Though the wheel was anonymously invented in 3500 B.C. by some brilliant Sumerian, it wasn’t until the height of the Roman Empire that customizing wheels for styling and performance became popular.
Chariot racers wanting to gain an advantage over their foes designed special wheels with metal spikes to cripple competing vehicles. Since there wasn’t a sanctioning body for the events held at the Circus Maximus, using such cutting edge technology was completely legal. Just ask Ben-Hur.
Patricians watching these races soon demanded to have similar wheels for their street chariots. Thus, the custom wheel aftermarket was born.
Today’s custom wheels, used on cars and light trucks as diverse as a Ford F150 to a Porsche 911, also descended from racing applications.
Ted Halibrand, a veteran racer and owner of a racing parts manufacturing firm, unknowingly started the craze for stylized wheels in the late 1940s when he engineered a light-weight magnesium wheel for track use. Its unique look grandfathered a wave of street copycats that entered the marketplace around 1960.
Such was Halibrand’s influence that these knock-offs were called “mag wheels” even though they didn’t contain any magnesium. Since they were subject to severe corrosion and posed a fire hazard, magnesium wheels have always been limited to racing applications.
The earliest custom wheels were either made of one-piece cast aluminium or aluminium centers riveted to chromed steel rims.
While aluminium wheels had been used on race cars as early as the 1920s, they were extremely expensive, preventing their spillover into standard automobile design. A stronger, but heavier and unattractive, steel construction had been used instead.
However, improvements in the manufacturing process eventually led to the development of economical aluminium wheels that resembled those used on the fastest cars in the world.
Since the birth of the modern custom wheel market in the 1960s, hundreds of companies have tried their hand at improving product performance, while creating styles attractive to car owners.
The one-piece cast wheel has always held the greatest share of the market, mainly because it is the least expensive. This type of wheel, formed at low pressure, is strong, but not nearly as strong as those made through counter pressure casting or billet forging methods—methods that invoke a lofty price.
Multi-piece wheels offer superior durability and, at the same time, are much lighter, more flexible in application and considerably more expensive than one-piece designs.
Since these processes have somewhat equalized the product quality of wheel manufacturers, styling has become the all-important selling feature for the 1990s.
However, this rarely has anything to do about translating what people see at the race track to the street.
Like clothing designs, the latest wheel fashions are now often the result of someone’s creative whim. For this reason, both have an extremely short life cycle.
If a new look sells, it usually lasts about six months before it’s copied by the competition and loses its distinctive look.
In time, such designs will be nothing more than a distant memory, while classic styles that harken back to the racing cars of 30 years ago have survived and thrived.
About the Author
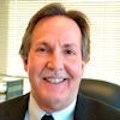
Bob Ulrich
Bob Ulrich was named Modern Tire Dealer editor in August 2000 and retired in January 2020. He joined the magazine in 1985 as assistant editor, and had been responsible for gathering statistical information for MTD's "Facts Issue" since 1993. He won numerous awards for editorial and feature writing, including five gold medals from the International Automotive Media Association. Bob earned a B.A. in English literature from Ohio Northern University and has a law degree from the University of Akron.