Inspection Process Is Best Way to Sell Brake Service, Says VIP’s Winkeler
In almost every facet of car maintenance, processes are the key. For almost every process, there is a step-by-step guide that allows for consistent and successful work. Brake system work is no different.
Needed brake service comes into the spotlight most often through vehicle inspections, says Tim Winkeler, CEO and president of Auburn, Maine-based VIP Tires & Service.
“The vast majority of our brake work comes by performing thorough inspections of vehicles when they come in for other, more frequent needs, such as an oil change, tire rotations or state inspections,” explains Winkeler.
“When our teams perform thorough inspections, our brake business increases.”
Another way to get vehicle owners’ attention is with specials. Winkeler says his stores run a promotion in the spring, usually April.
A normal promotion offers 50% off the price of brake pads.
The dealership maintains its usual price for brake rotors and labor in those cases.
Winkeler, who oversees more than 60 stores throughout New England, points to his company’s engagement process as a contributor, too.
“We internally call (it) ‘Going Five-for-Five,’ as there are five keys steps,” he says.
They include taking the customer through the job write-up, asking them to join a rewards program, performing a vehicle inspection, introducing customers to the technician who is working on their vehicle and asking customers to provide a Google review.
The technician performs “a multi-point inspection (MPI) as the first priority after the vehicle is pulled into the bay,” says Winkeler.
“When the technician performs a good MPI in a timely manner — using our tablets (and) doing a digital inspection — it gives the sales staff the information they need to then bring the customer out to the car in the shop and talk about what the technician has found”.
On the supply side, Winkeler says that VIP Tires & Service does not communicate with the manufacturers of brake parts, “but we do communicate regularly with the parts stores that we buy our brake parts from. In this case, that is O’Reilly Auto Parts. “We meet with O’Reilly leadership on a regular basis to discuss how our purchases of each category of parts are trending.
“We also get O’Reilly’s support for marketing, which we apply to discounted brake pads when we run that promotion.”
Best practices for brakes
MTD recently asked brake suppliers how they help and train tire dealers and technicians on braking systems and what’s new.
Gil Pulliam, senior manager, aftermarket sales, ADVICS North America Inc., says “the primary point we make to them is there is a reason why the manufacturer designed the brake system the way they did and with the quality level of parts they used.
“If ceramic brake pads were used to achieve the same braking performance, that should be considered in replacement. The weight of rotors, level of brake fluid — all of these tie to the delivery of the same braking performance the customer felt when they first drove that car off the dealer’s lot.
We also share the connection between cost and quality.”
Mike Eldard, aftermarket national sales manager, Akebono Brake Corp., has found that the most effective way to train technicians is through face-to-face interactions.
“We can personalize the discussion. When the service advisors and technicians are informed, it makes their job of talking to the customer that much easier.”
He emphasizes the importance of starting with quality parts.
“Cheaper brake pads cost you a lot more,” he notes.
“If a customer had quality, low-dusting ceramic brakes as original equipment and the technician replaces (them) with an inferior product, the customer will not be satisfied.
“Either they (will) come back and request a fix, which results in time and money out of the shop’s pocket” or they will “take their car somewhere to be worked on. In both cases, the shop loses.”
ADVICS and Akebono officials also discussed braking systems trends.
Brake components “have been really stable for the last 20 years, with the exception of one area: stability control modules,” says Pulliam.
“This unit is placed between the master cylinder and the wheels to ensure even distribution to all of the corners.
“So from the brake manufacturer’s side, if there is an issue with that unit, our solution is to replace it.
“But there are aftermarket options of programming or reflashing those units and the training for that typically comes from the device companies”.
Pulliam says that overall, braking system designs “have been very stable and until the electric/hybrid market becomes greater than 5% of vehicles in operation and leans on more regenerative braking, we don’t see any significant changes to how we stop cars.”
Bob Peters, chief brake engineer at Akebono, says three important, brake-related trends come to mind:
1. Legislation. Peters says California and the state of Washington both have enacted regulations that restrict the amount of copper used in brake pads.
As of Jan. 1, 2021, that level is limited to no more than 5% by weight.
In both states, this same regulation will limit the use of copper to less than half of 1% by weight, effective Jan. 1, 2025.
In many cases, vehicle manufacturers have decided to go directly to the 2025 “copper-free” step in 2021, according to Peters.
“We have engineered our ceramic brake pads to meet the regulations with very good results.
“There is very little — if any — difference in performance, dust or life with our copper-free formulations.
“Through competitive and trouble-shooting testing, we have found an increasing trend toward low-speed, low-frequency brake noise.”
2. The proliferation of electronic parking brakes. Most new vehicles are now equipped with electronic parking brakes, according to Peters.
“Most use an electric motor operating through a gear reduction system to apply the parking brake.”
Depending on the vehicle manufacturer, “the electronic parking brake may be applied following every drive cycle, leaving the brake pad squeezed to the rotor under very high load.
“In areas of the country where road salt is used during the winter months, this can lead to the brake pad corroding itself to the rotor.
“Not all friction formulations behave well under these conditions — specifically low-metallic or semi-metallic types — but we have even seen this create problems with some ceramic friction formulations.”
3. The presence of larger rotors. Many new vehicles are equipped with larger rotors and painted “opposed piston” calipers, where pistons apply pressure to the pads from both sides of the rotor.
“Because of the performance nature of these brakes or vehicles, we find they come with a dirty, dusty and often noisy friction formulation,” says Peters.
“Most of the dust visible on wheels and tires is actually due to rotor wear, between the corrosive nature of the friction material itself and the debris.”
About the Author
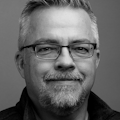
Ron Ledgard
Managing Editor
Ron Ledgard is the managing editor for Modern Tire Dealer and Auto Service Professional. He previously worked for The Athletic, the Akron Beacon Journal and DK Pittsburgh Sports. He started at MTD and ASP in January of 2021. He is a graduate of the University of Pittsburgh. #H2P He enjoys the outdoors, sports, cooking (or, at least, eating food) and running (but that is a work in progress).