Straightening a Bent Wheel: Restoring Structural Integrity Is the Key
If a vehicle wheel is cracked, can it be repaired? The general consensus is no, unless repairing the crack does not compromise the structural integrity of the wheel. It’s not easy to determine that, however.
What if the wheel is bent? Can it be straightened, and put back into service? The answer is yes, again as long as the structural integrity of the wheel is not compromised. That goes for both steel and aluminum alloy wheels, although repairing aluminum alloy wheels is more cost effective (in some cases, it costs less to replace a damaged steel wheel with a new one than it does to repair it).NewArc Tech LLC has a patented process to repair bent wheels that has exceeded SAE wheel and OEM standards. Two well-known suppliers of original equipment wheels, Blackburn OEM Wheel Solutions in Macedonia, Ohio, and EveryRim.com LLC, dba 1-800EveryRim in Santa Fe Springs, Calif., each have had thousands of bent wheels repaired without incident.
Here is what they had to say about wheel repair.
How NewArc works
There are more than 400 NewArc machines repairing bent wheels across the country. According to the NewArc website, a wheel straightened with the NewArc machine “will pass every structural safety test required by the SAE (Society of Automotive Engineers) for new wheels.”
Don Neubauer, who invented the process, says a wheel properly repaired by the process has never failed as a result.
“My patent attorney came up with a unique term. She called it a ‘massage,’ and that’s really a good description. We use controlled heat to make the wheel workable, then hydraulic pressure to push against the damaged portion of the wheel.
“Ken Archibald, my engineering partner, explained to me that when the metal gets bent it’s highly stressed in the area. That’s what we do — we relieve the stress. We do it by using two axes instead of one. We can take those two axes and alternate pressure against the bend. One is at an angle, one is straight, and we can change that angle, and we can also stagger the planes from which the pressure is coming.
“Basically what we’re doing is massaging the area, and relieving the stress by pressing out the bend. This process eliminates the likelihood of a subsequent crack. The dual-axis method provided by this machine is key to the patent.”
The application of heat is crucial, says Neubauer. “You can apply as little as 400 degrees of heat and make a wheel unsafe because you’ve destroyed the heat-treat level. That’s very critical to the SAE. The dual-axis system allows the user to apply as little as 400 degrees of heat for up to two minutes to straighten a wheel. It is known that heating beyond this can soften a wheel.”
How soon the bend in the wheel is treated makes a difference, says Neubauer. “When it’s very fresh it’s easier to straighten. If it’s been driven on awhile, it starts to fatigue. When you put pressure on a fatigued area, it could crack. If it cracks, we take it out of service. We don’t recommend it be welded up. That’s something the SAE has not approved.”
Archibald has been testing and designing steel and aluminum wheels for nearly 40 years. He is a volunteer member of the SAE, and has been on wheel-related SAE task forces for some 35 years. He also oversees some of them.
In addition to being part owner of NewArc Tech, he is owner and president of Independent Test Services (www.wheeltest.com). In that capacity, he has consulted with Alloy Wheel Repair Specialists LLC, and has been called on to provide expert witness testimony.
Independent Test Services is approved to conduct wheel testing for all the major original equipment vehicle manufacturers in North America, and many others around the world.
“I can attest that we used SAE-standard testing to test the wheels repaired by the NewArc machine,” he says. “SAE J328, which represents 98% of the aluminum wheels that are in the marketplace, provides test loads and minimum cycle requirements for cast aluminum wheels. Wheels properly repaired by the NewArc process exceeded the SAE minimum requirements by 2 to 3 times.
“And it isn’t as though they cracked. We just gave up testing because the wheels never cracked. It is very common in the automotive industry to run two to three times the minimum requirement in order to say you have enough margin to ensure that all wheels will be serviceable.”
The repaired wheels also passed Chrysler, Ford and General Motors vehicle test standards, says Archibald.
“This system really does work. It extends the life of a dented wheel. There is no doubt about that. That is bankable. When done properly, with this machine and using Don’s procedure, I’ve never seen an instance where it has jeopardized the serviceability of the wheel.”
Archibald says the deeper the dent, the more likely it will crack before it can be straightened.
“About 80% of dents are around a half-inch deep, plus or minus a quarter. And those can easily be straightened using the NewArc process. It takes more time to repair the one that’s three-quarter inch and less time to repair the quarter inch, but they are recoverable.”
Neubauer says outer cracks are not always visible. “Part of our process is a preliminary inspection. If we find something on the wheel that doesn’t look right when we’re inspecting it, then we do a dye penetrant test using an ultraviolet-light-sensitive material. It is an industry-standard test. For example, the aircraft industry uses it for checking turbine blades in aircraft.
“If a crack is found, that wheel comes out of service. Every one of my machines comes with a dye penetrant kit.
“Once we do a straightening, before we bless the wheel and put it back into service, we have to make sure there are no cracks. If there are no cracks, we can’t do any more than that. We now have restored it to a round condition and it’s uncracked. Scientific evidence this past year has proved if we restore that wheel to a round condition, it’ll pass every SAE structural test for brand new wheels.”OE wheels
Blackburn OEM Wheel Solutions’ inventory is made up of new OE wheels (excess and surplus); new takeoffs; and reconditioned and used “grade A” wheels that are spin tested and inspected. “We buy factory originals from salvage yards, dealers and service companies, but we do not purchase aftermarket wheels,” says co-owner Jimmy Blackburn. “In some cases we sell OE replacement wheels that have the exact specs of the OE wheel.
“If a used wheel comes in, we’re going to spin test and inspect it to make sure it doesn’t have any damage to it whatsoever. Then it’s going to get cleaned and cosmetically restored as best it can be.”
If the wheel is damaged, it is repaired or properly recycled. “These are variables that will scrap a wheel out, making it non-repairable,” he says:
- lug hole distortion,
- valve stem hole distortion,
- damage to the barrel of the wheel,
- wheels that are bent from center,
- wheels that are cracked,
- wheels that are missing material.
“The majority of what is getting repaired today are slight bends. A lot of them can be softly put back into place by applying a little bit of heat and little bit of pressure to the bent area.”
Blackburn OEM Wheels works with various plants that recondition its products depending on the material of origin, nature of the repair and the final finish, says Blackburn. “Each has specs on every OE wheel. They measure each repaired wheel for thickness of the lips and face, trueness and lateral runout, and restore the wheel to those specs.”
Properly repaired wheels are “very well accepted by the whole insurance industry,” he says. “In many cases, the insurance company would prefer a restored wheel over a brand new wheel when replacing a damaged wheel. The wheels that are on the car are already used, and the cost differential is significant.”
Billy Eordekian, owner of 1-800EveryRim, says virtually all insurance company collision repair estimators require that wheels be repaired as the first option. “Many of us ‘original used wheel people’ are surprised that, especially on an older vehicle, we can actually save the insurance company money on a used wheel, yet the insurance company opts for the repaired wheel.”
The company performs simple repairs in house, and sends out the wheels that are “more severely” damaged yet repairable to one of three different vendors depending on their strengths, says Manager Chase Potter.
“During the purchase process, we reject any wheel that is cracked. We also reject most wheels that have severe damage to any machined area because of inevitable cosmetic problems after the repair process, and any wheel that has been welded.”
Adds Eordekian, “Before subbing out, we are extremely careful to check for what would end up being an unsafe or unsuccessful repair as in cracks, lug hole damage, missing lug hole inserts (the metal piece that inserts between the lug nut and the wheel itself), valve hole damage, and center bends where the wheel is bent from the mounting pad.”
1-800EveryRim also grades the wheels for its dealers (see sidebar on page 28). “Grades A+ through B- are wheels that are most popular with tire dealers,” says Eordekian.
Wheels America is one of the companies that repairs and remanufactures wheels for 1-800EveryRim.
“Every wheel goes through the same strict process to ensure the product is not only cosmetically correct, but also structurally safe,” says Scott Stretch, vice president and director of operations for Wheels America. Making the Grade: 1-800EveryRim Codes Repairable Wheels
Here is the general grading scale that 1-800EveryRim will use as the basis for its soon-to-be-rolled-out B2B Extranet system for dealers. (A brief cosmetic description of the wheel is in parentheses.) The company has many more codes that its uses internally for damaged yet repairable wheels.
A+ (New): Brand new wheels, never mounted. No flaws on front or back of wheel.
RECON (Reconditioned): Looks brand new. Wheel has been reconditioned back to manufacturer’s specifications.
A (Like New): Looks brand new but has been mounted. No flaws on face of wheel. What you would expect if you bought a new car from the dealer. May have some brake dust on the back or mounting residue on rim flange.
A- (Very Good): Looks new from a 10-foot distance. Minor scratch on lip at worst, such as a barely noticeable wheel weight mark. Typical new take-off.
B+ (Very Good): Looks new from a 10-foot distance. A few very minor scratches. Imperfections on the center area and or lip area.
B (Good): Noticeable scratches at a 10-foot distance, but just a few. Good at first glance. No major flaws. Bright uniform finish.
B- (Good): Has minor curb scrape, but no missing metal. Otherwise “B” grade. OK for chrome plating with no repair work.
C (Bad): Many scratches and or scrapes and or pits. Bad finish. Very worn wheel. OK for chrome plating, but may not re-chrome well.
D+ (Dinged): Indented metal up to 0.5 inch (one-half inch). Otherwise “B” grade or better. Serviceable. No damage to bead area. Would need repair before chrome plating.
D (Terrible): Indented metal greater than 0.5 inch (one-half inch). Bad finish as “C” grade. Serviceable. No damage on bead area. Would need repair before chrome plating.
Two of the final grades also require work in order to match OE specs: P equals “paint is no match at all to OEM finish, could even be a different color,” and F equals “bent but can be repaired.”
About the Author
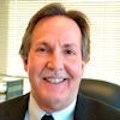
Bob Ulrich
Bob Ulrich was named Modern Tire Dealer editor in August 2000 and retired in January 2020. He joined the magazine in 1985 as assistant editor, and had been responsible for gathering statistical information for MTD's "Facts Issue" since 1993. He won numerous awards for editorial and feature writing, including five gold medals from the International Automotive Media Association. Bob earned a B.A. in English literature from Ohio Northern University and has a law degree from the University of Akron.