Success in a tire bay, as in any workplace, starts with mastering the basics. We’ve gathered tips from four tire equipment manufacturers to solve these everyday mistakes.
Hunter Engineering Co.’s Pete Liebetreu says the most common tire mounting and balancing problems are caused by fundamental mistakes that, in many cases, are easily remedied.
1. Mounting mistake: Bead not properly placed on the mount head
The number one cause of complications and tire damage is not placing the bead properly on the mount head. “In some cases you can get away with indifferently placing the tire on the mount head, and the mount head will accept it,” says Liebetreu, who is vice president of marketing for Hunter.
But in most cases, the tire will be damaged if a very thick bead or other conditions prevent it from climbing up over the mount head. “At that point you can cut the tire either from the rim or from the mount head itself.”
Also, top-bead mounting can cause the operator to lose the clock position for the tire pressure monitoring system (TPMS) sensor when the tire stops and resets.
2. Mounting mistake: Not pushing the tire into the drop center
Liebetreu says he frequently sees operators fail to push the tire into the drop center of the wheel. “It’s amazing how many technicians don’t completely understand the purpose of pushing the tire into the drop center,” he says. “You’ll see them stall the tire and damage it. Or halfway through top bead mounting have the tire pop off the mount head or the rim and fail to mount.” Failing to perform this basic step also is a major risk for TPMS damage. “If the tire is not feeding into the drop center properly it may mount 180 degrees behind where it should and perhaps catch the TPMS sensor.”
Almost every tire changer sold in America has plenty of press aids, according to Liebetreu. “Operators sometimes think they are saving time by not using the press aids, but if you look at how much time gets wasted with the tire stalling and being partially mounted and then having to be partially demounted and restarted, the incremental gains from not using it are lost.”
3. Mounting mistake: Not adjusting for clad wheels
Although not as plentiful as five years ago, clad wheels are still found on many vehicles. The plastic face of the clad wheel can reach the edge of the tire.
“All of your machine interfaces where you might be doing work on that rim when you are in the tire changing process are at risk. You can adjust for it and the machines are fully capable of it. In fact, we’ve changed our mount head design to be very forgiving for clad wheels. But if you don’t identify the clad wheel, you can’t take the countermeasures.”
Innovating an error-proof process
“The future of mounting and balancing is a continuation of error-proofing the process with the equipment as much as possible,” says Pete Liebetreu, vice president of marketing for Hunter Engineering.
What does that mean for a shop? “More sensors, more cameras, more machine vision, knowing what the wheel is, understanding what the wheel is, and automation wherever possible to make sure processes, where they can be formalized, are followed,” explains Liebetreu.
Hunter has been innovating tire service technologies since 1946. “We like error-proofing as an operational philosophy. If you can pull decision points away from the technician, it makes his life easier, and it means a more consistent outcome.”
4. Mounting mistake: Internally clamping a black wheel
Table top tire changers quickly and easily grab wheels but leave marks on the inside of open spoke black wheels. “If you leave a bite mark and break the black paint or powder coating off the inside a black wheel with an open spoke design, the vehicle owner will be able to see it,” says Liebetreu.
5. Balancing mistake: Careless weight placement
Large wheels create problems when positioning clip-on weights. If the wheel is large, it is hard for the operator to tell if he is placing the weight straight above the spindle. Some Hunter balancers are equipped with lasers that show where to place a weight.
But non-clip applications involving tape weights are an extra challenge.
“A lot of operators use the balancer’s automatic weight placement. If you are doing a tape weight on the inner plane, it will be pretty far against the spokes, but certain wheel profiles make it tricky,” says Liebetreu. The outer plane is closest to the operator and usually easier to do. “But sometimes folks put the weight in crooked or off a few degrees. The problem is the closer those weight planes get together on a wide wheel, the harder it is to get the answer right.”
Liebetreu says the Road Force Elite balancer displays a realistic image of the inside of the wheel on a screen, showing operators where to place the weight.
6. Balancing mistake: Not centering the wheel on the balancer
Sometimes worn equipment or cones cause a tire to not center correctly on a balancer. But usually failure to center the tire is due to shortcuts and poor practices. Front coning is a big culprit. The back of almost all wheels is machined for centering while the front of the wheel is to be used for the center cap.
“Make sure you are using the back side of the wheel when centering,” says Liebetreu. “We sort of designed around that with our collet system. Collets are lower taper, more direct fitting for each wheel.”
Liebetreu says Hunter Road Force Elite balancers, which are equipped with cameras, can spot a lot of centering problems.
“If you have a lower-end machine you basically have to watch for that yourself or watch for a weight answer that just doesn’t seem logical. Many of our balancers have a more manual version of centering where you clamp, you rotate 180 degrees and reclamp. If you get the same answer for the balancer then you know it is the wheel that is out of round. If you get a different answer then you know the clamping is the problem.”
7. Balancing mistake: Not using a flange plate on a clad wheel
The risk of damaging a clad wheel is greater on a wheel balancer than on a tire changing machine. “If you don’t use a flange plate, if you just clamp on to that plastic wheel face, you are going to damage it. And you are not going to get a good clamp because that plastic is just going to give,” says Liebetreu.
Liebetreu shared ways to avoid the most common mounting and balancing mistakes during Modern Tire Dealer’s recent visit to Hunter’s headquarters in Bridgeton, Mo.
We also asked other manufacturers of mounting and balancing equipment to address common problems. The respondents were Dave Scribner, product development manager at CEMB USA/BL Systems Inc., Don Vanderheyden, director of marketing at Hennessy Industries Inc., and Kevin Jones, wheel service product manager for the Rotary wheel service division of Vehicle Service Group.
Tips from CEMB USA
Scribner outlined ways to prevent five common tire mounting mistakes as well as four balancing mistakes.
8. Mounting mistake: Inside clamping alloy wheels
On table top tire changers, avoid using clamping jaw teeth to inside clamp alloy wheels, which damages the rim. “Always outside clamp alloy wheels. Bead press systems are much easier to push the wheel downwards with the tire bead loosened when it is outside clamped,” says Scribner.
9. Mounting mistake: Reversed wheels clamped facing upwards
To prevent tire and rim damage, reversed drop center wheels can only be demounted and mounted when clamped upside down so the drop center balcony side is closest to the flange always facing upwards. “A wheel with negative offset is always suspect,” says Scribner. “Look inside the tire when bead loosening and find the drop center while lubricating the tire using a liquid lube and preparing the wheel for demounting.”
10. Mounting mistake: Too much or too little lubrication
Scribner recommends a lubrication product that is a vegetable oil-based paste with a short shelf life applied by a brush. Lubricate the rim barrel, rim drop center balcony edge and bead toe edge area. Avoid rim bead seats and tire beads.
“Do not use too much lubrication to prevent tire slippage. Index the inner tire sidewall to the rim edge when done balancing to be able to check for rim to tire slippage if vehicle returns. Too little lube and the tire doesn’t seat properly, and eccentricity problems can cause ride disturbance issues.”
11. Mounting mistake: Failure to identify, pretest and reprogram TPMS
If the TPMS sensor is at the valve, it has the potential to be damaged. “Test and make notation that TPMS sensors are working before service. This will protect you from customer accusations that you damaged their TPMS,” says Scribner.
12. Mounting mistake: Failure to minimize wheel RFV eccentricity
Scribner says to reduce RFV (radial force vectoring) eccentricity and provide a smoother ride, use a tire rapid inflation technique as recommended best practice by many tire manufacturers. The three steps are 1) with the valve core removed, perform a rapid seal, seating and inflation, 2) deflate the tire, 3) re-inflate the tire and install the valve core and bring air pressure to placard inflation pressure.
13. Balancing mistake: Failure to validate the wheel is centered
Back-cone mount and use a flange plate from the front whenever possible to best center the wheel. Some very wide wheels and larger light truck wheels may require spacers and larger cones to be front cone mounted. When in doubt, use a centering repeatability check to validate the wheel is centered.
“To validate the wheel is centered, the process is simple, mostly unknown and rarely done,” says Scribner. Clamp the wheel and take a balance measurement. Note the location and the amount of weight required to balance the wheel. Unclamp the wheel and reposition the adaptors and the wheel to a different clock position, reclamp the wheel. Take a second balance measurement. The weight amount and location should repeat closely to within the smallest round-off incremental size of wheel weight used.
14. Balancing mistake: Hidden residual static imbalance
Scribner says most wheel balancers use dated software with fixed dynamic blinding of 0.29 ounces per plane often displaying “0.00oz__0.00oz” when residual static imbalance can be as high as 0.58 ounces. He says the best solution is static minimization software, which compensates automatically and eliminates residual static by shifting weights to reduce residual static imbalance lower than the round-off setting.
The “okay” solution involves the use of a third static residual weight display, if available, allowing the operator to add a third weight or shift weights. The “poor” solution is to balance in a “fine mode” to lower than lowest round-off increment.
15. Balancing mistake: Failure to address RFV eccentricity
When using a wheel balancer with RFV eccentricity (non-uniformity) measurement capability, check RFV eccentricity, minimize if needed and mark the high-spot of the assembly. Unless the tires are new, before measurement the vehicle should be driven about 10 miles to remove any temporary flat spots. Sensitive vehicle should be less than approximately 0.025 inches R1H (radial 1st harmonic of runout), less sensitive vehicles up to approximately 0.040 inches. If limits are high, remove the assembly, loosen the beads, lubricate the tire, rotate 180 degrees, re-inflate and remeasure.
16. Balancing mistake: Random wheel-to-vehicle hub mounting
Once the assembly is off the balancer, placing the assembly back on the vehicle hub with the high point (R1H radial runout) is another opportunity for improving ride quality. The idea behind the hub pilot is the hub-to-hub bore fit is supposed to center the wheel.
“The fact is it is often much too loose and the clearances are enough to allow gravity to shift the weight of the wheel to rest only on the upper part of the hub creating a gap in the bottom. Even the smallest gaps result in an egg-shaped motion upon rotation that can cause huge errors in imbalance and run-out eccentricity stacking that causes tire force vibration.” Scribner says the company’s HubMatch wheel mounting helps reduce eccentricity by subtracting the high point of the assembly from the hub bore clearance of the wheel to the axle hub.
Tips from Hennessy Industries
Vanderheyden specified six tire mounting and balancing errors that impact ride quality.
17. Mounting mistake: clamping from inside
Many technicians clamp wheels from the inside, which can cause the jaws to leave marks on the inside of alloy and steel wheels. Today’s wheels, whether alloy or steel, should only be clamped from the outside in. “This not only prevents the wheel from shifting or walking during demount, it can also stop the wheel from spinning on the clamps during mounting of the top bead. Using a rim clamp tire machine equipped with a protected jaw such as Grip-Max Plus Clamps alleviates this issue,” says Vanderheyden.
18. Mounting mistake: Metal-to-metal contact
When changing a tire on a wheel with black paint or powder coating, having the mount demount head adjusted properly along with using a poly head instead of metal is a great way to eliminate metal-to-metal contact that can scratch or mar coated or painted wheels. This is a very common and costly mistake and is easily avoidable by using the correct technique and accessories.
19. Mounting mistake: Incorrect use of bead loosener
When using a side-mounted bead loosener, in the interest of speed, many technicians will place the side shovel too far from the bead of the tire, which can cause tire damage. Technicians may also place the shovel too close to a TPMS sensor causing breakage. Paying close attention to the position of the bead loosener relative to the wheel assembly is critical.
“A precise bead loosener that is hand controlled and has power in and out control gives the user a great amount of control when loosening beads, eliminating these types of issues,” says Vanderheyden.
20. Balancing mistake: Failing to center the wheel
Centering the wheel on the balancer is the critical first step to success in wheel balancing. Unfortunately, it is also the most common step to be overlooked.
Vanderheyden recommends collets instead of cones. “Wheels should be centered from the inside hub bore center only, not from the outside or against the hub nut. This ensures that the wheel is centered the same way it centers when it is on the vehicle.”
21. Balancing mistake: Not using pin plates
Pin plates or flange plates are a necessity to protect plastic cladded wheels and to center heavy truck wheels. A pin plate utilizes the wheel’s lug holes to be certain that even force is applied against the outside of the wheel when mounting in order to aid in centering. For heavy wheels, it allows the wheel to “climb” the collet uniformly to make centering on the tooling a snap.
22. Balancing mistake: Not correcting residual imbalance
When balancing certain assemblies in dynamic mode, a certain amount of residual static forces can be created inadvertently; this can cause a vibration or customer comeback.
“A balancer that can quickly identify this residual imbalance and prompt the user to correct it before the tire is mounted back on the vehicle is a necessity for today’s vibration-prone vehicles. Counter balancing all static and dynamic forces down as low as possible is a requirement,” says Vanderheyden.
Tires won’t balance? Here’s why
Hennessy Industries breaks down the causes of improper balancing in tire shops into the following percentages:
- Improper centering 60%
- Residual static unbalance 10%
- Improper wheel weight usage 7%
- Drive train vibration 6%
- Balancer calibration 5%
- Eccentricity problem 5%
- Improper lug nut torque 4%
- Bent wheel rim 2%
- Other 1%
(Included in “Other” is force variation at .05%.)
Tips from Rotary
Jones offered ways to avoid six mistakes that occur most often in the mounting and balancing process.
23. Mounting mistake: TPMS damage
TPMS damage often occurs because the technician does not pay attention to where the TPMS is located before starting to demount or mount the tire. “A simple check can easily help avoid this issue,” says Jones.
24. Mounting mistake: Incorrect clamping which causes wheel damage
“All aluminum wheels should be externally clamped, but often what we see is that technicians will try to save time by internally clamping the wheel,” says Jones. This causes scratches on the inside of the wheels. Using a center clamping changer will prevent this type of damage.
25. Mounting mistake: Not using lube when demounting
“Almost every operator I see does not use lube when demounting a tire,” says Jones. “They say it takes too long to apply lube, but then they struggle to get the tire off the wheel, which costs them time and can damage the tire.”
It’s important to use the right amount of lube, too. “When you don’t use enough, you can damage the tire and wheel. If you use too much, you can create tire-to-wheel slippage and encounter vibration problems.”
26. Balancing mistake: Mis-mounting the wheel on the balancer
With today’s plastic and/or chrome clad wheels, shops that use cones to center the wheel on the balancer will experience balancing issues.
Collets are a better solution for servicing OE wheels or when working on clad wheels. “The collet is shorter and doesn’t go as deep into the hub bore of the wheel. Collets, along with finger plates, which replace the standard pressure cup, help provide even more mounting accuracy,” says Jones.
27. Balancing mistake: Front coning instead of back coning
“All wheels should be back coned; that is, the cone/collet should be placed on the shaft first, then the wheel, then the finger plate or pressure cup then the wing nut,” says Jones.
Most aluminum wheels have a taper on the back of the hub bore that helps center the wheel on the collet. If an operator is front coning, the shop will likely see that car back in the shop more frequently with balancing issues because the front of the wheel is not designed to accept a cone or collet.
28. Balancing mistake: Incorrect weight placement
Most aftermarket wheels and many OE wheels today require stick-on weights for balancing. These weights must be placed inside the wheel at the proper location.
Using a balancer with a laser line or pointer to indicate the weight location can help the operator place the weight in the precise location. Just a slight miscalculation in weight location can cause the balancer to be off and call for more weight.
“Additionally, many of today’s aftermarket wheels for light-duty trucks have an offset that is so negative that the only balancing mode available is static which uses only one weight, so correct weight placement is important,” says Jones.
About the Author
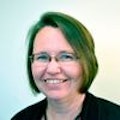
Ann Neal
Ann Neal is a former senior editor at Modern Tire Dealer.