Traction controls the propelling, cornering and braking of a vehicle through the friction of the tire treads and the road surface, hence providing safety. The field of traction is complex, particularly when considering the road/tire/vehicle/driver system interactions involved.
The traction performance of a given vehicle depends on the following:
• tire friction properties (particularly tread hysteresis and hardness) from new to replacement time;
• vehicle properties from new to replacement time;
• road surface friction properties, from new to polished/worn by traffic, and from smooth to bumpy;
• vehicle speed, driver inputs and reactions;
• climatic conditions, hot/cold (summer vs. winter), winds, snow- or ice-covered road surfaces, rainfalls and road surface water drainage efficiency;
• tire tread design, footprint shape, dimensional proportions and amount of tread depth remaining; and
• tire type, load and inflation pressures.
Mathematical modeling and virtual testing of tires
In spite of the power of scientific means available to engineers today, tires remain extremely difficult, if not impossible, to model to the level of effectiveness required to yield tangible/reliable results representing real world situations.
To ease their tasks, and to attempt to reduce costs, engineers rely on assumptions, probability and statistical analysis, computer software algorithmic programs, etc., all in an attempt to correctly rate road/tire/vehicle/driver system operational characteristics. This includes the use of virtual testing, an approach which, at times, misses typical real world operating conditions. Mathematical modeling or forecasting, in fact, never gets to the point where it is 100% accurate.
As for human factors, they simply cannot be modeled with mathematics. So, when excessive faith and unrealistic optimism are placed on this approach, unpleasant surprises can arise, particularly once the product is in the public’s hands.
Although expensive and time consuming, real world road/tire/vehicle/driver system testing still yields the best results, but must be conducted by hands-on development engineers experienced in this field. This expertise, which takes years to acquire, is becoming harder and harder to find these days, and reliable interpretations of test results are paramount.
Tires as vital components of vehicle safety
Tires, of course, cannot be divorced from the rest of the vehicle system, for the way vehicles behave essentially depends upon the tire/vehicle system reactions to driver inputs.
For example, the way the vehicle rolls and loads are transferred when cornering, accelerating and braking. If the responses are too rapid or non-linear, ordinary drivers easily can be overwhelmed by conditions that are beyond their control, particularly when the tire-to-road-surface friction is significantly reduced, or when a tire belt/tread detachment occurs. This is true regardless of whether or not the vehicle is equipped with anti-lock brakes, traction/stability control and a tire pressure monitoring system (TPMS).
Tire/vehicle system development engineers should always put themselves in the consumer’s place to make sure that they can live with their driving mistakes — not only under the conditions when the tires internally are still in one piece, but also when the tires are near the point of experiencing severe structural degradation, such as belt/tread detachment.
As for vehicle stability control systems, they typically manipulate brakes and throttle/reduce vehicle speed in an attempt to help drivers maintain control. The Insurance Institute estimates that these systems diminish the risk of fatal single vehicle accidents.
Perhaps more stringent safety test criteria should be applied to vehicles. In the case of traction, the criteria should apply to the variable conditions of the road surface (friction), particularly when:
• such friction is significantly reduced;
• the tires have aged and have lost a large portion of their tread depth; and
• the tires experience belt/tread detachment.
I don’t know if today’s vehicles are validated under such comprehensive protocol, for of its own making, the industry today is confronted with an irrational myriad of tire types, sizes, aspect ratios, wheel diameters, tire tread designs and compounds, and an equally irrational quantity and variety of vehicle models and architectures. The overall result is high tire/vehicle system development and manufacturing cost, which is automatically passed on to the consumers.
Synthetic vs. natural tread rubber compound
The difference between synthetic and natural tread rubber relates to the resiliency/hysteresis values of the respective tread compounds. A 100% synthetic tread rubber compound has a low resiliency/high hysteresis value.
A 100% natural tread rubber compound has a high resiliency/low hysteresis value.
The use of synthetic rubber tread compounds contributes to definite improvements in tire grip/traction/skid resistance. Racing tire treads use very high friction, 100% synthetic rubber and soft compounds, a key factor in winning races. Other types of vehicles, such as medium/heavy-duty trucks, earthmovers and airplanes, use tires featuring high grade natural rubber compounds for their structures and treads. Winter tires also use soft tread compounds, which do not harden much at low temperatures (32 degrees Fahrenheit and under).
Grip is more of a static condition. For example, when a vehicle is parked on a steep incline with the parking brake on, it will still be there days or weeks later. This is grip, whereby the maximum level of tire to road surface reaction force is reached without the stationary vehicle sliding down the incline.
Friction is more of a dynamic condition, whereby maximum tire to road surface reaction forces are reached when the vehicle is in motion. Grip and friction are components of the overall tire to road surface traction/skid resistance system, which is equal to their sum.
A sufficient amount of tire to road friction must always be available to maintain driving control, including when the roads are affected by ice, snow and rain.
Tire to road surface friction affects tire/vehicle system traction properties. Friction, however, means hysteresis (energy loss) and fuel consumption.
As I indicated in the August 2008 issue of Modern Tire Dealer on tire rolling resistance, the tire tread, when new, represents a significant portion of the total tire hysteresis loss value.
However, this value diminishes when tires have aged with time and mileage, and when their tread grooves and sipe depths are a fraction of their original sizes, which, in turn, reduces tire to road surface friction properties.
In the meantime, some tire producers are promoting tires with multiple tread compounds. This means that the tire to road surface friction values change from one tread zone to the other, further complicating an already complicated situation.
Effect of tire stiffness on traction
For practical purposes, all tire traction/road adhesion testing is conducted on dry and slippery, flat/smooth road surfaces. To obtain maximum traction/skid resistance/adhesion, a tire must have a low spring rate (low stiffness) throughout its deflection stroke: in other words, a spring rate versus deflection curve as flat as possible. The stiffer the tire, the easier it is for the tire/wheel assembly to leave the ground when road surface irregularities are encountered. At this point, traction is impaired. This is why racetracks are designed to provide maximum friction and maximum smoothness and flatness — and why tires are designed with minimum radial and lateral force variations for a given tire/vehicle suspension system.
In 1961, I developed a tire uniformity grading machine at Ford Motor Co., which determined not only radial and lateral force variations, but also the dynamic radial stiffness and damping factor of tires (J.J. Bajer, SAE paper no. 667B presented in Detroit in March 1963 on tire uniformity, and J.J. Bajer, SAE paper no. 690526 presented in Detroit in May 1969 on road/tire/vehicle system wet skid resistance testing).
Traction testing
There are advantages of road/tire/vehicle/driver system testing over indoor tire testing machines:
1. It is more versatile.
2. All vehicle sub-systems affecting tire performance are on-board (power train, brakes, steering, suspension, etc.).
3. Vehicle instrumentation and data acquisition are easily accommodated.
4. It represents real world consumer experiences.
While indoor tire testing machines can determine some aspects of tire traction, such as aquaplaning resistance, outdoor vehicle testing is still the best method to grade tire performance, as indicated earlier.
The tire contact patch
When an inflated and loaded tire is deflected against the ground, it creates a footprint, called a tire contact patch. A contact patch much longer than it is wide, typical of high aspect ratio tires, increases the tire residence time on the road surface, and provides more resistance to aquaplaning for a given tread design. Such contact patch has a length (L) to width (W) ratio ranging from 1.75 (to 2) to 1 at normal tire loads and inflation pressures, with the tires deflecting a minimum of 20% of their inflated section height at stabilized pressures and temperatures.
Ultra-low aspect ratio tires have contact patches not nearly as long as high aspect ratio tires, and therefore, are less resistant to aquaplaning, but provide higher tire lateral stiffness and guiding force on dry, high friction road surfaces. A reduction in tire inflation pressure increases the length of the contact patch, and an increase shortens it.
Since the section height of such a tire is low, a 20% deflection means much less tire deflection as compared to a high section height tire; hence, vehicle ride and NVH (noise, vibration, harshness) quality and traction on slippery surfaces deteriorate, particularly at low tire tread depths. Therefore, in addition to the contact patch length to width ratio, the tire tread volume to void ratio must be taken into consideration, as well as the tire tread hardness and resiliency under both warm and cold weather vehicle operating conditions.
Figures 1A and 1B show the contact patches of high and low section height tires.
Tires operating on deformable surfaces
When tires operate on snow, mud, dirt or sand, the tire treads gear themselves to these deformable surfaces. In this case, a tire having a contact patch length to width ratio of 1.75 to 1 minimum is highly desirable, as is low (within limits) tire inflation pressure. When the vehicle rolls and the wheels are cambered, the tire pressure distribution is considerably altered, and the contact patch shape becomes trapezoidal.
Tire contact patch pressure
The intensities and distribution of tire contact patch pressure affect tire traction and the effectiveness with which water can be dispersed from the contact patch when the road surface is wet. Contact patch pressures also affect the regularity and rate with which tire treads wear and, to some extent, tire structural integrity, particularly at the tire belt edge zone (the radial tire’s Achilles’ heel).
Tread wear resistance, rolling resistance and skid resistance, when well balanced, are vital signs of well-developed and produced tires.
Contact patch research
Over the years, tire contact patch shapes have been well-researched and documented, using, among other techniques, photographs taken through a glass plate under tire static and dynamic operating conditions, and through contact patch pressure measurements.
In 1962, a technique was developed by Walter Horn and his colleagues at NASA to study the contact patch behavior of large aircraft tires under dynamic operating conditions, particularly in regard to aquaplaning. Later on, the technique was improved by the Dunlop Rubber Co. Ltd. of Birmingham, England. These early efforts contributed to a better understanding of the tire contact patch. The details were obtained under wet surface operating conditions via color photography using dyes in the water to study the turbulence and evacuation characteristics of the water flow for a given tire and tread architecture.
In my office, I have a 1964 full-size color print of an aquaplaning-resistant Dunlop radial passenger car tire going through water at a fairly high vehicle speed. The print shows the initiation of aquaplaning at the leading edge of the tire contact patch.
This shot was taken as part of a comprehensive tire/vehicle system development collaboration between Ford and Dunlop during the early days of the Ford radialization program, in which I was deeply involved. Over the years, visitors to my office have been amazed by the combined artistic and scientific nature of this photograph (see photo with this article).
Tire inflation pressures and their effect on traction
In contrast to the radial-ply tires originally introduced on the U.S. market in the 1960s, and as compared with the bias-ply tires used in pre-U.S. radialization, today’s radial-ply tires operate at much higher inflation pressures, 35 psi instead of 24 psi.
Tire loads, however, for practical purposes have remained the same. Also, today’s radial-ply tire deflections and aspect ratios have been significantly reduced. As indicated earlier, an increase in tire inflation pressure shortens the length of the contact patch, and a reduction increases it. Again, to derive a good balance of tire to road surface traction, the contact patch should be much longer than it is wide.
Racing tires
Racing tires, such as used on Formula 1 race cars, operate at relatively low inflation pressures and light loads, and are quite large in relation to the loads they carry. These tires are designed/developed to maximize tire lateral force, longitudinal power transmission (propulsing and retarding), and overall traction on dry, high grip, flat and smooth track surfaces, and they don’t have sipes. Such tires are ineffective when operating on insufficiently drained wet track surfaces, and when that happens, the race must then be stopped.
Aircraft tires
To resist aquaplaning, tires used on large civilian and military aircrafts have high aspect ratios; perform at high pressures (300 psi+) and relatively high deflections; feature long, narrow tread contact patches; and use appropriate tread grooving volume. Aircraft tire treads are also sipe-less.
Lateral force is not as much of a factor with aircraft tires as with racing or passenger car tires, for the aircraft handling and trim during take-off and landing (the two critical aircraft operating modes) is essentially controlled by the aircraft airfoil shapes set by the pilot, with traction playing an important role. Aircraft tires are used as duals.
Medium/heavy-duty truck tires
The traction performance of medium/heavy-duty truck tires is a critical aspect of the overall tractor/trailer performance. Usually 18 tires are involved, eight on the trailer and 10 on the tractor. The tires, all of .75 aspect ratio, are also used as duals, except on the steer axle.
Dual tires provide very good traction and stability and a very interesting safety feature, for when one of the two tires loses pressure, the other tire can sustain the load (the ideal run-flat tire system), which eliminates the use of a spare. This idea was applied to passenger cars years ago on an experimental basis, but was never commercially introduced.
For years, the industry had tried to eliminate the use of duals on trucks, yet today duals prevail (they were originally introduced by Manufacture Française Des Pneumatiques Michelin of Clermont-Ferrand, France, in 1908).
The giant Caterpillar 797 mining truck uses duals on its rear axle. The truck has a 360-ton payload capacity and is equipped with high aspect ratio 55/80R63 tires originally developed by Michelin. The tires are called “ultra-class,” and are rated on a ton/mile per hour basis (TMPH), a rating originally developed by Caterpillar in the early 1960s to supplement the Tire & Rim Association ratings. TMPH specifies the levels at which the tires can safely and economically work, balancing heat generation with heat dissipation at a fully loaded maximum permissible truck speed, with the tires operating at maximum possible temperature (tire work capacity).
The power input to the tires and their tractive and load capacities versus temperature relationship at maximum truck load and speed is, indeed, critical. TMPH, therefore, offers the user of earth-moving equipment the means of accurately estimating job costs, and a standard by which they can determine the type of equipment necessary for the job.
This interesting subject is mentioned in passing, for ultra-class tires must also provide very high traction performance (the 797 truck engine delivers 3,400 hp, high torque and long life), as the truck must operate 24 hours a day on unpaved surfaces that must be kept at good levels of maintenance for the truck to carry its full load safely at 45 mph to 50 mph under typical mining operations worldwide.
Testing for traction and degradation
It is important how traction is tested and rated, and what the facilities, testing procedures and road/tire vehicle system engineering expertise used to conduct such traction testing are, as well as how the test results are analyzed and correlated with the real world consumer experience.
Unfortunately, passenger car producers seldom take tire traction and tire structural integrity degradation into consideration when testing their vehicles. The effect of tire punctures is also often ignored, in spite of the fact that tire structural failures, particularly those occurring at or near the tire belt edge zones, are, at times, related to punctures.
Also to be recognized are losses of inflation pressure due to poor puncture repair, porous cast aluminum wheels, poor tire innerliner pressure retention, poor tire bead-to-rim fits, leaky tire valves, poor tire valve-to-rim fit, and poor tire valve design and manufacture.
As a result, tires operate underinflated for long periods of time, thereby developing structural fatigue and poor tire traction.
Summary
Tires play a vital role in vehicle operational characteristics and safety, which includes traction. Vehicle producers should remember this when validating their vehicles for public use. As for replacement tires, consumer product publications rate them, and make recommendations according to their own tire performance acceptance criteria. But how comprehensive and representative is such testing, and what happens once tires have been validated for application on these vehicles and begin to be produced by the millions?
At this point, consumers only can put their faith in the tire and vehicle producers, trusting that they have done the right thing to protect their safety. However, tire manufacturing variations do occur and, when severe and undetected, can have dramatic safety consequences, regardless of the original tire approval procedures used.
Consequently, the effect of these variations must be taken into consideration when validating tires for public usage, and this includes tire traction validation. ■
About the Author
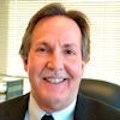
Bob Ulrich
Bob Ulrich was named Modern Tire Dealer editor in August 2000 and retired in January 2020. He joined the magazine in 1985 as assistant editor, and had been responsible for gathering statistical information for MTD's "Facts Issue" since 1993. He won numerous awards for editorial and feature writing, including five gold medals from the International Automotive Media Association. Bob earned a B.A. in English literature from Ohio Northern University and has a law degree from the University of Akron.