Tire rolling resistance, also called tire “drag” or tire “power wastage,” is a relatively small force. It is expressed in pounds per 1,000 pounds of tire load (eight to 15 pounds per tire at moderate speeds of 25 to 45 mph), and is extremely difficult to measure under real world vehicle operating conditions. Consequently, it is measured with indoor tire testing machines.
Even though the values of tire rolling resistance issued from such machines are not those that would be obtained under real-world operating conditions, and even though these machines are expensive and require frequent maintenance and calibrations, they nevertheless significantly simplify the tire rolling resistance measurements. An SAE standard, SAE J2452, has been developed to grade tires for rolling resistance based on the use of such machines.
Tires consume power primarily through hysteresis losses from the rubber compounds they are made of, and, to some extent, from certain types of cords making up the tire cross-sectional structure. These materials are not 100% resilient. Therefore, as tires, in the process of providing vehicle functions, go through their continuous deformation and recovery cycles, they waste power in the form of heat.
Tires also consume power due to friction between the tire tread and the road surface. Therefore, the type of road surface over which tires operate affects their rolling resistance values. A very smooth, traffic-polished road surface provides the lowest rolling resistance. A very coarse-textured surface, such as a new concrete highway surface, provides the highest rolling resistance, the lowest fuel economy and the fastest tread wear.
[PAGEBREAK]
Of utmost importance: One must have a sense of proportion when comparing the magnitude of tire power losses with power losses from other portions of the vehicle system, such as:
* the engine,
* the transmission,
* the drive line,
* the transfer case,
* the axle gears and bearings,
* the wheel bearings,
* the resistance the vehicle encounters propelling itself through the air, and
* head and side winds.
The loss of power needed to overcome vehicle mass, the high inertia of heavy, large tire/wheel assemblies, overloaded/underinflated tires and, last but not least, the effects of poor vehicle maintenance, including wheel alignment and tire inflation pressure in general, also must be taken into consideration.
Tires also consume power through windage, particularly at high speeds. Here is an extreme comparative example: A narrow, light, energy-efficient, beadless, full-torous bicycle tire, such as used in the Tour-de-France race, has extremely low windage losses as compared to an ultra-wide, ultra-high performance passenger car tire.
In view of the recent, unprecedented increases in the price of fuel, it must be realized that a reduction in tire rolling resistance has a much greater effect on the amount of fuel consumed by a low-drag, efficiently powered, relatively light (3,000 pounds or less) two-wheel drive passenger car equipped with broad-line 185/65R15 tires than it will have on a large, heavy (4,300 pounds or more) four-wheel- drive high-drag vehicle equipped with ultra-wide, ultra-low section height tires mounted on 17-inch diameter wheels or larger. Tire/wheel assemblies with high-rotating mass and high inertia take more power to accelerate and decelerate and maintain vehicle speed at road loads.
[PAGEBREAK]
The effect of lowering tire rolling resistance alone on fuel consumption is much less pronounced than it appears at first glance from the tire rolling resistance values typically derived from indoor tire testing machines.
Fuel economy and vehicle efficiency do not necessarily mean small vehicles. Efficient use of materials (old and new), vehicle mass reduction, improved powertrain, chassis and body efficiencies, as well as tires, must all be viewed as parts of a total system, for they are the keys to a significant reduction in vehicle fuel consumption. Today, this could be achieved without complication, to the dismay of those having a keen interest in keeping things, including tires, the way they are.
According to Modern Tire Dealer’s 2008 Facts Issue, tires come in more than 1,700 size varieties. Some section heights are low to the point of being simply ridiculous, with the wheel rim flange as little as two inches from the ground. At times, such an ultra-low section height tire can detrimentally affect wheel structural integrity.
Let us not forget that tires and wheels are supposed to absorb road surface irregularities and shocks without structural degradations. This requires sufficient tire section height.
Based on my tire/vehicle system engineering/development experience, tire properties other than tire rolling resistance should be given equal or more importance, particularly those related to vehicle operational safety and economics, such as tire and wheel structural integrity retention, tire traction (skid resistance) and, of most importance, long tire life. And, if in the process, lower rolling resistance tires can simultaneously be derived, the better.
Factors affecting tire rolling resistance
Tire rolling resistance is at its highest when the tires are new. After they have been running for 100 to 200 miles at moderate speeds, accelerations, decelerations and cornering, the rolling resistance stabilizes and remains relatively constant at a given speed, load and temperature.
There are many factors that affect tire rolling resistance.
1. Tread wear. Near the end of the tire tread life (3/32nds-inch of tread groove depth remaining), the tire rolling resistance has gradually diminished, except for the effect of tread-to-road surface friction. At that point, a large portion of the tire rolling resistance is attributable to tire flexing and deformations.
2. Tire tread thickness. For a given tread compound formulation, tread design and width, the thicker the tread, the higher the tread hysteresis loss, and the higher the tire rolling resistance. For traction performance reasons, tire tread compounds must be made of a relatively high hysteresis polymer, which contributes about 55% to the tire’s rolling resistance when the tire is new. Again, as the tread wears out and its thickness diminishes, the tire rolling resistance, from the tread standpoint, is gradually reduced. However, at that stage, and depending upon the climatic conditions encountered, the tire may operate at a lower equilibrium temperature, which, in turn, increases the tire rolling resistance.
3. Tire size. Tire rolling resistance values, for practical purposes, are independent of tire size for a given line of passenger car tires of normal dimensional proportions (aspect ratio), such as .65 to .75.
[PAGEBREAK]
4. Tire operating temperatures. Tire operating temperatures have a significant effect on tire rolling resistance. Other conditions remaining relatively constant, an increase in tire operating temperature reduces the tire hysteresis losses from the tread to the balance of the tire components, which, in turn, reduces the tire rolling resistance. The reverse occurs when the tire operates at lower temperatures, such as during the winter months.
5. Vehicle speed. At vehicle speeds ranging from 25 to 45 mph, the tire rolling resistance does not rapidly increase with speed, but at speeds from 55 to 90 mph it does, although at these higher speeds, the tire operating temperatures increase, which, in turn, increase tire inflation pressures, hence reducing the tire rolling resistance.
6. Tire compounding. The effect of tire compounding on rolling resistance is quite pronounced. The higher the hysteresis loss of a given tire compounding system (the total number and variety of all compounds required per tire), the higher the rolling resistance. However, such a compounding system increases the tire operating temperature. This, in turn, reduces the tire rolling resistance at the point when the tire has reached its equilibrium operating temperature and pressure.
7. Wheel rim width. Mounting tires on wider rims than ideal reduces tire deflection for a given tire inflation pressure, and, therefore, decreases tire rolling resistance.
8. Tire load variations at a constant tire inflation pressure. An increase of tire load at a constant inflation pressure increases tire deflection, and, consequently, increases both tire rolling resistance and tire operating stress (shear, bending, tension, compression). Again, tire operating deflections and temperatures come into the picture, and are not to be ignored.
9. Tire inflation pressure variations at a constant tire load. An increase of tire inflation pressure at a constant tire load decreases tire deflection, which decreases tire rolling resistance. It also decreases the tire operating temperature, but increases the tire operating stresses.
10. Constancy of tire rolling resistance. By now, one easily can conclude that the rolling resistance of a tire is not constant. If it were, the rolling resistance would be inversely proportional to tire load. The relationship between rolling resistance and tire load is affected by the non-constancy of the rolling resistance, particularly under real world vehicle operating conditions.
11. Cornering. When cornering, a tire operates at a slip angle; consequently, its rolling resistance is increased as a component of the tire cornering force. Severe tire conicity values, which result in vehicle pull, have the same effect, as the driver, to keep the vehicle going down the road straight, must exert a steering correction. The result is a slip angle and cornering force, which increases the tire rolling resistance. Misaligned wheels, particularly excessive toe-in or toe-out, have the same effect.
[PAGEBREAK]
Incidentally, “conicity” is a term that has been used since the advent of radialization, and does not apply to bias-ply tires, which are still used in significant parts of the world.
12. Vehicle acceleration/deceleration. When severe and frequent, the effects of vehicle acceleration and deceleration are detrimental to tire rolling resistance. Smooth, fluid driving not only conserves fuel, but also increases tire tread life as well as overall tire life from the structural integrity standpoint.
13. Internal tire architecture. The type of internal tire architecture used on a given vehicle has by far the most pronounced effect on tire rolling resistance, operating temperature, tire tread life and other vital aspects of tire performance.
The original Michelin radial passenger car tire consisted of three high-density steel cord-triangulated belt plies that were well-decoupled from the tire rim bead seats via two thin 90 degree rayon cord plies. The tire made a major contribution to decreasing tire rolling resistance and operating temperature while increasing (nearly tripling) tire tread life, as compared to equivalent size four-ply bias tires.
The decrease in tire rolling resistance reduced vehicle fuel consumption by 4% to 5% when these tires were fitted to typical small, light European cars.
Such overall tire performance was, indeed, welcome in Europe right after World War II, when raw materials and gasoline were expensive and in very short supply. Later, when fitted to much larger, heavier, more powerful American cars equipped with a variety of accessories, the fuel economy advantage was significantly reduced (down to 2% to 3%).
Can tire rolling resistance be further reduced?
With the currently used radial tire materials and architecture, tire rolling resistance still can be reduced somewhat. Keep in mind, however, that it cannot be eliminated, for it takes relatively high hysteresis tread compounds to provide good road grip on wet or dry surfaces, as well as good vehicle stability.
It also takes tire deflection (about one inch at equilibrium tire pressure and temperature), with some minimal damping, to protect vehicle components from road surface irregularities and shocks, and provide comfort to vehicle occupants. In addition, it takes proper tire footprint shapes and dimensional proportions (length to width ratio, tread void to solid ratio), as well as proper tread siping design and density, to provide other road/tire/vehicle system desirable functions.
[PAGEBREAK]
How to prove that low rolling resistance tires can reduce vehicle fuel consumption
Test A: Equip a vehicle with new, ordinary, broken-in radial tires, operate the vehicle under normal, real world conditions for a period of three months, and keep a record of the fuel consumed. Repeat the test, using broken-in lower rolling resistance radial tires, and compare the difference in the amounts of fuel consumed.
Test B: With the same vehicle and tires used in test A, conduct comparative vehicle coast-down tests on a smooth, flat road at 45 mph with the transmission in neutral. Record the difference in the distances required for the vehicle to come to a complete stop. The longer the distance, the less the tire drag. Wind velocity and direction should be taken into consideration when conducting coast-down tests.
Test C: With the same vehicle and tires used in tests A and B, record the difference in the amount of carbon dioxide emitted by the test vehicle with ordinary and lower rolling resistance radial tires. The lower the amount of carbon dioxide emission, the better the tire/vehicle system fuel efficiency. Example: 200 grams of carbon dioxide emitted by a passenger car per mile is roughly equivalent to 50 miles per gallon.
Conclusion
Tire rolling resistance and its effect on vehicle fuel efficiency can be measured. The benefit particularly shows up with low mass, low drag, reasonably dimensioned, efficiently powered vehicles, driven fluidly and at reasonable speeds.
All in all, the most effective way to save/conserve energies, including the energies required to produce tire materials and the tires themselves, is by providing consumers not only with low rolling resistance tires with double the tire life, but also by doing so using significantly less tire materials and a more precise, more energy-efficient tire manufacturing process.
However, there is only so much one can squeeze out of radial tires to improve tire/vehicle system fuel efficiency, for the bulk of such efficiency lies in the improvement of vehicles.
Coming up: The next chapter in this series will be on “Tread wear resistance.”
For more than 50 years, Jacques Bajer has championed the cause of tire structural integrity in one way or another. His work with Ford Motor Co., beginning in 1955, led to the creation of a tire uniformity grading machine. In 1964, he almost single-handedly developed low-profile tires for the 1964 Lincoln and Thunderbird. They performed so well that Ford made them standard equipment on all its vehicles the following year.
The French-born engineer also owns a patent for a “casing preparation method” used in producing quality retreaded tires.
He is perhaps best known, however, for radializing the domestic automotive industry. Bajer didn’t invent the radial tire, but when he convinced Ford to offer them as options on its vehicles, the radial tire era began.
Bajer opened his own consulting company, Tire Systems Engineering Inc., in Grosse Point, Mich., in 1970. The firm specializes in the design of advanced manufacturing systems for the economical mass production of tires, power transmission belts, lathe-cut seals and air springs. More than 30 years later, he still stresses the need to analyze the relationship between the vehicle, tire and road. He can be reached at (313) 886-6860.
About the Author
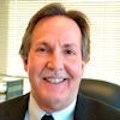
Bob Ulrich
Bob Ulrich was named Modern Tire Dealer editor in August 2000 and retired in January 2020. He joined the magazine in 1985 as assistant editor, and had been responsible for gathering statistical information for MTD's "Facts Issue" since 1993. He won numerous awards for editorial and feature writing, including five gold medals from the International Automotive Media Association. Bob earned a B.A. in English literature from Ohio Northern University and has a law degree from the University of Akron.