Earlier this year, I completed my 30th year in the tire industry. When I first started working for my dad, customers had limited choices when purchasing replacement tires, and “performance balancing” was much simpler.
They could choose between bias or radial construction and thin whitewalls or wide whitewalls on certain sizes. Alpha-numeric sizing was in the final process of being phased out of the market, so we had to remember the P-metric conversion when installing new tires on older cars. If a car came in with ER78-14 tires, then we would install a set of P195/75R14s. The P-metrics were a little smaller in diameter with a wider section width (a trend that really hasn’t stopped), but most drivers never noticed the difference so they weren’t considered performance tires.
At that time, the concept of aluminum alloy wheels was reserved for few car enthusiasts because chrome was still king and the majority of OE vehicles at the time were equipped with steel wheels and wheel covers. Sports cars were really the only ones equipped with actual performance tires from the factory, so when we talked about a performance package back in the day, we were probably looking at someone in the market for custom tires and wheels. I can still remember when a friend of mine bought a set of 50’s on chrome dish wheels from us for his 1971 Chevelle. With the raised white letters and the wide treads, that vehicle was all about performance in his mind. Of course, nothing else on the car had changed. The engine, transmission and suspension were all stock, but the tires and wheels made it a completely different car to drive.
Fast-forward three decades after my first years in the business and it seems like a century has elapsed. After the new vehicle manufacturers started recognizing the superior handling and cool factor that performance tires and wheels added to a vehicle, the race was on. While 50- and 60-series aspect ratios and 16- and 17-inch rim diameters were once reserved for a small segment of sports cars on the OE scene, they became common on compacts and sedans. And while it was once something special to see a 20-inch tire and wheel package on a sport utility vehicle, the whole Donk culture changed everything with 24-inch rims on full size sedans. In 2001, the P235/75R15 was the most popular replacement tire and original equipment tire. Less than a decade later, the P225/60R16 is the most popular replacement tire and the P215/60R16 is the most popular OE tire. What’s even more amazing is that the P275/55R20 has become a top 10 OE size. And the P235/75R15? It’s fourth on the replacement list and falling fast and completely out of the OE top five altogether.
The growth in high-performance (HP) and ultra-high-performance (UHP) is even more pronounced. In 2001, the total HP and UHP tire market was 25 million units, or 13% of total production. A decade later, the HP share alone was 32 million and the UHP was 29.7 million, which represents approximately 27% of domestic tire production. If this trend continues and it ends up doubling again in 10 years, more than half of the domestic tire market will be HP and UHP.
I have a lot of theories on what’s driving the industry toward performance tires, but the one that I believe has the most merit is based on new government regulations. When Federal Motor Vehicle Safety Standard (FMVSS) 139 came into effect a few years ago, the tire companies were forced to build a more durable and robust product. And with the creation of FMVSS 126 that includes the new electronic stability control (ESC) requirement, all vehicles under 10,000 pounds GVWR must, “use automatic computer-controlled braking of individual wheels to assist the driver in maintaining control in critical driving situations” starting with the 2012 model year. These two requirements together are changing the way that vehicles, and tires, are being engineered.
[PAGEBREAK]
In order to fulfill the government requirements and improve the level of handling, the new car companies will continue to use more HP and UHP tires. The smooth ride that used to come from the cushiony 75- and 80- series tires is now dependent on much shorter and stiffer sidewalls. Since it has been made possible by replacing the coil springs and shocks with independent suspension and sophisticated electronics, even the slightest amount of imbalance may be felt by the driver in the steering wheel or seat. Adding to the problem is a tire pressure monitoring system (TPMS) sensor that can weigh between 1 to 1.5 ounces. In an age where a balanced assembly is more critical than ever for customer satisfaction, it’s amazing that so little attention is paid to doing it correctly.
Customers who spend the money to purchase a set of HP or UHP replacement tires deserve to expect more than the average tire buyer. They have resisted the temptation to step down to an S- or T-rated alternative and save a few dollars because safety, performance and handling are key factors in their decision. Tire retailers across the nation depend on these educated consumers because they understand the importance of following maintenance recommendations. You won’t find them standing at the counter and arguing about what work should be performed. They trust their service provider to do what is best for their vehicle, which is the primary reason why the independent tire dealer continues to thrive in a big-box world.
So why do so many technicians continue to take the easy way out and slap a quick static balance on a performance tire and wheel assembly? You might as well dust off the old bubble balancer because a static balance on a computer balancer is basically the same thing. Static imbalance refers to the amount of “hop” in a rotating assembly, and placing a single weight on the inboard rim flange opposite the “heavy” spot will account for the difference. With the virtual elimination of the outboard rim flange on most alloy wheels, this is by far the easiest way to balance a performance tire on a typical OE wheel. It’s fast, easy, and requires very little training or effort, which probably explains why it is so popular. But is it really the best thing for the tire or the driver in a performance vehicle world?
A performance balance
Performance balance begins with the mounting process. All of the bead seating surfaces of the rim must be cleaned and lubricated with a non-petroleum rubber lubricant. After lubricating the beads and mounting the tires, any red or yellow sidewall stamps should be aligned with the valve stem sensor. Then the tires should be fully inflated to the maximum inflation pressure molded on the sidewall and deflated to allow the beads to relax. Studies have shown that this practice improves concentric bead seating and reduces the amount of run-out. While the maximum allowable amount of variation between the rim flange edge and the molded rib on the lower sidewall is 2/32 of an inch, technicians should re-seat every tire that shows any variation in that distance. Finally, the tires must be inflated to the pressure indicated on the vehicle placard before making any attempt to balance.
The next step is to secure the assembly to the balancer and center it on the rotating shaft. If technicians want to take the high-tech bubble balance approach, the standard back cone with a front cup is simple and quick. But it is also less precise and more prone to misalignment than pin plate installation. And while pin plate sets are not cheap, the pay-off in the long run is a much happier customer base with fewer vibration complaints. Measuring devices make it a lot easier to determine the pin positions, and by combining the proper positions with the correct size back cone, technicians can consistently center every assembly on the machine. Some balancers also include the functionality to determine if the tire and wheel are centered on the shaft. Technicians can follow a few simple steps to verify that the assembly is centered on these machines. If that function is not available, activate the balancer and then take note of the locations for the weights. Loosen the hub nut and then re-spin the tire. If the amounts and locations of the weights have changed significantly, the assembly may not have been centered.
In order to bring most assemblies into complete balance, weight must be added to both rim flanges. Besides the “hop” associated with static imbalance, there is also some degree of “wobble” to the rotating assembly. Dynamic balance uses weights on the inside and outside of the rim to offset both forces, making it far superior to static balance.
[PAGEBREAK]
Tape weights
Because the trend toward alloy wheels without an outer rim flange is no longer a trend — it is now a common trait on OE fitments with performance tires — the installation of tape weights is necessary and unavoidable. Modern balancers are already set up to make it much easier than the guessing game of decades ago. Technicians just select the wheel weight positions that they want to use and then follow the regular procedures for selecting the size and position of both weights.
One of the biggest challenges of using tape weights has been getting them to stick to the rim surface. A little brake cleaner spray on a shop towel does a good job of removing most contaminants without leaving a residue or damaging the surface. Applying brake cleaner directly to the surface can damage the finish on the outside of rim as a result of the overspray. It may take some time to clean the area for the tape weight, but a performance balance is all about the details, so accuracy is the most important factor, and that requires a tape weight on most wheels. And while the inside rim flange on most wheels will still accommodate a standard clip-on weight, technicians must still select the correct weight for the flange contour and make sure that a coated weight is used so the finish is not damaged.
Modern balancer technology
For tire service providers who want to distinguish themselves from the competition by offering extreme performance, modern balancer technology can measure and correct a lot more than static and dynamic balance. These machines can measure the run-out and balance of the tire and wheel so they can be match mounted on the wheel and on the vehicle. And for those who want to factor in any road force when measuring and correcting imbalance, there is a balancer that includes a hydraulic wheel that simulates a loaded assembly. In the hands of a well-trained technician, advanced features on today’s computer balancers can drastically reduce the amount of weight that is necessary by matching the heavy and/or high spots of the tire with the light and/or low spots of the rim while taking run-out into account.
Balancing has come a long way since the bubble balancer. Tires have come even farther. And the vehicles that we service today are far more sophisticated and have more computer power than the lunar landing modules that pre-dated my first years in the business. Since the government is mandating a safer vehicle with safer tires, there will probably be an increased emphasis on performance, especially when it comes to handling.
I purchased a new compact car in 2010 and recently replaced the V-rated 17-inch performance tires without balancing them at all because I “didn’t have time.” But I did the performance bead seating of fully inflating and then deflating before properly inflating them because I figured it would help. On a road trip to Chicago, I noticed some vibrations at highway speeds. So I decided to performance balance my tires and take a few pictures for this story. It took a little work, but I was able to get rid of the vibration and now the ride is smooth at every speed. If I had done it right the first time, I could have saved myself the extra time and effort. The total cost was about two hours and after complaining to management about the inconvenience, I’ve decided to deduct two hours of NFL draft coverage from my personal time and do something productive around the house instead.
I hope your customers are as understanding when shortcuts and general laziness result in preventable ride complaints.
Kevin Rohlwing is senior vice president of training for the Tire Industry Association (TIA). He can be reached via e-mail at [email protected].
[PAGEBREAK]
Beware the hidden trap: How to prevent residual static imbalance
Even with a two-plane dynamic balance, there is a hidden trap that most technicians aren’t aware of, which is residual static imbalance, i.e., static imbalance that is left over even after a successful dynamic balance that yields “0.00” on the balancer. According to Kevin Keefe, vice president of marketing for Hennessy Industries Inc., here’s how it happens.
“Most everyone’s balancer will not indicate that 1/4 ounce of dynamic corrective weight is required in either plane unless the imbalance measurement is actually 0.25 ounce through 0.38 ounce. That means up to 0.24 ounce of residual dynamic imbalance can be left in either or both planes while still achieving a successful ‘0.00’ dynamic balance.
“So, let’s take the worst scenario, where there is 0.24 ounce of residual dynamic imbalance in both planes (remember, balancer says all zeros, tech is happy, believes he’s doing outstanding work). If he’s lucky, the locations of those residual imbalances are exactly 180 degrees away from each other, and the resultant residual static imbalance is zero. The odds of this happening are one in 360.
“Now, let’s consider the opposite scenario, where the locations of those residual static imbalances are exactly the same radially. The resultant residual static imbalance is 0.48 ounce. That’s a half ounce of imbalance the operator can’t see (remember, balancer says all’s well!) that will surely bring most passenger car vehicles back with a vibration complaint. Again, one in 360 odds, but there are still a lot of unacceptable scenarios between 0 and 0.5 ounce of residual static imbalance.”
Keefe offers two remedies for residual static imbalance.
1. The long way: “After every spin, put the balancer in fine mode, look at the magnitude and locations of the dynamic residuals, and if necessary put the balancer into static mode and re-spin, placing an additional corrective adhesive weight in the center plane of the wheel to correct for the excess static imbalance without negatively impacting the dynamic balance.”
2. The shorter way: “Using our equipment as an example, the Coats 1250 Series or ProRide wheel balancers have a unique balancing algorithm that calculates the corrective dynamic weight amounts and placements in order to automatically minimize residual static. In most cases, it’s below 0.20 ounce, well below what even the pickiest of customers could feel. And, as a quality check and to keep it top-of-mind, we actually display both dynamic and residual static data. Balance it dynamically on any of these balancers, and it’s absolutely going to be balanced statically as well.”
About the Author
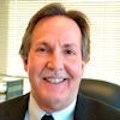
Bob Ulrich
Bob Ulrich was named Modern Tire Dealer editor in August 2000 and retired in January 2020. He joined the magazine in 1985 as assistant editor, and had been responsible for gathering statistical information for MTD's "Facts Issue" since 1993. He won numerous awards for editorial and feature writing, including five gold medals from the International Automotive Media Association. Bob earned a B.A. in English literature from Ohio Northern University and has a law degree from the University of Akron.