Maybe Izzy, the dyed-hair kid, wants a set of 215/40ZR17 black rubber bands on his VTEC Honda. Or Dr. Dough, the surgeon, desires a set of 275/35ZR19s for his weekend-toy M5 BMW.
These guys, and anyone who purchases performance-grade tires and custom alloy wheels, assume a few notions from the get-go. Aside from the anticipated traction, response and eye-appeal that they assume will accompany their new performance shoes, they fully expect the mounting and balancing procedure to be performed properly, with no scuffing, scratching or scarring of their wheels, and no tears or scuffs on the rubber.
They also expect the new set of tires to travel down the highway vibration-free. But, as the expert, you know the reality of putting high performance tires on their vehicles, especially when plus-sizing is involved. So it is up to you to tell Izzy or Dr. Dough that their ride is going to be different if they choose, for example, a Plus Four move.
[PAGEBREAK]
RULE #1: DO NO HARM
This pledge, taken by every medical doctor in the country, also should be taken seriously with regard to the handling of custom wheels. Granted, the customer may swipe his new alloys against a curb 15 minutes after leaving your shop, but that´s beyond your control. While the wheels are in your hands, do not scratch or gouge, period. While that simple directive sounds, well, simple, it´s anything but.
There are enough potential risks and horrors in the shop that it´s sometimes surprising new alloy wheels don´t jump out of their boxes and run out of the door screaming. Where´s the danger? Just take a look around the shop.
* The wheel could be handled with dirty hands that are full of grit or adorned with rings that can scratch the fine surface finish. Preventing this danger is simple: Clean your hands before handling the new wheels, and remove all jewelry, including your watch.
You should not be wearing jewelry during work hours anyway due to the ever-present danger of catching that jewelry on a moving part or tool. While everyone knows this, too many ignore the risk until they see a buddy´s finger ripped off in a shop accident that could have been avoided.
* The wheel can be dropped or scraped on the floor. If the wheel slips out of your hands, it could drop and hit the concrete floor with the obvious risk of surface finish damage.
Again, make sure that your hands are clean and dry before handling the wheels. If your hands are slimy with bead lube, don´t attempt to handle a bare wheel.
Even if the wheel is carefully laid onto the floor on its rear lip surface, it could be kicked or nudged by accident, scuffing the rear lip surface (and possibly scuffing a clearcoat layer in the process). The answer: Try your best to keep the floor clean, and first lay down protective material before resting wheels on the floor. This could be anything from a chunk of clean scrap carpet to a piece of clean cardboard.
* The wheel could be scratched, scraped or gouged by the changer. This danger potential involves several issues. First of all, regardless of the type of changer you employ, keep it clean.
Sure, changers are easily contaminated. They get dirty quickly during the routine business of the day, and it´s hard to find the time to clean the darned thing. However, if you´re handling expensive custom wheels, find the time. A dirty changer offers great potential for surface-finish scuffing because grime, grit and dirt can rub against the wheel, or can transfer from your hands to the wheel.
One option, of course, is to purchase a second tire changer dedicated only to custom alloys, but that´s up to you and your accountant.
Do not use an impact gun to install custom alloy wheels. Aside from the fact that alloy wheels should be torqued manually, there´s a simple wheel care issue at stake as well.
The outside of the socket may be dirty or rough (especially black oxide-coated impact grade sockets), which can easily leave circular scars on the inner walls of the fastener hole recesses. Even if the socket is clean, it doesn´t take much to leave light scrapes and scratches due to off-angle rubbing against the wheel surface.
With that said, in a perfect world we also would rail against the use of guns for wheel removal, for the same fear of scratching the fastener recess walls. However, we all know nobody wants to monkey around with a car on a hoist, with a buddy holding the brake pedal down, so that we can manually loosen each wheel nut or bolt. In the real world, it´s just easier to at least loosen the fasteners with a gun.
So, if you´re going to loosen with a gun, try to follow a few guidelines to reduce the risk of damage to the wheels.
Clean the fastener area as much as practical to remove any grit that might contact the socket. Hit the fastener only enough to crack it loose, then remove each manually.
The danger lies in allowing the socket to spin at full burst, since we know that once the nut or bolt leaves the threaded connection, it´s likely to continue to spin wildly (off center) for a moment or two even after we release the trigger.
To protect yourself, have customers look at all four tires and wheels before they drive off, and then sign off on their appearance. That way, they can´t come back later and say a blemish was your fault.
[PAGEBREAK]
RULE #2: LUBE FREELY
Prior to running a seating guide or tire iron around the bead, it is imperative to lubricate the tire bead with a clean and recommended bead lubricant. This includes both the rear and front beads. The lube must be clean -- no grit or metal shavings, which means that the changer and the tub of lube should not be parked next to a bay door, a glass bead machine or a drill press.
Then the lube should be carefully applied to the entire bead surface to eliminate any dry-spot snagging during the bead positioning process. Unless you´re prepping a wheel/tire package for a racecar that´s already in the pits, there´s no need to rush this part of the job.
Inspect the application brush to make sure that it´s clean. Apply lubricant along the tire bead surface, including both the front face of the bead and the inner edge of the bead. Excessive amounts of lube are not necessary, but total coverage is.
Make sure you haven´t accidentally dropped a big glob of lube into the tire before placing the tire onto the wheel. Also, if you drop your brush on the floor, as will happen from time to time, set it aside for cleaning and grab your backup brush.
If you don´t keep a backup brush, then stop, clean the brush, re-wet it with lube and continue. If you wouldn´t eat a hot dog that fell onto your floor, then you shouldn´t allow your lube brush to touch it as well.
RULE #3: PAY ATTENTION TO SEATING PRESSURE
Once the tire has been mounted onto the wheel, the beads must be seated properly. Attach the air chuck to the wheel´s air valve, and step aside while you apply pressurized air via the changer´s foot pedal.
Never stand directly over the wheel/tire during initial bead seating inflation. Maybe you´ve never experienced a blowout or slip-off, but that doesn´t mean that you should tempt fate.
Also, never exceed 40 psi during bead seating. If both rear and front beads do not seat at 40 psi, don´t follow your temptation to inject more air pressure. The safe way is to remove the air chuck, allow the internal air to bleed off, break the beads loose (fully, all the way around the bead circumference!), re-lube both beads and try again.
[PAGEBREAK]
RULE #4: LOOK FOR BUBBLES
Once the beads have seated, examine the bead edges closely and look for air bubbles. If your lube isn´t the type that is loose and watery, squirt some soapy water onto the bead areas in search of bubbles. Evidence of escaping air means that contaminants are trapped between the tire bead and the rim´s bead seat, or that a burr exists on the rim, etc. If bubbles are found, mark the spot with a tire crayon, break the bead seat loose and examine for the cause of the leak.
RULE #5: MATCH-MOUNT WHEN POSSIBLE
Match-mounting is an approach that allows you to position the tire to the wheel in the best location in order to increase the odds that the assembly will run smoothly with no vibrations or thumps.
There are actually two methods of match-mounting, designed to either reduce the chance of runout vibration/thumping, or to optimize balance. The basic idea with regard to match-mounting is to place the tire in the "best" clock position on the wheel to fine-tune the fit.
If we match-mount to reduce runout-associated vibration, we align the "high" spot of the tire (the area where runout is greatest) to the wheel´s "low" spot (where runout is minimal). In theory, this mating of tire high spot to wheel low spot will negate the effect. At the very least, match-mounting for runout avoids the "stacking" of tolerances, which would happen if the tire high spot aligned with the wheel high spot (this scenario would pose the greatest chance of producing a radial "thump" during operation).
Match-mounting to reduce the chance of runout vibration or a phenomenon called "radial force variation" has nothing to do with the balance condition. Radial force variation involves the shape of the tire mass as it impacts and leaves the road surface.
In order to match-mount to avoid runout-stacking conditions, the tire may be labeled with a color dot (paint mark or label, likely in red) that indicates the high spot of the tire´s maximum runout or the expected force variation location. This should be aligned with the wheel´s low-runout spot, which may be identified with a small notch or color dot. Since labeling approaches vary, check with the wheel maker´s instructions for low-spot identification.
If only one or neither component is labeled, runout locations can be found manually. Chuck the bare wheel onto a lathe or changer (the lathe or changer spindle should be verified true first). Place a dial indicator on a secure stand adjacent to the wheel. Place the dial indicator probe, equipped with a roller tip, against the outer edge of the rim radius. Pre-load the probe plunger and zero the indicator dial.
Slowly rotate the wheel until you find the lowest spot of the radius, and mark that spot with a crayon or other marker (be careful not to apply a permanent marker to an exposed surface of the wheel).
If the high spot of the tire is already marked, simply mount the tire to align the tire high spot to the discovered rim low spot. If the tire isn´t pre-marked, go ahead and mount the tire to that wheel. Chuck the assembly onto a changer spindle, set up the dial indicator at the center of the tread and slowly rotate the assembly.
When you find the tire´s highest runout spot, mark this and record the tire´s runout reading. If it´s acceptable, go ahead and balance. If you think the runout is too great, or if you simply want to try minimizing it, break the tire beads loose and rotate the tire on the rim to match the two marks.
After re-inflating the tire, make a runout check again to see if the tire runout has increased or decreased, or if the runout spot has moved. Adjust the tire to the rim accordingly.
If you don´t wish to bother with match-mounting with regard to runout or radial force variation, you may be able to match-mount to improve the balance of the assembly.
If the tiremaker also has marked the tire for balance (a second dot, likely in yellow, will indicate the tire´s lightest weight), you can weight-match the mounting by aligning this dot to the wheel´s air valve. In theory, the valve location may be the heaviest spot on the wheel, so it makes sense to try to cancel the light spot of the tire against the heavy spot of the wheel to optimize the initial state of balance.
Assuming the valve area of the wheel always will be the heaviest area is debatable, since the valve might actually weigh the same, less or more than the wheel metal that was removed to create the valve hole. Nevertheless, the theory is acceptable in most cases, so if a tire weight dot is found, go ahead and align it to the wheel´s valve location.
So, match-mount if possible, to either reduce the chance of runout thump, radial force variation or to optimize the balance. Regardless of which method you select, once this is done, the assembly can then be balanced.
[PAGEBREAK]
RULE #6: INFLATE TO SPEC
Always adjust the inflation pressure to the specification for that vehicle, and always check for specific front/rear inflation specs. Do this before installing the assemblies onto the vehicle, so that this step is not missed later.
There´s another good reason to set pressures as soon as the chance arises: It´s not uncommon at all for some customers to request mounting and balancing while planning to install the assemblies to the vehicle themselves. The vehicle may be on stands at home because the owner is performing other modifications or maintenance. Or the weather that day may be bad, prompting the owner to leave the vehicle at home and use his daily commuter instead.
Inflate the tires to spec now, so that you know they left your shop in proper condition. Never assume that the customer will remember to correctly adjust the pressure.
INSTALLATION TIPS
While the thrust of this article discusses how to mount and balance high performance tires and wheels, we thought it important to mention a few installation rules as well.
1. Make sure the hubs are clean.
2. Check the thread condition of the fasteners.
3. Don´t tighten fasteners with an impact gun. Install the fasteners (nuts or bolts, depending on the application) by hand, and then tighten with a calibrated torque wrench (in two or three increments) to specification value, and in proper sequence.
DO YOU NEED A NEW CHANGER?
The topic of selecting the changer style is touchy, because in today´s economic climate some shops may be hesitant to make capital equipment investments. However, if your only changer is an antique that can´t handle wide rims, big-diameter rims and stiff tires, you may not be able to cleanly mount these systems.
If you´re going to mount/dismount today´s performance wheels and tires, you need a changer that will secure the wheel solidly without digging into the material with big, fat, sharp teeth. You need a changer that offers a bead-pusher aid so that you don´t need four arms and irons to push the tire bead past the outer rim flange.
The changer also should be massive enough not to deflect during the strain of stiff-tire bead seating. If an overhead arm deflects, this changes the position of the guide spoon, which can then dig into the rim.
Speaking of guide spoons, or whatever name you want to give to the stationary curved fixture on the machine´s arm that "guides" the bead onto the rim, you need one that is somewhat protective of the wheel. The guide should be coated with a protective, slippery material to reduce the chance of wheel damage if the guide, indeed, bumps into the wheel.
An old rim-clamp style changer, for example, might offer a bare steel guide that, over the years, has developed a few sharp edges and burrs. If this jumps into the wheel rim flange, something is going to be gouged, and you can bet that it won´t be the guide.
So, either keep your existing machine clean and well maintained, or buy/lease an updated machine that will handle today´s big wheels and stiff tires. Even if your current machine is maintained in like-new condition, you need to update it if it was designed to handle a limit of 8-inch wide and 15-inch diameter wheels shoved into 80 to 60 series tires.
Granted, you may be able to use your old machine to "get the job done," but if that means constantly worrying about damaging each wheel that´s placed onto the machine, the current machine probably is past its prime and should be replaced. It may be a hard pill to swallow if you´re not comfortable with assuming new debt, but without a capable machine, you´ll lose money (and customers) in the process. Just view the new equipment as an investment instead of an expense.
[PAGEBREAK]
BALANCING ACT
Every wheel and tire package needs to be checked for balance and corrected as needed. The only exceptions are those tires and wheels that are being used for low-speed, off-highway use on applications such as tractors, off-road rock-crawling trucks, etc.
Although today´s wheels and tires, by and large, are extremely well made, small manufacturing deviances can occur in terms of weight distribution. On a smooth road at typical driving speeds, these deviations can result in a vibration that is felt by the driver and passengers. To eliminate this potential, you should check the mounted tire/wheel package for both static and dynamic balance.
1. Static balance refers to the correction for weight when considering radial force only (the force that occurs in a perpendicular line from the center of the axle outward).
Imagine a tire/wheel resting on a spindle at the wheel center. If you view the mounted tire/wheel face-on as a clock, then imagine a one-pound weight is attached to a spot on the center of the tire tread. That heavy spot will naturally come to rest at the bottom, or the 6 o´clock position, regardless of where you rotated the tire to position the weight elsewhere.
When driven, the extra weight (whether that weight is in the tire, the wheel, or a combination of the two) will act with more force against the road, creating a vibration as that heavy spot thumps its way along. When we add weight to the wheel on the opposite side of the axle from the tire´s heavy spot, we can counteract the tire´s heavy spot so that the wheel/tire would not be weight-biased at one spot along the radius of the tread center.
Static imbalance would create an up/down force that we feel as a vibration. We could also call static imbalance "radial" imbalance because of the direction of the force.
2. Dynamic imbalance is a condition in which there is unequal weight on either side of the tread centerline. While that unequal weight affects static balance in a radial direction, it also affects the axial direction, and causes a wobble or shimmy-type vibration because the weight difference exists off of the tread centerline.
While static imbalance can be monitored on a simple pedestal-type "bubble" balancer, dynamic imbalance only can be monitored on a "spin" balancer that allows the varying weight differences to be revealed in both radial and axial planes (that´s why spin balancers are often referred to as dual-plane balancers).
In addition to checking for weight balance, runout-related imbalance can be checked by measuring radial runout (see "Radial force variation" sidebar) and lateral runout. While radial runout is measured at the circumference, perpendicular to the axle, lateral runout (also called axial runout) can be measured at the tire sidewall and wheel rim face (parallel to the axle).
If excessive lateral runout is measured, suspect a bent wheel; it likely is distorted at the wheel center area. The tire also can be measured for lateral runout at the sidewall.
So if you find lateral runout, it´s likely the wheel´s fault, and the wheel should be replaced (if the wheel can be straightened, do not attempt straightening it on your own). As with any other opportunity to handle the wheel, balancing offers a fair number of chances to scratch the wheel finish. Make sure the balancer is clean; that includes the spindle, the spindle backing flange, the centering adapter and the spindle nut/arm. Make sure the backing flange and the centering adapter are free of burrs as well.
Before spinning the assembly, take a look at the wheel to determine what type of weight will be used. Your choices include conventional "clip on" weights, which feature a formable tang that slips onto the rim lip; adhesive-backed "stick on" weights; and more intricate and less-common screw-adjusted weights (used on some Jaguars and other exotic imports, these gently position onto the rim lip but are secured with an adjustable tang via a threaded adjuster to prevent wheel damage).
Tell the customer about the different wheel weight styles and let them decide what they want. If appearance is key, and the customer does not want to see a clip-on weight on the rim face, you may be able to correct any static and dynamic imbalance with a combination of clip-on weight on the rear lip and/or adhesive weight on the inboard surface of the rim.
Before installing adhesive weights, be sure to wipe the installation area with evaporating solvent such as denatured alcohol or a paint-safe surface-prep solvent. If the weight´s installation surface area is not clearcoated or painted, you may be able to use a brake cleaning solvent, but be sure beforehand, since this type of solvent can quickly and severely damage many coatings.
[PAGEBREAK]
If the adhesive weight involves something longer than one short section, pre-form the weight strip to the contour of the area first by placing the weight onto the surface and bending it to conform to the rim curve. Then remove the backing to expose the adhesive and stick the weight onto the surface. Apply firm finger pressure to ensure that the weight adheres thoroughly.
If the weight is a clip-on, be extremely careful when dealing with a coated wheel. For instance, if the rim is clearcoated, the weight´s clip might pierce the clearcoat layer, and allow long-term moisture migration under the clearcoat. This will result in fogging and staining, essentially ruining the wheel´s appearance.
If the rim is coated or painted, and the owner cares about long-term appearance, stick with adhesive weights.
And for your safety, whenever a wheel/tire assembly is about to spin on the balancer, never stand in-line with the tire, since an unsecured weight can eject and cause personal injury. And don´t be tempted, as some shops are, to remove the safety shield from the balancer. A spit-out weight can cause serious damage to people or nearby vehicles.
Getting in tight with your customers: Re-torquing wheels shows how much you care
While some wheel makers may say that there is no need to re-torque today´s wheels, there is no harm in doing so. Most experts regard this as a post-mounting and balancing requirement, because the tightness of the fasteners may change as the new wheels and fasteners "settle" after being exposed to temperature changes and dynamic stresses.
Suggest to your customers that the fasteners should be re-torqued after the first 50 to 100 miles or so.
Don´t automatically blame the tires! Look at the big picture to solve vibration problems
Shakes, rattles and rolls may be desirable cuts on an Elvis CD, but they´re certainly not welcome aspects of a snazzy new wheel and tire package.
Customers may be quick to single out the tires, or your handling of them, as the source of their vehicle vibration problems. But many other variables are potentially involved, any one of which could be the root cause of the vibration.
In addition to those mentioned in the main story, consider the following as possible problem areas, none of which directly involve the tires.
* Worn or loose wheel/hub bearings.
* Loose wheel fasteners (check the torque!).
* Wheel not mated squarely to the hub face (due to debris on the mating surfaces).
* Distorted or out-of-balance CV shaft (maybe the rubber damper fell off).
* Worn, loose or too-soft bushings at critical control arm locations (torque rod in the case of a single-pivot lower arm setup), control arm pivots, etc.
* Out-of-balance primary drive shaft.
* Flat-spotted tire treads (the result of previous severe brake lockup).
* Mud/dirt collected in the inboard wheel cavity.
* A too-large tire setup (in terms of mass) that is not designed for use on the specific vehicle.
* Hubcentric wheel mated to a lugcentric hub flange or lugcentric wheel mated to a hubcentric hub. If not centered properly, this would create an eccentric out-of-round condition.
* Severely worn dampers (shocks/struts).
* Broken weld joints in a unit-body chassis. It´s a stretch, but if the vehicle is equipped with stiff, short sidewall tires and stiff springs/shocks, the unit-body seams may have been fatigued. This condition may or may not help to create a vibration, and could also contribute to wander and reduction of steering response.
Radial force variation: In rare instances, maybe it is the tire
There are two types of radial runout, defined as runout deviation that can be measured statically but may only show itself under dynamic conditions (when the tire runs with a load).
Static runout, as we noted earlier, refers to a high spot of the tire, a physical characteristic that can be measured with no load placed on the tire. Radial force variation refers to a runout condition that only occurs when the tire runs at speed, under load, due to variations in construction stiffness.
Radial force variation is so-named because the radius of the tire varies according to vehicle speed and load. Of course, any tire, because of its compliance, will vary slightly in radius at the load spot during operation. Although a "radial force" might be the result of a runout area that is pronounced enough to affect the tire´s impact on the road, a radial "force variation" may occur if the tire has appreciably different "soft" spots and "stiff" spots in the carcass and/or tread or in the sidewall construction.
Given the high quality control processes used by today´s tiremakers, it´s rare that a force variation problem will occur. But when it does, it can be a tricky demon to chase.
Even though no problems may be found as the tire rotates on the balancer, when the tire experiences a load, the transition of the harder and softer sections of the tire may create a series of harmonic vibrations as the tire contacts and leaves the road surface. Depending on conditions, this harmonic may occur once per revolution of the tire, or it may occur in a series of multiple vibrations per revolution.
It´s possible that this phenomenon may vary according to changes in tire pressure, vehicle speed, individual tire load and the road surface conditions, all of which may serve to reduce and/or amplify the vibration problem. In other words, the vibration that the driver feels may not occur at any one rate of speed, or on any road surface, because the problem may appear only under a specific combination of these variables.
If a tire/wheel will not balance properly, or if a vibration exists after a successful balance job, don´t automatically blame the tire. If you haven´t checked the hub and wheel for runout, you may be jumping to conclusions.
If, however, all balance, static runout and chassis parts variables have been exhausted, then it may be time to suspect a radial force variation problem.
In order to check for and attempt to actually verify a dynamic radial runout condition, a spin-balancer with a built-in load roller is recommended. This type of balance machine places a load (which attempts to simulate road load) onto the tire as it´s spun, and monitors and records the subsequent variances of runout.
If load variation is found, it may be corrected with the use of balancing weights. In extreme cases, the tire may have to be replaced.
LOADED TIRE RUNOUT
As a general rule-of-thumb, a minimum range of from .3 to .5 ounce (7-14 grams) of imbalance is usually enough for the average motorist to notice an imbalance-induced vibration.
If a vehicle is sensitive enough to exhibit noticeable vibration at only .3 to .5 ounces of imbalance, that same amount of vibration may be present with as little as 10 to 15 pounds of radial force variation, which (although hard to believe) can be caused by as little as .010 to .015 inch of loaded radial runout.
Using this as an example, it´s easy to see how loaded runout can dramatically affect vibration. In other words, a little bit of "loaded" tire runout variance can make a big difference in terms of operating smoothness or harshness.
About the Author
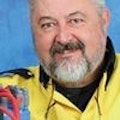
Mike Mavrigian
Longtime automotive industry journalist and Modern Tire Dealer contributor Mike Mavrigian also is the editor of MTD’s sister publication, Auto Service Professional. Mavrigian received a bachelors degree from Youngstown State University in English literature with a minor in journalism in 1975.