Tire dealers in Minnesota, the latest state to ban lead wheel weights, have about five months to find non-lead alternatives. Minnesota’s wheel weight law goes into effect on Jan. 1, 2016. In addition to Minnesota, lead wheel weights are illegal in California, Illinois, Maine, New York, Vermont and Washington.
Two states and one country are now considering wheel weight regulations. Legislators in New Jersey proposed a law banning lead and mercury wheel balance weights in February 2015. In New York, which banned lead wheel weights in 2011, lawmakers are considering a bill prohibiting mercury wheel weights. In Canada, lead and mercury wheel weights could be banned throughout the entire country. Environment Canada (EC), the government body responsible for coordinating environmental policies and programs, has been studying the issue for about a year.
Plombco Inc. was part of a public hearing held in the summer of 2014 regarding lead wheel weights in Canada, according to Martin Lussier, president of the Valleyfield, Quebec-based company. “The Ministry of Environment stated that lead wheel weights must not be used anymore and explained in length why they believe it is a threat to the environment. However, they are weighing their options in terms of how to achieve that. Plombco supports that initiative, and we hope that the Ministry of Environment makes a decision as soon as possible.”
Try the lead-free options
As individual states and the Canadian market continue to move away from lead, at some point the U.S. Environmental Protection Agency is likely to step in and force the rest of the market to transition, says Gregory Parker, marketing manager for Wegmann automotive USA Inc., the parent company to the Perfect Equipment and Hofmann Power Weight brands. “This means that all businesses should be investigating and testing the non-lead options to better prepare themselves for the future.”
Steve Parker, sales manager for Hanco Corp., an Eagan, Minn.-based distributor of tire and wheel-related products, tools, equipment and supplies (and no relation to Wegmann’s Parker), suggests dealers ask their suppliers for wheel balancing options. “It’s tough to change when you are used to something. Some techs don’t like the look of a certain weight. You used to be able to make a lead weight work just about anywhere, but it’s a lot different with non-lead.”
Samaritan Tire Co. in Minnetonka, Minn., sells on average 60 to 80 tires a day, or about 20,000 tires a year, according to owner Chris Mortensen. “We’re tire-focused,” says Mortensen. “We do everything wheel-related; we do nothing under the hood.” Although the 15 employees in his 10-bay shop provide retail and commercial services, high-end vehicles such as Ferrari, Porsche and BMW make up the bulk of the business.
Mortensen’s service manager, Rob Roy, began planning the transition to non-lead weights a couple of years ago. Multiple vendors brought in different weights for techs to sample. “We tried some composite weights. It’s a different system than what we’re used to, and it just didn’t work for us because my techs are used to clip-on weights.”
OEs also drive the shift
Samaritan Tire continues to adjust. “Iron and zinc seem to work about the same,” says Roy. “The iron is a little denser so the weights are a little smaller so when you get to a big weight the arc of the weight doesn’t necessarily match the rim arc. With the lead weights it didn’t matter, you would just re-form them to the correct shape. But you can’t do that with zinc and iron.”
Wheel weights are a significant expense, and the non-lead options cost slightly more than lead. “Right now we bounce back and forth between iron and zinc; the main deciding factor is cost. We stock all the different profiles of wheel weights for clip-ons, and we do a lot of tape-on. As the years go by we do more tape-on weights, but we still stock the clip-on profiles. They have to work, and they have to be cost-effective,” says Roy.
Samaritan Tire’s use of adhesives is consistent with market trends, according to Wegmann’s Parker. Original equipment manufacturers as well as legislative actions are behind the shift to lead-free alternatives.
“One thing to take note of is the slow increase in the usage of adhesive weights industry-wide as compared to the slow decrease in the usage of clip-on weights. This is due to two factors. One, the increased introduction of flangeless alloy rims from the OEs and two, the introduction of adhesive wheel weight automation in OE factories.” ■
About the Author
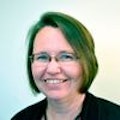
Ann Neal
Ann Neal is a former senior editor at Modern Tire Dealer.