Craig Bruneel’s father offered his son wisdom that still guides Craig as he runs the Bruneel family’s tire dealership, which has stores throughout Oregon and Idaho.
“My Dad used to always tell stories of how he and his partner would have to go out on service calls together, so that one could hold a large tire iron wedged against the truck compressor pulley somehow to keep the compressor working.
“The point (was) that in order to do our work properly and efficiently, we need the tools to do so. I have always tried to keep good working equipment so that our staff can be efficient, safe and productive.”
Having the right equipment can mean the difference between a store that is doing well or a store that is struggling.
Is it better to repair existing equipment or buy new equipment? And what are some guideposts dealers should use as they make these decisions?
Bruneel, who is president of Bruneel Point S Tire & Auto, a 12-store chain based in Boise, Idaho, says his team has a process that it follows when looking to replace rather than repair shop equipment like tire changers, balancers and vehicle lifts.
“We have each location manager monitor equipment for performance issues and repair concerns.
“Usually, when a piece of equipment is older, we look at replacing versus repair. Of course, the locations that take better care of equipment have longer (equipment) life.”
That’s where a good process helps guide the repair or replace decision, while helping stores stay within budget. “If a location manager thinks it may be time to replace versus repair, we have a corporate position with oversight to review the situation and make purchases, if necessary.”
Bruneel Tire follows other guidelines. “We do not have a schedule for replacement related to time, (but) usually more of the condition of the equipment and the cost of repair versus purchase. We do compare the usual life of equipment in our organization. I expect a tire balancer to last from seven to 11 years, hoists 12 to 25 years and tire machines five to nine years.”
Bruneel counts on employees to own the process.
“Managers, who are accountable for (and are) bonused on profits, give input to repair versus purchase.
“They instigate the purchase review process on larger purchases — anything over $1,000.”
Best practices and guidelines
MTD recently took the “repair or replace” question to equipment manufacturers — focusing on companies that supply tire changers, balancers and lifts — and asked, “When should a tire dealer replace equipment? Is there a timetable or are there guidelines?”
Here’s what representatives from each company had to say. (Answers are arranged in alphabetical order, based on company name):
Chuck McCourt, president, Base USA Corp. (Accu-Turn): For high-volume shops, use five years as a template. (For) medium-volume, seven years and low-volume, 10 years.
Robert Ladosky, product specialist, Bend-Pak Inc. (Dannmar): High-quality vehicle lifts and wheel service equipment can perform for many years if they’re properly maintained and used correctly.
For lifts, an Automotive Lift Institute (ALI)-certified lift inspector should perform a Check360 Certified Lift Inspection on every vehicle lift in your shop each year. This inspection will identify any areas of concern on your lifts, including necessary repairs and whether any lifts should be removed from service.
For wheel service equipment, we recommend making a thorough inspection of equipment every month and replacing any damaged or severely worn parts as they are identified.
In many cases, the replacement cycle for large equipment like this is dictated more by functionality than disrepair. For example, a shop that wants to expand its business beyond passenger vehicles to include work trucks will need to invest in a lift with a higher-rated capacity, as well as wheel changers and tire balancers that can efficiently handle larger wheels and tires.
Fabian Martinez, sales development manager, southwest, for CEMB-USA: This is a question that many dealers struggle with because this type of financial decision can have short-term and long-term financial effects on the business. While there is no one, recommended timetable, a dealer must always be forward-looking to ensure that they are able to replace or repair the equipment when it is required. The best shops budget for this expense in advance. They do this by reserving capital at a rate that is (commensurate) with an amortization schedule for their existing equipment and the revenue generated by the equipment.
Usually, a percentage of the replacement value for each piece in use — based on a life expectancy of five to seven years, depending on the current condition of the equipment — is sufficient.
As a (dealership) owner evaluating when equipment should be replaced, there are several factors that should generally be considered:
Safety: Since the most valuable assets of an owner are his technicians and staff, if a piece of equipment has the potential to be a safety hazard, it must be repaired and if repairs are not possible or not cost-effective, then replacement is required.
Serviceability: If the cost of lost opportunity exceeds the cost of repairs, then the equipment should be replaced.
Relevance: If the equipment as it exists is damaging to your brand or profits, then it must be upgraded or replaced. Tire fitments and rim configurations have changed dramatically in the last 10 years and they will continue to evolve.
Profitability: What is the return on investment on a piece of equipment? This is a question that should be asked at the beginning and before the purchase of any equipment or repair. If the timetable for the return on the investment exceeds the life expectancy of the equipment, then the equipment or repair purchase should not be made.
Kyle Harris, product manager, Hennessy Industries Inc. If a (dealership) has a tire machine that is no longer able to safely and easily service the tires that the dealership services today or wants to service in the future, (this) is a great reason to move up to a more suitable machine.
Oftentimes, balancers are replaced because they are no longer able to keep technicians as productive as a new balancer. Tire balancers have a life generally of about seven years at a busy tire shop. However, seven years is generous if you are not equipped with a modern balancer.
An ALI-certified lift inspector can always help advise a tire dealer on lift safety, but sometimes a dealership will simply outgrow a lift because it lacks the overall lift capacity they need.
It is important to evaluate your customer base’s needs to optimize the life of your vehicle lifts. For example, for alignment and drive-on lift needs, many tire dealers find that they need a lift that will support longer wheel bases or one that can lift heavier vehicles.
Pete Liebetreu, vice president of marketing, Hunter Engineering Co.: For any equipment, there are two reasons to purchase new: because your old equipment is worn-out (and) because vehicles have changed and your old equipment can no longer service the vehicles you see. But these reasons are nuanced.
If number one is your reason, shouldn’t you consider number two in your purchasing decision. If number two is your reason, don’t just consider what you need to service today’s vehicles, but also future vehicles.
Hunter makes very durable shop equipment, as evidenced by our three-year, across-the-board warranty.
Tire changers and balancers have useful lives in five to seven years in high- usage environments — much longer in moderate-usage shops. But the pace of change for tires and wheels is still very high, so there are often technological reasons to upgrade sooner.
Steve Perlstein, president of Mohawk Lifts LLC: When to replace is dependent on brand, quality and maintenance. Some lifts have a three- to four-year lifecycle and are priced as disposable items. A Mohawk Lift has a 25-year structural warranty and a 10-year mechanical parts warranty.
I believe focusing on shop productivity — getting more vehicles in and out of the shop in the same eight-hour day — makes the tire dealer more profitable.
Some lift brands save dealers time by not having to bend down and position the swing arms at each corner of a vehicle’s lifting point. Essentially, this option — offered by a few manufacturers — makes a two-post lift ... into a drive-on lift, yet leaves the tires hanging free for tire rotations, brake and front end work.
Yet another lift option to speed repairs through the shop is a tire engaging adaptor that again saves techs the few minutes needed to position the swing arms under the vehicle’s lifting points.
Kevin Jones, wheel service product manager for Vehicle Service Group (Rotary): When it comes to equipment replacement, it can vary greatly based not only on the quality of equipment purchased, but also the average use and how well the equipment is maintained. If shops aren’t doing regular inspections and maintenance on their equipment, then something minor like a bolt that needs replacing or a cable that’s not repaired could lead to a major issue down the road. When it comes to the condition of a tire changer, watch for worn-out shoe sliders, hydraulic seals and pressure bladders.
If (your) shop still has a hand-spin balancer hanging around, it may be time to consider upgrading to electric.
The potential to increase volume is reason enough, but it will also save time and strain on your techs.
Pay close attention to the wheel balancer shaft.
A worn shaft can lead to improper balancing and cost the shop lost productivity and revenue.
On hydraulic lifts, check the fluid level and quality regularly and refill/replace it as needed. Always keep lift components clean and free of corrosive agents, solvents and road de-icing chemicals.
Schedule annual lift inspections with a qualified lift inspector.
What’s new in service equipment: Changers, balancers and lifts take center stage
MTD recently asked equipment manufacturers to provide information about new products they offer. The following companies responded:
Base USA Corp. (Accu-Turn): Base USA Corp. offers new, touchless tire changers, plus wheel balancers with 19-inch video interface, touch screen and 3D, in which technicians can just touch the tire / wheel in three spots and it will automatically record the size, width and distance of the tire. The balancers also have sonar to measure radial run-out in the tire/wheel assembly.
Bend-Pak Inc. (Dannmar): Bend-Pak says the new Dannmar D2-10C symmetric, two-post lift is Automotive Lift Institute-certified and has a rated capacity of 10,000 pounds, low-pressure direct-drive cylinders for reliability and smooth operation and an adjustable top beam that can be configured for narrow or wide installation, depending on service bay lay-out.
The Dannmar DT-50A tire changer helps increase shop workflow, according to Bend-Pak officials. It has a non-tilt-back design, which means it doesn’t require extra space, and can even be installed flush to a wall. Its swing arm design lets technicians load tires quickly.
In addition, the Dannmar DB-70 automatic wheel balancer handles wheels up to 28 inches in diameter. An easy touch pad panel displays tire and wheel assembly graphics. Bright LEDs indicate the exact amount and location of weights needed in just seven seconds.
CEMB-USA: The ER75TD HubMatch balancer is one of the latest offerings from CEMB-USA. This unit will perform all balancing functions required and also uses innovative solutions to deal with eccentricity issues. The AutoAdaptive mode uses proprietary methods to cancel vibrations that might be felt on the steering wheel. CEMB’s one plane balancing system saves time and money by canceling static vibrations and minimizing residual dynamic values.
The EZ10 and EZ15 from CEMB can help dealers who are space-restricted. The ER100EVO is CEMB’s most comprehensive wheel service balancer.
The SM628BPS is the company’s newest and most robust tire changer. It comes with a three-contact point articulating bead press system meant to handle difficult fitments.
Hennessy Industries Inc.: Hennessy’s new tire changer, the Coats 80C, clamps the wheel with a large center wing nut, eliminating damage from jaws. The machine has a swing arm design that is easy to set up and robust enough to handle even the highest through-put. Hennessy says the design is simpler than a rim clamp and uses fewer moving parts for less maintenance and long service life.
Hunter Engineering Co. Hunter’s new L494HD is a 35,000-pound, heavy-duty, four-post lift. The L494HD features galvanized runways capable of servicing vehicles with up to a 320-inch wheelbase.
Hunter’s TCX58 and TCX59 table-top tire changers feature the company’s FastBlast hands-free blast inflation for difficult-to-seat truck and SUV tires. The TCX58 and TCX59 are equipped with features set specifically for those tire types.
Hunter officials say the company’s new Auto34R is the easiest to use and highest-performing variation of the popular center clamp tire changer.
Vehicle Service Group (Rotary): The new Rotary R1200 Leverless Pro Tire Changer is designed to address some of the common challenges facing tire dealers. Packed with innovative, easy-to-use features and designed with automated and intuitive controls, the R1200 helps technicians cut repair time, increase accuracy and more easily change high-performance tires and rims without causing damage.
The new Rotary R1065 Tablet-Operated Wheel Alignment System is space-efficient. Its tower-free design requires no minimum bay size and it comes with a portable, compact cart with built-in sensor chargers.
About the Author
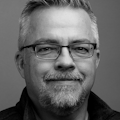
Ron Ledgard
Managing Editor
Ron Ledgard is the managing editor for Modern Tire Dealer and Auto Service Professional. He previously worked for The Athletic, the Akron Beacon Journal and DK Pittsburgh Sports. He started at MTD and ASP in January of 2021. He is a graduate of the University of Pittsburgh. #H2P He enjoys the outdoors, sports, cooking (or, at least, eating food) and running (but that is a work in progress).