 1970 Lincoln Continental MK3. This required the car to be specifically “radial-tuned” to be acceptable to American consumers. Another major U.S. improvement was the use of front-wheel drive powertrains, a European idea (the 1934 Citroën, the 1959 Morris Mini Minor). Such vehicle architecture permitted another level of vehicle package amelioration.
A seldom-mentioned improvement that also took place over the last 50 years in America is tire and wheel manufacturing precision and uniformity, which includes tire/wheel assembly centering precision and uniformity as mounted on the vehicle spindles. Ford led the way, first with bias-ply lower section height tires for application on the 1964 Lincoln and Thunderbird, hence creating a new era in tire/wheel systems, tire/vehicle system development and product acceptance engineering specifications.
Sneak peek at the future
Here are five areas that OEMs need to address, along with a few of my own predictions.
1. Operating efficiency. At this point, I urge the U.S. automobile industry to concentrate much more of its financial and personnel talents on improving the overall efficiency of its vehicles, from tires on, via a further reduction in overall vehicle weight, improvements in vehicle internal to external dimensional ratio. Also necessary are improvements in vehicle chassis (suspension, brakes, steering, etc.), body system precision, and, last but not least, significant improvements in vehicle propulsion systems based on the use of efficient, quiet, light, high torque, powerful, turbo-charged, common rail, economical to operate, four cylinder diesel engines, such as those that have been operating on vehicles in Europe for years.
Today, 60% of the European passenger cars are powered by diesel engine-based powertrains, which, on correctly tuned cars, are capable of nearly achieving today the fuel economy standards mandated by the U.S. government for 2025. In Europe, 100% of the taxi cabs have been powered by diesel engine powertrains for years. All these diesel-powered vehicles exhibit high levels of operating smoothness characteristics.
To reach the 2025 U.S. average fuel economy standards of 54.5 mpg and make these vehicles affordable to mainstream Americans, the average U.S. vehicle weight must be reduced by 300 to 400 pounds and tire/wheel assemblies by 25 pounds each. This will require super-creativity and innovations. All this has not been adequately explained to U.S. consumers by those who determined that 12 years from now American cars should average 54.5 mpg. In the meantime, I estimate the retail price of a 2025 U.S. car to increase by $4,000.
[PAGEBREAK]
2. Vehicle styling. The U.S. automobile industry should return to the uniqueness and elegance of the American car of yesteryear, gradually phase out the production of SUVs, and return to the station wagon type of vehicle architecture, in order to lower the vehicle’s center of gravity, and thereby improve vehicle stability and safety, and simultaneously increase vehicle fuel economy. Germany, for example, has already started this revival (VW and others), and the Japanese are just beginning to produce, for the first time, diesel engine-powered station wagons (Mazda).
3. Vehicle safety. Recently, Volvo, known for years for its safety-minded vehicle design, and the inventor of the three-point seat belt, announced that by 2020, it can produce an accident-free vehicle, whereby no-one will be killed or injured operating or riding in it. If Volvo’s objectives are met, it will represent quite an industry milestone and will, no doubt, be the revival of Volvo (now owned by a Chinese company). I expect others to follow suit. At this point, nearly 40,000 people lose their lives in America operating or riding in cars yearly, and many more are injured.
4. Electric or electric/internal combustion engine hybrid vehicles. The trend started with the Honda Insight hybrid nearly 20 years ago, and continued with the Toyota Prius three years later. At this point, all these vehicles are still too costly to purchase and operate. For example, the replacement cost of the battery pack alone for either type of vehicle (fully electric or hybrid) is much too high, and these batteries only last seven or eight years.
In the case of the fully electrically powered vehicle, the lower power density of the electric propulsion system as compared to the turbo-charged diesel engine-based propulsion system is a concern to me, as well as the limited range of fully electrically propelled vehicles. So is the anxiety factor associated with the battery power approaching full depletion and the lack of readily available charging stations.
All these are serious barriers to market entry for the electrically propelled cars. On the other hand, I appreciate the desire of a certain percentage of the U.S. consuming public to operate its vehicles at zero carbon emissions; but the electricity (and with it the pollution) has to come from somewhere.
5. Education. Finally, and of most importance, the American consumer must be properly educated about the pros and cons of all these recently marketed (promoted) vehicle propulsion systems. The engineering and scientific integrity of those involved with the development of these systems must be preserved and must come first. The public must be told the truth, and marketing must be set aside until all these new systems are fully understood, developed and made affordable.
In summary
The following is a recapitulation of the vehicle improvements I would like to see in the future: improved styling, weight and aerodynamic drag reduction; improvements in vehicle external to internal dimensional ratio; use of significantly more efficient common rail, turbo-charged diesel-based propulsion systems (which include more efficient transmissions and axles); more precise chassis systems (which includes better wheel alignment); and smaller/lighter wheels combined with narrower and lighter tires with aspect ratios of not less than .60, with the aim of reducing tire rolling resistance by 5% to 6%.
Also required will be more appropriate tire/vehicle system outdoor testing, as indoor machine testing can be limited in as far as duplicating real world road/tire/vehicle/driver system operating conditions are concerned. This will not only require lots of time and money, but also lots of talented, dedicated tire/vehicle system design and development engineers, which might be a problem.
Finally, the U.S. highway and street system must be improved in quality, durability and surface friction (traction) characteristics, in order to reduce vehicle skidding types of accidents. Also to be developed are warning and control devices to prevent a vehicle from driving off the road at high speed by automatically slowing it down when it approaches the scene of an obstruction, or when it is operating at speeds in excess of safe tire-to-road friction surface values for an encountered condition.
Undertaking these fundamental programs, and implementing them rapidly and successfully — for example, meeting the 2025 U.S. government regulations of 54.5 mpg corporate vehicle average fuel economy — might require an American manufacturer to enter into a partnership with others. ■
Jacques Bajer opened his own consulting company, Tire Systems Engineering Inc., in Grosse Pointe, Mich., in 1970. The firm specializes in the design of advanced manufacturing systems for the economical mass production of tires, power transmission belts, lathe-cut seals and air springs. He can be reached at (313) 886-6860.
About the Author
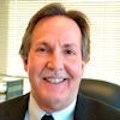
Bob Ulrich
Bob Ulrich was named Modern Tire Dealer editor in August 2000 and retired in January 2020. He joined the magazine in 1985 as assistant editor, and had been responsible for gathering statistical information for MTD's "Facts Issue" since 1993. He won numerous awards for editorial and feature writing, including five gold medals from the International Automotive Media Association. Bob earned a B.A. in English literature from Ohio Northern University and has a law degree from the University of Akron.