Now that diesel fuel is more expensive than ever, fleets are looking for every possible way to control their operating expenses. This means that companies that were previously resistant to tire repair programs may be suddenly interested in exploring repair options. Unfortunately, there are a number of definitions of the word “repair.”
According to the Rubber Manufacturers Association (RMA) and the Tire Industry Association (TIA), there is only one recognized method for repairing tires. This method includes specific guidelines for the location and size of the injury, in addition to step-by-step procedures for effectively restoring the original condition of the casing.
With more fleets starting to understand the actual value of a truck tire after the original tread has been worn away, commercial tire dealers will be expected to preserve the integrity of the tire so it can be retreaded multiple times.
Location, location, location
Just like real estate, the key to advanced tire repair starts with location. The official RMA/TIA stance is that the injury must be located in the crown area of the tire. (The crown is the region in the center of the tread that extends approximately one to 1.5 inches in from each shoulder.)
The shoulder of the tread outside the crown area is the location of the belt edge, which is the most vulnerable spot for tread separations following a puncture.
As the tire adapts to the road while in motion, the belt edges tend to generate a tremendous amount of heat as they flex, especially when under-inflated. When everything is sound and the inflation pressure is correct, all of the wire strands that comprise the cables that make up the belt package stay in place.
The outermost shoulder is an extremely sensitive area on a truck tire; all it takes is one stray wire on one previously damaged cable to create enough movement that eventually separates the entire belt package from the casing. Any repairs in this area must be approached carefully to ensure that all of the damage has been removed. That’s why standard “plug and patch” methods are not recommended in the shoulder.
[PAGEBREAK]
Sizing it up
After the issue of location has been addressed, technicians must consider the size of the injury.
In order to perform an advanced repair of a puncture in the crown area with standard “nail hole” repair materials, the damage cannot exceed 3/8-inch in diameter. If the injury is larger than 3/8-inch, then the tire must be referred to a full-service tire repair facility for a section repair.
Section repairs require special tools to remove all of the surrounding rubber and steel that has been damaged by the penetrating object. Once the damage has been removed, the area is filled with raw, uncured rubber and the inside of the tire is reinforced with a repair unit. The rubber is then heated under pressure so it vulcanizes with the surrounding tire.
It requires a significant investment in tools, equipment and training to perform section repairs, so commercial tire dealers who are interested in getting into this part of the business must assure themselves there will be enough demand to justify the expenses. They also must make sure they have employees who are capable and also possess the necessary attention to detail that section repairs demand.
Drill and fill
The lion’s share of the truck tire repair business will always be the standard nail hole or puncture repair located in the crown area where damage can be removed with a carbide cutter.
Tool speed (recommended 1,200 rpm or less) is important when using the carbide cutter for a number of reasons, but the most important is the danger of scorched rubber, which will not vulcanize with repair materials. While scorched rubber is difficult to locate, the best method is to look for smoke during the injury removal process. If the cutter is generating smoke as it removes the damage, scorch is likely present.
Once all of the damage has been removed, it’s necessary to fill the void with rubber. The most effective method is to insert a cured rubber stem, or plug. However, the ancient (and dangerous) practice of using a fabric insert, or string plug, somehow continues to survive in certain parts of the country. Advanced tire repair procedures for both the RMA and TIA specifically call for a rubber insert; anything short of that practice would be considered outside industry guidelines.
While we’re on the subject of being outside industry guidelines, nothing is more frustrating than a “patch-only” repair. Unlike the typical outside-in string plug installation, the patch-only approach requires the technician to perform every step, except the removal of the damage and the filling of the injury. In the short term, these repairs are often very effective, but the long-term consequences include creation of a path for water and moisture, which attack the belt packages and body cables. Over time, the rust in the injury grows and eventually results in a belt separation. Commercial tire dealers who patch tires without removing the damage or filling the injury are rolling the dice with every repair. If the practice is ever scrutinized in a courtroom, the jury will see that every industry organization -- including the RMA and TIA -- as well as tire manufacturers are against patch-only repairs, no matter how small the injury may be.
[PAGEBREAK]
Keep it clean
Another aspect of advanced tire repair that’s often overlooked and misunderstood is the cleaning of the inner liner.
First and foremost, release lubricants used on the inside of a tire during the manufacturing process must be removed because lubricants keep things from sticking. Advances in tire repair materials have created adhesion values that far exceed the minimums because they have to account for the hundreds, if not thousands, of tire dealers who do not clean the inner liner prior to performing a repair.
To make matters worse, most inner liner cleaners are designed and labeled as “pre-buff cleaners,” which means the cleaning should take place before the buffing process. However, I have consistently seen people use pre-buff cleaner on the buffed inner liner.
If a jury ever finds out that pre-buff cleaner was used on the buffed inner liner of a tire that experienced a repair failure, it will not be pretty.
Speaking of buffing and looking pretty, you want to create a smooth and uniform surface for the repair unit. Poor technique, worn buffing wheels and stones, improper tool speed and general carelessness are just some of the factors that will result in an improperly buffed inner liner.
An RMA #1 or #2 velvet-like texture is the most desired surface following the buffing process. Buffed surfaces where the mold design is still evident or the buffing extends past the inner liner to expose the body cords are destined to fail following installation of the repair unit.
Remember that before the repair unit can be installed, vulcanizing cement must be applied to the buffed surface.
The most important thing to remember about cement is that the thin coat must be completely dry before installing the patch.
[PAGEBREAK]
‘Minimal liability’
As some of you may have guessed by now, advanced nail hole repairs are defined when all of the recommended procedures and guidelines are followed. That means the location and size of the injury are considered and the main components of a proper repair are in place.
When injuries in the crown area that are 3/8-inch or less are prepared with a carbide cutter, filled with a rubber stem, and repaired with a patch on the inside, the original condition of the casing is restored.
When nail hole repairs are installed in the shoulder or the damage exceeds 3/8 of an inch, the tire may hold air immediately following the repair, but it’s just a matter of time before the tire fails or is rejected during the retreading process.
For those commercial tire dealers who follow the guidelines for advanced tire repairs, there should be minimal liability and few repair-related problems to deal with.
This article is part of an exclusive on-going series written for CTD by Kevin Rohlwing, senior vice president of training for the Tire Industry Association.
About the Author
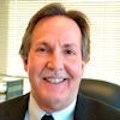
Bob Ulrich
Bob Ulrich was named Modern Tire Dealer editor in August 2000 and retired in January 2020. He joined the magazine in 1985 as assistant editor, and had been responsible for gathering statistical information for MTD's "Facts Issue" since 1993. He won numerous awards for editorial and feature writing, including five gold medals from the International Automotive Media Association. Bob earned a B.A. in English literature from Ohio Northern University and has a law degree from the University of Akron.