Independent tire dealers account for more than $5 billion of the suspension service work performed in the U.S. That averages out to yearly sales of $189,000 for any tire dealer who offers both chassis/suspension service ($125,459) and shock and strut replacement ($62,379).
Many high-end vehicles use air suspension systems that feature a lot of moving parts your technicians may not be used to servicing. Mike Mavrigian, editor of Modern Tire Dealer’s sister publication, Auto Service Professional, explains how to service this niche system with the help of KnowYourParts.com, the industry information campaign of the Automotive Aftermarket Suppliers Association.
Just about every Asian and European luxury import nameplate manufacturer has a seven- to 10-year-old vehicle on the road with an air suspension at all four corners. Chances are one of these vehicles will be coming to your shop sooner rather than later.
Regardless of the nationality of the automaker, most of the systems use German-manufactured air struts connected to a WABCO (Westinghouse Air Brake Co.) compressor. In between the struts and compressor are reservoirs, control valves and a lot of software controlling the system. The secret to diagnosing problems comes down to knowing what criteria the system uses to regulate the compressor/reservoir and having a scan tool that can interpret the information.
These systems do not use the compressor to directly fill the air bladders. Instead, the compressor will supply air to a reservoir that is used to fill the bladders. Some vehicles, like Land Rovers and Jaguars, will have only one reservoir, while some Mercedes or BMWs may have multiple reservoirs. The reservoir is equipped with a pressure sensor and valves to send compressed air to the spring and exhaust excess pressure.
Do not work on any reservoir unless the system is allowed to depressurize before performing any repairs. Some systems may require the use of a scan tool to release the pressure and re-pressurize the system.
The reservoirs are typically made of aluminum. They can be located in the trunk or tucked behind fenders or quarter panels. It is rare for the tank to develop a leak, but it is common for the air-line connections.
Air suspension systems look for information like vehicle speed, ambient air temperature and ride height. From this information, a system can calculate how long the compressor should run to fill the reservoir. If it is taking too long to fill a reservoir, the air-ride module will set a code, alert the driver, and put the system in a safe mode.
The codes for this type of problem will typically include the words “replenish,” “reservoir,” “overheat,” “no pressure increase” or “timed out.” There are two main culprits for these codes — a weak compressor or a leak in the system. It is possible that a sensor in the reservoir is faulty, but this is extremely rare.
All air suspension systems are unable to do two things. First, they can’t measure wear in the compressor. As a compressor runs, the ring wears and the compressor is unable to generate enough pressure to operate the system. The control module can’t measure the wear on the ring. Second, air-ride systems can’t detect leaks in the system.
However, what air suspension systems are able to measure is compressor run time.
The control module will not immediately turn on the compressor when the engine is started and will trim the suspension from the air in the reservoir. Some systems will not engage the compressor until the vehicle has reached a predetermined speed like 25 mph. These rules are in place so moving air will cool the compressor. That way, the driver will not notice the compressor operating while the vehicle is stopped. But, in some cases, the compressor will run during startup if the pressure is low enough.
All four-corner systems are using air from the reservoir even if the car is parked. This is because as the vehicle cools, the air volume and pressure in the bladders and reservoir will decrease. The system will trim the ride height to make sure the vehicle is not sitting on the ground when the driver returns to the vehicle in the morning.
Also, some systems will keep a level ride height if the vehicle is parked on an uneven surface, or the vehicle is unlocked and a load is placed in the trunk. But, most systems will never turn on the compressor to make a key-off correction.
Most systems have fail-safe modes that preserve the system until it can be serviced. This means that the control module will not allow the compressor to meltdown if there is a leak. Also, most units will maintain minimum pressure or height in order to prevent a bladder from fully compressing and the suspension from bottoming out.
Before a vehicle is returned to a customer, you should perform a calibration procedure for the air suspension system, if required. Calibration procedures typically involve measuring the four ride heights and entering the data into the scan tool. Not performing this procedure can lead to a comeback. ■
About the Author
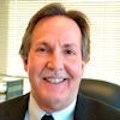
Bob Ulrich
Bob Ulrich was named Modern Tire Dealer editor in August 2000 and retired in January 2020. He joined the magazine in 1985 as assistant editor, and had been responsible for gathering statistical information for MTD's "Facts Issue" since 1993. He won numerous awards for editorial and feature writing, including five gold medals from the International Automotive Media Association. Bob earned a B.A. in English literature from Ohio Northern University and has a law degree from the University of Akron.