The science of wheel fastening: Now's the time to refresh your knowledge of this serious subject
Gaining a basic understanding of wheel fasteners is critical with regard to proper wheel installation. Sadly, this is a subject that is all too often taken for granted. After all, if the wheels are not secured to the vehicle correctly, the results can range from wheel or fastener damage, to catastrophic failure.
This article briefly discusses fastener styles, thread size and pitch and installation guidelines.
Note that not all wheel fasteners involve wheel nuts (or, using the common slang term, lug nuts). Some vehicle applications require the use of wheel bolts, where the hubs feature female threaded holes. So, when speaking in generalities, it's correct to refer to wheel fasteners, since this term covers all types.
Fastener sizes
Sizing any threaded fastener involves several dimensions, including diameter, thread pitch and length. Following are the basics.
Thread diameter refers to the diameter of the threaded section of the fastener (outer diameter of a bolt shank or stud). For example, if you measure the thread diameter of a 1/2-inch stud using a dial caliper, the diameter measured at the thread peaks will measure almost 1/2-inch (usually the exact measurement will be 0.005 - 0.008 inch or so less than exactly 1/2-inch). Wheel fasteners exist in both inch and metric formats. Common inch-format wheel fasteners include 7/16-inch, 1/2-inch and 9/16-inch. Common metric-format wheel fasteners include 10mm, 12mm and 14mm.
[PAGEBREAK]
Thread pitch refers to the number of threads or spacing between the threads.
In the inch format, the pitch refers to the number of threads found within a one-inch length of threaded area. For example, a 1/2-inch x 20 fastener is 1/2-inch in diameter, with 20 threads per inch of threaded area length. A pitch of 20 is commonly referred to as a "fine" thread, as compared to a 1/2-inch x 13 size, which would feature only 13 threads per inch -- commonly called a "coarse" thread. The terms coarse or fine are relative terms, depending on the thread diameter. For instance, a 1/4-inch diameter bolt with a 20 thread pitch is considered coarse, while a 28 thread pitch is considered fine. On a larger diameter bolt, such as a 1/2-inch bolt, 20 pitch is fine and 13 pitch is coarse.
In the metric format, thread pitch refers to the distance between threads. For example, a thread pitch of 1.25 indicates that the distance between two adjacent threads is 1.25mm. If the thread pitch is 1.50, the distance between threads is 1.5mm. In metric format, the higher the number, the more "coarse" the thread pitch. For example, a 1.0 pitch is "very fine," a 1.25 pitch is "medium fine," a 1.5 pitch is "medium" and a 1.75 pitch is "coarse."
While it may seem confusing at first, once you understand the measuring approach, it will be easy to identify thread sizes.
With regard to wheel fasteners, the threads are always "fine." As compared to coarse threads, this provides increased bolt strength and potential clamping load. If a wheel fastener is 7/16-inch in diameter, the thread pitch will be 20. If 1/2-inch diameter, thread pitch will be 20. If 9/16-inch diameter, thread pitch will be 18. Metric wheel fasteners will either feature a 1.25 or 1.5 thread pitch, regardless of thread diameter.
Thread engagement length is critical. At the minimum, thread engagement length must be equal to or greater than the diameter of the fastener. In other words, if the stud is 1/2-inch in diameter, the nut must engage onto the stud by at least 1/2-inch. If not, either a longer stud or longer nut must be used. If a longer nut is needed, the nut must protrude further through the wheel hole to meet the stud.
Use of longer nuts is possible when the nut features an extended shank that offers greater thread length. This will vary depending on nut style. If this isn't feasible, a longer stud must be used.
When using wheel bolts or capped nuts, care must be taken to avoid bottoming the bolt or nut. For example, if the stud offers one-inch of exposed length for nut engagement, but the threaded hole in the nut is only 3/4-inch deep, the nut will bottom-out on the stud and will not clamp the wheel against the hub. Pay attention to length, instead of blindly screwing on whatever nuts are handy at the time.
[PAGEBREAK]
Fastener drive style
Common wheel fastener drive styles will involve either a male or female hex or a spline drive that features a series of grooves or splines.
A spline drive style requires a special splined socket, while male hex head nuts or bolts require a six-point socket. Small-diameter spline-drive fasteners are commonly found on many "tuner" style wheels in order to accommodate small hub areas. By the same token, a female-hex type nut or bolt allows the use of smaller outside diameter fasteners where space is at a premium. These require the use of a hex bit (in slang terms, this is often called an "allen" wrench, a term that isn't always correct, since the term "allen" actually denotes a specific tool brand).
In short, if you plan to service today's custom wheels, it's important to realize that you'll need a broader array of tools beyond a basic selection of female six-point socket wrenches.
Another point worth mentioning relates to socket wall thickness. In many cases, the clearance between the fastener and the wheel's bolt hole entry cavity is very tight, requiring the use of thin-wall sockets to avoid scarring the wheel finish. This is something that many shops tend to ignore, until it's time to install or remove the wheel.
Our suggestion would be to stock a small inventory of thin-wall 1/2-inch-drive deepwell sockets (for servicing hex-headed wheel nuts or bolts), that are dedicated only to custom wheel service. Another benefit to this approach, as long as you don't use those sockets for routine repair jobs, is that the sockets will remain "healthy" (clean, with minimal wear and burrs that could damage chrome fasteners).
Wheel seat styles
The "seat" refers to the actual contact area between the fastener's head and the wheel.
It's critical to understand that the seat style of the fastener must match the seat style featured on the wheel. If the wrong seat style is used, the wheel simply will not be fastened to the hub correctly. If the seat style of the fastener does not match that of the wheel, you'll likely damage the wheel finish, and more importantly, the wheel will eventually loosen and wobble as it moves in relation to the hub. In short order, any play between the wheel and the fasteners will ruin the wheel's fasteners holes, resulting in either severe wheel damage or complete loss of the tire/wheel assembly.
The seat styles most commonly found include radius, conical, and flat ("mag"). These terms refer to the shape of the seat (where the fastener contacts the entry of the fastener hole in the wheel).
[PAGEBREAK]
Radius
Radius seats are also called "ball" seats, since the base of the nut (or base of the head on a wheel bolt) features a ball shape, which mates into a wheel's female radiused ball relief at the wheel's mounting hole.
Conical
Often referred to as "tapered" seats, the conical style features an angled seat wall (a "cone" shape). The fastener will feature a male cone seat, and the wheel will feature a female cone entry hole. The most common angle of taper is 60-degrees.
Mag
A "mag" wheel nut features a flat contact patch at the wheel (the nut usually features a thick flat washer). A mag style nut may also feature a smooth outer-walled shank that serves to help center the wheel on a lugcentric design, as the shank enters the wheel's bolt hole and serves as a guide pin to center the wheel's hole over the wheel stud.
When using a capped nut (where the female threaded hole does not pass all the way through the nut), it's important to pay attention to thread engagement length. At the very least, the nut must engage onto the stud at a depth that is equal to the stud diameter.
For example, if the stud diameter is 12mm, the nut must thread onto the stud by at least 12mm of depth. Also, make sure that the stud does not bottom-out inside the nut. If the stud bottoms out, it will be impossible to achieve full clamping load.
Fastener torque
NOTE: Prior to installing any wheel, verify the condition of the fastening system's threads (nuts and studs or bolts and hub threads). All threads should be clean and free of dirt, grease, grit, etc. If burrs or flat spots are found, replace the offending fastener.
Since the threaded wheel fasteners offer the only means of securing the tire/wheel assembly onto the vehicle, great care should be taken when installing. This means paying attention to both the degree of tightening and the tightening pattern.
All threaded fasteners are intended to stretch slightly when fully tightened to specification. This creates the correct preload required to secure the wheel.
If the wheel fasteners are under-tightened, they will eventually loosen, resulting in wheel damage or separation from the vehicle. If the fasteners are tightened too aggressively, the wheel stud or bolt can permanently stretch (fatiguing beyond its designed elastic range). Over-tightening can result in fastener failure, or at the very least will result in great difficulty during future removal. Especially when dealing with today's lightweight alloy wheels and sometimes light (and thin) rotor hats, severe wheel vibrations under braking can occur if wheels are improperly or unevenly tightened.
[PAGEBREAK]
The only way to assure correct clamping loads is through the use of a torque wrench. In a perfect world, all wheel fasteners should be tightened with the use of a calibrated torque wrench. In the real world, you at least need to draw the line with regard to custom wheels. Every custom wheel should be installed by tightening the fasteners with a torque wrench. There are no exceptions. Yes, using a torque wrench is more time consuming as opposed to using an impact gun, but when someone buys a set of custom wheels, they expect (and rightfully so) that the installation is performed correctly.
Always follow the vehicle maker or wheel maker torque specifications. Just remember that tighter is not necessarily better.
Never use an impact gun to tighten custom wheel fasteners. Not only will the level of tightness be suspect, but use of an impact tool can easily damage the fasteners or the adjacent wheel surface from a cosmetic standpoint.
INSTALLATION TIP: Since dissimilar metals (aluminum wheel mated to a steel hub) may result in electrolysis (corrosion causing the wheel to stick to the hub), before installing the wheel, apply a very thin coating of an anti-seize paste to the hub face where the wheel makes contact. Avoid applying excess compound, since any excess can sling out as a result of centrifugal force and can contaminate the wheel face or brake surfaces. A thin coating of this compound will make it easy to remove the wheels in the future.
By the numbers: Inch and metric formats differ
In the inch format, the higher the pitch number, the finer the threads.
In the metric format, the lower the number, the finer the threads.
[PAGEBREAK]
Make a correct fastener ID: Don't confuse thread size with wrench size
A common mistake is to falsely identify fasteners based on the wrench size required to service the nut or bolt.
For example, since a 3/4-inch socket wrench may be required to service a 1/2-inch nut, someone may refer to the nut as a "3/4" nut, even though the thread diameter is 1/2-inch. The hex size of the nut or bolt has nothing to do with the actual thread diameter!
Thread size is always based on the diameter of the threaded area. Always refer to any fastener's size according to the thread diameter, not the size of the tool required.
Using readily available measuring tools, it's easy to accurately identify the thread diameter, pitch and length of any wheel fastener.
These tools include a combination bolt/nut sizing card (usually made of plastic, with one card offering measuring for both inch and metric sizes) and two thread pitch gauges (one for inch and one for metric).
About the Author
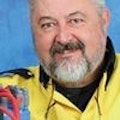
Mike Mavrigian
Longtime automotive industry journalist and Modern Tire Dealer contributor Mike Mavrigian also is the editor of MTD’s sister publication, Auto Service Professional. Mavrigian received a bachelors degree from Youngstown State University in English literature with a minor in journalism in 1975.