As it stands today, there are four types of repairs in the commercial truck tire industry: puncture, spot, reinforcement and section.
A puncture repair can be installed in the field and must be located in the crown area of a truck tire, which is the center of the tread approximately 1 to 1.5 inches in from the edge of tread. Puncture repairs are also limited to a maximum of 3/8 of an inch in diameter. A spot repair is a rubber-only repair on the outside of the tire where an area of missing rubber is replaced without any damage to the body cables or belt wires. When a piece of rubber is missing and the casing is exposed or damaged without actually penetrating the innerliner, a reinforcement repair may be installed. Finally, when the damage exceeds 3/8 of an inch or the injury is located in the shoulder or sidewall area, a section repair is required.
A repair, by definition, restores the original condition of the tire. In order to accomplish this, there are several criteria that must be met.
First of all, the damage must be completely removed. Truck tires are a complex blend of rubber and steel cords, so when an object penetrates the belt package and body plies, the area surrounding the injury is initially weakened to some degree. Since each cord is actually wound like a cable, when it breaks, the cable will continue to unwind. As the cables unwind, the area becomes even more unstable, which often leads to a separation.
Another key step to restoring the original condition with a proper tire repair is to fill the void with rubber. In the case of puncture repairs, this is typically accomplished by installing a cured rubber stem. The stem is coated in cushion gum, which reacts with the vulcanizing cement to chemically cure, or bond, the stem with the tire.
When puncture repairs are installed in a retread plant, un-cured rubber may be used to fill the void with an extruder gun. In these instances, the tire must be placed in a chamber to cure the rubber or the main components of vulcanization (time, temperature and pressure) can be applied with a portable spotter.
In either case, the end result is identical. The void left by the penetrating object is filled with rubber so water and moisture cannot enter the casing which will lead to corrosion and, you guessed it, a separation.
Finally, the innerliner of the tire must be sealed with a repair unit to prevent any further air loss. On puncture repairs, this is accomplished by a universal or reinforced repair unit.
Since the goal is to restore the original condition of the tire following a repair, there is universal agreement on the basic steps and guidelines for all types of repair. However, one particular type of injury continues to be a problem for the truck tire service providers.
Puncture repairs are restricted to the crown area which means simple “nail holes” in the shoulder must be treated as section repairs. This results in a large number of tires and casings being permanently removed from service for a variety of reasons.
First and foremost is the fact that a section repair cannot be installed in the field or on the side of the road. The tools and curing equipment are not readily available in a typical commercial tire service facility, so these tires usually are sent to a retread plant. Then there is the issue of price. A section repair will cost the tire dealer anywhere from $30 to $50. After the markup, the fleet can pay up to $70, which in many cases is almost the price of the casing. These two factors alone are often sufficient to scrap the tire.
[PAGEBREAK]
Mini-sections hybrid
Bob Majewski, president of Sumerel Tire Service Inc. in Newport, Ky., has solved this problem by installing “mini-sections” that are a hybrid of the puncture and section repair processes.
When a simple puncture is located in the shoulder area, they remove the damage with a standard carbide cutter and fill the injury with a cured rubber stem. Then they install a larger repair unit so the edge extends beyond the flex area on the sidewall. And while it doesn’t necessarily conform to the exact repair guidelines established by the truck tire manufacturers, Sumerel Tire has experienced tremendous success with these repairs.
“Most of our fleet customers are reluctant to add another $30 or $40 to the price of a retread for a section repair just because there is a puncture injury in the shoulder,” remarks Majewski. “We got tired of scrapping perfectly good casings, so we started installing mini-sections to repair these tires.
“The damage can be properly removed with a carbide cutter and the cured rubber stem fills the void, so the repair unit on the inside of the tire became the only component that needed to change.
“By installing a larger repair unit that extends to the non-flex area on the lower sidewall, we avoid the problems associated with lifting when the edge rests squarely in the middle of the high flex area. Since there is the possibility that a pencil bulge may become evident on the sidewall of the tire after a mini-section is installed in the shoulder and the tire is inflated, we install a blue triangle patch on the outside of the tire so law enforcement officials will know that the bulge is associated with a repair,” says Majewski.
“We’re able to save a lot of time by avoiding the labor-intensive process of installing a section repair so we can pass those savings on to our customers.”
The way I see it, there is no reason that this practice cannot be extended to the commercial tire service industry. Carbide cutters and cured rubber stems are already used on a daily basis, so larger repair units are the only new components that will be needed. And since most truck tire dealers do not have a supply of blue triangle patches to explain any pencil bulges in the sidewall, tire repairers need to add those as well. Of course, there are other factors that must be considered.
First, before installing a repair unit that extends from the shoulder to the non-flex area of the lower sidewall, the beads of the tire must be relaxed or the repair will bridge and eventually fail. On a well-lit spreader that positions the tire at the ideal working height, it’s not as difficult as it sounds. But when this practice is attempted on the side of the road, there are definitely some challenges that need to be overcome.
Second, technicians must be certain that the damage in the shoulder does not extend beyond the limits of standard puncture repair materials. The belt edge of a radial truck tire is an extremely sensitive area so any technician that installs one of these mini-sections must be positive that all of the damage has been removed.
But the most important factor that must be taken into account is the reality that mini-sections are not currently endorsed by any of the major tire or retread manufacturers.
Sumerel Tire has experienced success with these repairs, but that doesn’t translate into collective success for the rest of the industry. Their repair technicians are well-trained and they have all of the proper equipment to ensure that mini-sections fulfill the objective of restoring the original condition of the tire. Majewski will be the first to admit that every puncture in the shoulder cannot be handled in this manner. There are a lot of factors that must be taken into consideration, including the angle of the injury, the condition of the tire and the final application.
With skyrocketing natural rubber and oil prices, fleets are becoming more willing to accept a repair that falls outside the category of a simple puncture in the crown area. And since the average commercial tire dealer does not have the training, tools or equipment to perform full-blown section repairs in the field, the concept of mini-sections in the shoulder area has the potential to solve a number of problems for all of the parties involved.
However, at the present moment, neither the Rubber Manufacturers Association (RMA) nor the Tire Industry Association (TIA) recognizes these repairs, so they remain outside the mainstream. While I cannot comment on the RMA position, I can say that TIA will follow the lead of the tire and retread manufacturers when it comes to the installation of mini-sections.
Unfortunately, the inherent risks that accompany all types of tire repair make engineering and legal departments reluctant to step outside the box. Without conclusive data that universally supports the practice of using a mini-section to repair a simple puncture in the shoulder of a radial truck tire, these injuries will continue to result in a section repair or a scrap tire. And since we know that at least one retreader is having success, I believe that the alternative of improperly repairing puncture injuries in the shoulder creates even more risk for everyone.
Regardless, the industry is changing at a rapid pace, so the pressure to keep tires and casings in service for as long as possible should be enough for RMA and the truck tire manufacturers to at least consider the possibility of gathering the necessary data so the industry has an answer one way or another. ■
Kevin Rohlwing is senior vice president of training for the Tire Industry Association (e-mail [email protected]).
About the Author
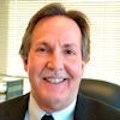
Bob Ulrich
Bob Ulrich was named Modern Tire Dealer editor in August 2000 and retired in January 2020. He joined the magazine in 1985 as assistant editor, and had been responsible for gathering statistical information for MTD's "Facts Issue" since 1993. He won numerous awards for editorial and feature writing, including five gold medals from the International Automotive Media Association. Bob earned a B.A. in English literature from Ohio Northern University and has a law degree from the University of Akron.