The issue of proper torque and how to obtain it is critical for the proper installation of wheels.
When tightening any series of wheel fasteners, the degree of tightening in order to achieve proper clamping load must be considered. In addition, pay attention to the tightening sequence, or pattern, to assure that clamping loads are evenly distributed across the hub contact area.
Threaded fasteners, by design, are intended to stretch slightly when fully tightened to specification. This creates a preload, which serves to clamp the wheel securely to the hub. If under-tightened, the nut (or bolt) can gradually loosen. If over-tightened, the stud or bolt can exceed its "elastic" range, and be permanently stretched (fatigued), which destroys its ability to provide clamping load. If this happens, the stud or bolt can either loosen on its own or can break during operation.
Severe wheel vibrations under braking can occur if wheels are improperly or unevenly tightened -- especially when you are dealing with today´s lightweight alloy wheels and sometimes light (and thin) rotor hats. This leads us to the topic of torque wrenches.
Trying to convince everyone to take the time to use a torque wrench when tightening wheel fasteners is akin to pulling teeth. This may not be what the busy shop wants to hear, but when installing custom alloy wheels, always use a torque wrench. While with some OE jobs an impact gun (or an impact gun with a torque stick)may be used, custom alloys require a torque wrench to do the job the right way.
[PAGEBREAK]
REASONS NOT TO USE AN IMPACT GUN
There are several reasons not to use an impact gun on custom alloys:
1. Fastener damage: It´s sometimes too easy to chip the chrome plating and to burr the hex edges of the nut or bolt head, especially if an ill-fitting socket is used.
2. More fastener damage: If there are tuner nuts that feature female hex drives, it´s way too easy to damage the hex hole. If the nut features a spline drive, the chrome can be knocked off of the spline edges.
3. Inaccurate torque: Chances are your compressor is set at 100 psi or more. If the wheel fasteners specify 85 ft.-lbs., final clamping force will never be certain, even if the gun is regulated. Plus, the amount of gun dwell time it takes to work on each fastener will probably differ, which aggravates the problem by resulting in uneven tightening from fastener to fastener.
4. Wheel damage: If socket-to-fastener recess is minimal, or if a thick-walled socket is used that minimizes clearance, the outer wall of the socket can abrade against the fastener recess. If the socket is dirty, abrasive damage to both the fastener and wheel is possible. Where appearance is important, ditch the impact gun and use a torque wrench. Impact tightening also can cause the seat contact area of the wheel to gall as the nut or bolt seat is pounded and ground into the aluminum wheel.
5. Excessive or uneven tightening can warp the wheel, hub or rotor hat, which will lead to vibration complaints.
6. Excessive tightening can cause the nut or bolt seat to pound into the aluminum wheel´s seat pocket, displacing the aluminum (gouging/deforming the alloy). This eventually can lead to fastener loosening, since the seat base integrity has been deformed or reduced.
7. Excessive tightening can stress the wheel stud (or bolt shank), permanently stretching the thread shank beyond its elastic point and weakening the threads considerably. When this happens, the stud (or bolt) eventually may break or allow the nut (or bolt) to loosen.
Tighter is not better. Always follow the torque specifications listed by either the vehicle manufacturer or the wheel maker.
[PAGEBREAK]
FASTENER PREP
First, make sure the threads are clean and free of dirt, grease, grit, etc. Inspect all threads for condition. If burrs or flat spots are found, replace the fastener (whether a nut, bolt or stud).
Most tightening specifications are listed based on dry (no lubricant) threads. Applying oil, grease or moly to the threads will result in inaccurate torque values, as this likely will result in over-tightening.
Even if aluminum wheel nuts are used (which are popular in some racing situations, Porsche applications, etc.), the advice is the same. Simply make sure the threads are clean and dry. Aluminum wheel nuts are typically made from a very dense, strong 7075 alloy, and will function properly if handled correctly. Even though a light coating of lubricant on the fastener seat may aid in achieving proper torque, don´t be tempted to apply this, because any excess (resulting from brake heat and centrifugal force) may migrate out onto the wheel face.
TO RETORQUE OR NOT TO RETORQUE
There are two schools of thought regarding the need to retorque wheel fasteners. We´ll ignore one of these and focus on the correct method.
While it´s possible to "get away" without retorquing, the right approach is to retorque each wheel fastener (in sequence) following the first 50 to 100 miles or so of operation. Because of a concern for potential metal compression/elongation and thermal stresses, the wheel clamping loads may change during initial use, so it´s simply a good idea to re-check.
In order to retorque, first wait for the wheels to cool to ambient temperature. Then, loosen and retighten each fastener to specified value, in sequence.
[PAGEBREAK]
TORQUE WRENCH TIPS
Micrometer type ("click" type) ratcheting torque wrenches can and do go out of calibration over time, resulting in inaccurate tightening values. It´s a good idea to send your torque wrenches out for recalibration once or twice per year, depending on use. Several calibration service houses across the U.S. offer this service, and the cost is usually only about $25 or so.
When tightening a fastener with a torque wrench, approach the tightening value slowly. Avoid yanking the wrench -- by tugging on the wrench too quickly and abruptly, chances are good that the pre-set value will be passed by a few pounds. For accuracy and repeatability, use the torque wrench slowly. Use a smooth, controlled pull. Once a preset warning is heard/felt, stop.
Do not use a torque wrench as an installer or remover. Only use the torque wrench for achieving final clamping value. While the wrench may provide a ratcheting feature, it is not intended to be used as a general service wrench. Install and snug fasteners by hand or with a general service wrench, then use the torque wrench to gain final value. This will help to maintain calibration and will provide longer tool life.
Also, pay attention to torque wrench labels and instructions. Some torque wrenches are designed for both right-hand (clockwise) and left-hand (counterclockwise) operation, and some are designed only for right-hand operation. If you attempt to use a right-hand-only torque wrench to loosen fasteners, this can quickly cause a calibration problem.
Don´t treat torque wrenches like other tools. They´re not emergency hammers or pry bars. They are delicate instruments and are to be treated as such. Buy a good quality torque wrench and care for the tool properly. It will pay off.
A torque wrench is only useful if properly calibrated to provide accurate and repeatable tightening values. Otherwise, it´s an expensive paperweight.
WHEEL AND FASTENER INSTALLATION TIPS
1. Never mismatch nut or bolt seat styles. Seat matching is absolutely critical for safe and effective wheel installation. For example, if the wheel features ball type (radius) seat pockets, you must use only ball type fasteners. Using the wrong seat style will have dire consequences. At the least, the wheel will be damaged. At the worst, the wheel will separate from the vehicle.
2. Make sure that there is no grease, snow, ice, etc., lodged inside a closed nut. When tightened, this can create a hydraulic lock, causing the stud tip to bottom out against this material. If the nut roof bottoms out on its stud, the nut seat will not achieve adequate clamping force. And clamping force is the name of the game -- it´s what secures the wheel to the hub.
3. Inspect the hub face for surface contaminants such as dirt, rocks, grease, etc. The hub face should be clean and smooth to provide an even, aligned mating surface for the wheel.
4. Avoid mixing inch and metric fasteners. Just because a nut can be threaded into place does not mean that correct thread engagement has taken place. If threads are not compatible, the fastener will install at an angle, or it may seize, or it may damage (and weaken) threads. If in doubt, use a thread pitch gauge and sizing card to verify correct size. Remember: Whenever a wheel is installed, somebody´s life is at stake. This is no time to make a mistake.
5. Apply a very thin coating of an anti-seize paste to the hub face where the wheel makes contact to avoid corrosion that may cause an alloy wheel to "stick" to a steel or iron hub. Don´t apply too much, because any excess can sling out as a result of centrifugal force and contaminate the wheel face or brake surfaces. A thin coating of this compound will make it easy to remove the wheels in the future.
As we mentioned earlier, don´t apply lubricant to fastener threads, since fastener torque specification values are based on the use of clean, dry threads. By lubricating the threads with a slippery substance, inaccurate (usually too high) torque values may be obtained.
About the Author
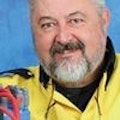
Mike Mavrigian
Longtime automotive industry journalist and Modern Tire Dealer contributor Mike Mavrigian also is the editor of MTD’s sister publication, Auto Service Professional. Mavrigian received a bachelors degree from Youngstown State University in English literature with a minor in journalism in 1975.