Nobody wants to tell a customer that a flat tire with good tread depth is junk. In fact, most drivers will accept any repair as long as the tire holds air long enough for them to get back on the road. They will even promise to get it changed out as soon as they get home, but usually return weeks later with the same tire in the same position and a mysterious case of temporary amnesia.
In the old days, the consequences of a marginal tire repair were relatively minor. You would just write “No Guarantee” on the invoice if the injury was in the shoulder or sidewall. If the customer came back and demanded a refund because the tire failed, it was easy to explain that the repair was temporary, therefore, the driver was out of luck. Times have definitely changed.
First of all, there really is no such thing as “No Guarantee” anymore. Every commercial tire dealer is an expert in the eyes of the law, so using these words on an invoice or work order basically amounts to an admission of guilt. While it may prevent a refund in some instances, it certainly won’t play out well in a courtroom should an accident occur as a result of the failed tire.
Just imagine how the testimony will go when the dealer explains why they would not guarantee their work. Look at it like a plumbing company that makes a temporary repair on the natural gas line to someone’s house. One minute the employee falls for a hard luck story by doing a favor for a person who appears to be in need, the next minute the company is in court trying to explain why their employee blew up the house and took out half the block.
“So your employee knew the repair might not hold, but he went ahead and jeopardized the lives of the occupants and the neighbors so the homeowner could save a few bucks?”
Repair guidelines
The primary authority for radial truck tire repair is definitely the Rubber Manufacturers Association (RMA) wall chart. (A sample of the chart can be downloaded for free at website www.rma.org under the Publications tab.) Since RMA guidelines reflect a unanimous consensus among the tire companies, they are virtually indisputable from a legal perspective. As far as commercial tire dealers are concerned, the only type of repair that can be installed in the field is referred to as a puncture, or nail hole, repair.
Puncture repairs are limited to the crown area of the tire, which is the center of the tread approximately 1 to 1.5 inches in from each shoulder. Puncture repairs are also restricted by size and cannot be larger than 3/8 of an inch in diameter. And while truck tires have no finite limits with regards to the number of nail hole injuries that can be repaired, the RMA wall chart says, “The number of repairs may be limited by application, economics, and/or manufacturers’ recommendations.” Regardless of the number of repairs, the repair units cannot overlap (see photo 1) and if the repairs are directly across from each other so that the same radial body cable is injured more than once, the tire cannot be repaired in the field. The reason is that the cable in between the injuries becomes a “floater” that is not anchored by either bead. This creates instability that often leads to a belt separation when repaired with puncture repair materials.
Step by step
As far as procedures are concerned, RMA is very clear on the necessary steps for a puncture repair. While each step in the process is important, there are a few that are vital to restoring the original condition of the tire.
The first is removing the damage using a carbide cutter mounted on a low speed drill with a recommended tool speed of 1,200 rpm or less.
You’ll never find the words “hand-reamer” or “drill bit” in any credible tire repair resource. A carbide cutter is specially designed to cut the damaged steel belt and body cables flush with the surrounding rubber. This stabilizes the area so the void can be filled with a cured rubber insert, which is the second key step.
The RMA is specific on the requirements for filling the void. If the material is not vulcanizing material or a cured rubber stem, then it doesn’t meet industry recommendations. The final step is to seal the injury on the innerliner with a repair unit.
Notice I didn’t use the word “patch.” Repair units are divided into two categories: rubber-reinforced and fabric-reinforced.
While I personally lean toward a fabric-reinforced repair unit in a truck tire, I will acknowledge that the rubber-reinforced variety perform equally as well in the field.
Regardless, the repair material manufacturer has a specified repair unit for every size injury. If that guideline is not followed, then the tire repair will definitely be considered improper.
[PAGEBREAK]
Patch-only repairs
It’s also important to note that there are exactly zero advocates of the old “patch only” repairs. Even the smallest hole in the deepest tread block will allow water and moisture into the injury, which leads to corrosion in the belts. This is a virtual death sentence for every radial truck tire because a field technician has no idea how much corrosion is in place under the tread.
I’m willing to bet that more casings are lost to patch-only repairs than any other type of improper repair. Sure, they hold air and get the driver back on the road. But the end result is either a scrap casing or a blowout. Failing to remove the damaged cables creates the type of instability that leads to belt and sidewall separations.
No matter how you look at it, when patch-only repairs are installed in the tread or sidewall, technicians roll the dice with the lives of the drivers and everyone else on the road. Again, no credible resource in the tire industry recommends fixing the leak only with a patch and it’s pretty easy to spot on the mangled carcass after a failure.
Plug-only repairs
Another improper repair that anyone can identify is an on-the-wheel or “plug only” repair. They have the same number of supporters as the patch-only camp, but the consequences are much more severe. When the tire is not removed from the rim, the technician cannot inspect the inside of the tire. What appears to be a simple nail on the outside of the tread may cause extensive damage to the inside of the tire.
And when the technician gets lucky and manages to install the plug without creating another hole on the innerliner, the broken cables in the injury channel are still subjected to corrosion and instability because they are not trimmed back to solid rubber.
You will find universal agreement among the tire manufacturers, tire repair material manufacturers, tread rubber manufacturers and industry organizations like the RMA and the Tire Industry Association (TIA). Everyone agrees that the tire must be removed from the rim so the injury can be inspected on the inside of the tire.
Crowning touch
Finally, injuries in the crown area that are larger than 3/8 of an inch as well as those located in the shoulder and sidewall must receive a section repair that requires additional time, tools and equipment not typically found in the average commercial tire dealership. Section repairs are most commonly associated with retread plants where the technicians are trained to use special tools to remove the damage and fill the void with raw rubber so it can be cured in a press or chamber. A large reinforced repair unit is also installed on the innerliner of the tire and the tread design is regrooved after the raw rubber has cured. Like the patch-only repair, a section repair is easy to spot on the tire so any half-hearted attempt to fill the void will be obvious to an accident investigator.
A roll of the dice?
Understanding all of the rules and guidelines is critical in order for technicians to know what cannot be repaired. For example, if it’s a 3/8-inch bolt in the tire, then it may need to be considered for a section repair because it may be difficult to remove all of the damage with a 3/8-inch carbide cutter.
Likewise, if the injury extends from the shoulder to the crown on an angle or vice versa, then it becomes a possible candidate for a section repair.
When it comes to existing improper repairs, the best practice is probably to scrap the tire. Removing the improper repairs and replacing them with the proper stem and repair unit comes with a certain degree of risk, especially when patch-only repairs are in place. With no way to inspect the area around the injury to look for rust and corrosion, it’s definitely a roll of the dice when they are replaced in the field.
Commercial tire service technicians have to be trained to resist the urge to repair everything with a rubber stem and repair unit because they think it will hold long enough to get the driver home. They need to remember that drivers have short memories and yesterday’s favor to get a guy home can quickly turn into next month’s accident investigation. They also need to remember that lives are in their hands because an improperly installed repair is totally unpredictable after it returns to service.
As long as they understand and follow the RMA procedures on every tire, there’s very little to worry about if management supports them when they say a tire cannot be repaired. The problems start when someone approves a repair outside the limits and guidelines established by the industry.
So while it’s important to know what can be repaired, it’s equally imperative to understand what cannot be returned to service after installing some repair materials.
Kevin Rohlwing is senior vice president of training for TIA. He can be reached at [email protected].
About the Author
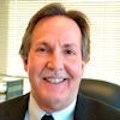
Bob Ulrich
Bob Ulrich was named Modern Tire Dealer editor in August 2000 and retired in January 2020. He joined the magazine in 1985 as assistant editor, and had been responsible for gathering statistical information for MTD's "Facts Issue" since 1993. He won numerous awards for editorial and feature writing, including five gold medals from the International Automotive Media Association. Bob earned a B.A. in English literature from Ohio Northern University and has a law degree from the University of Akron.